Which Part Of A Belt Driven Non Hermetic Compressor
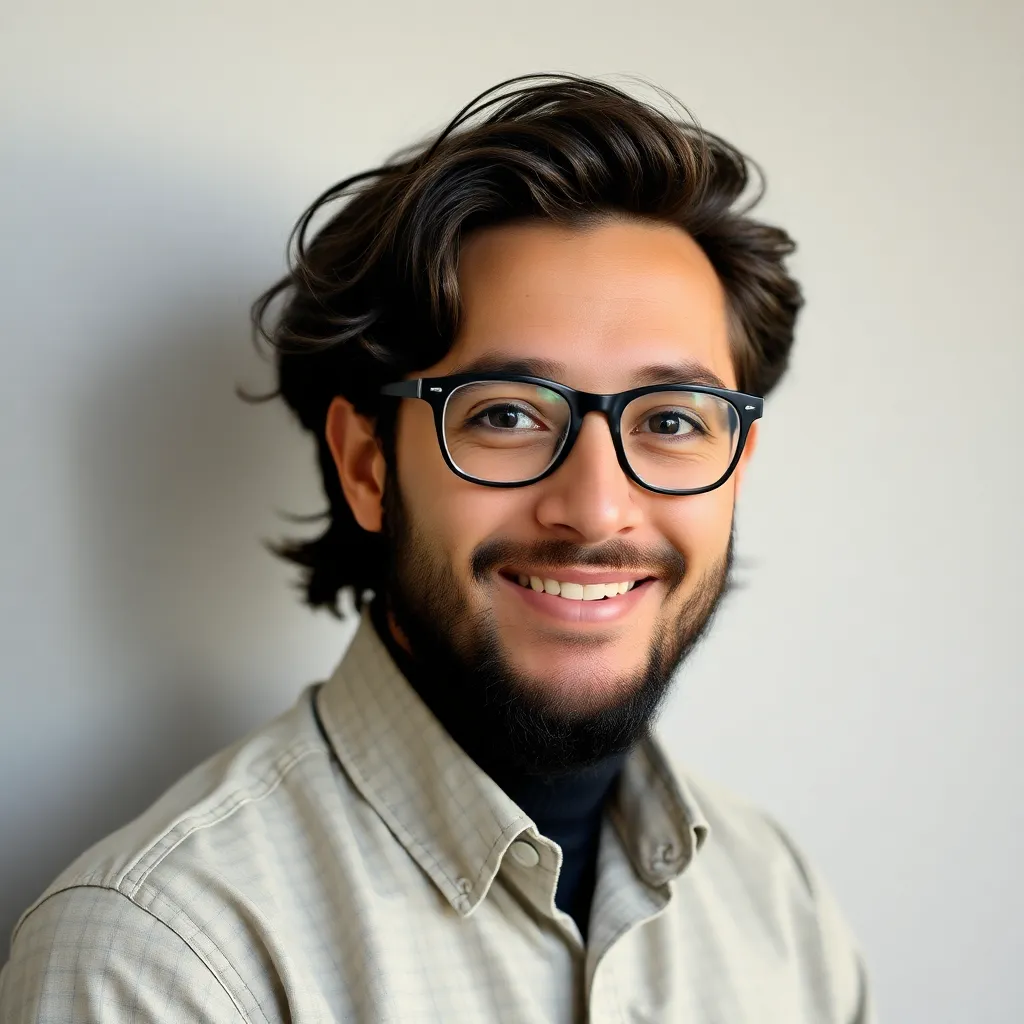
Breaking News Today
Apr 04, 2025 · 5 min read
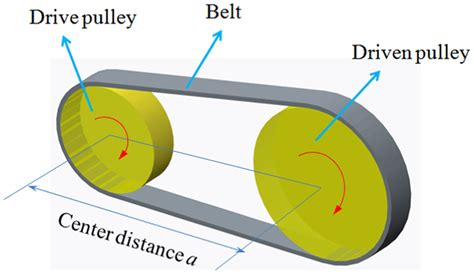
Table of Contents
Decoding the Anatomy of a Belt-Driven Non-Hermetic Compressor: A Deep Dive into its Components
Belt-driven non-hermetic compressors are workhorses in various refrigeration and air conditioning systems. Understanding their intricate components is crucial for effective maintenance, troubleshooting, and efficient system operation. This comprehensive guide delves into each part, exploring its function, potential issues, and overall significance within the system.
The Heart of the System: The Compressor Cylinder
The compressor cylinder is the central chamber where the refrigerant undergoes compression. This is arguably the most critical component, as its integrity directly impacts the entire system's performance.
Piston and Piston Rings:
The piston, driven by the crankshaft, moves within the cylinder, compressing the refrigerant vapor. The piston rings create a seal between the piston and the cylinder wall, preventing refrigerant leakage and maintaining compression efficiency. Worn piston rings are a common cause of reduced efficiency and increased power consumption. They can also lead to increased oil consumption and potential compressor failure.
Cylinder Liner:
The cylinder liner is the inner wall of the cylinder. It provides a smooth, wear-resistant surface for the piston to move against. Scratches or damage to the cylinder liner can lead to reduced efficiency and eventual compressor failure. Regular maintenance and careful handling during repairs are vital to protecting its integrity.
Connecting Rod:
The connecting rod links the piston to the crankshaft, transmitting the reciprocating motion of the piston to the rotational motion of the crankshaft. A bent or damaged connecting rod will severely impair the compressor's function and may result in catastrophic failure. This is often a symptom of a more serious underlying issue.
Power Transmission: Crankshaft, Belts, and Pulleys
The energy needed to compress the refrigerant is transferred to the crankshaft, which, in turn, drives the piston. This process involves a series of interconnected components.
Crankshaft:
The crankshaft converts the reciprocating motion of the piston into rotational motion, driving the system's pulleys and belts. Wear and tear, bearing failure, or imbalances in the crankshaft can lead to vibrations, noise, and eventual failure. Regular lubrication and proper alignment are crucial for its longevity.
Drive Belt:
The drive belt transfers power from the motor to the compressor's pulley. Cracks, fraying, or slippage of the drive belt significantly reduce power transmission efficiency. Regular belt inspection and replacement are essential for maintaining optimal system performance.
Compressor Pulley:
The compressor pulley receives power from the drive belt and transfers it to the crankshaft. A damaged or misaligned pulley can lead to slippage, reduced efficiency, and premature wear on the belt. Proper alignment and regular inspection are important preventative measures.
Suction and Discharge: Valves and Ports
The efficient flow of refrigerant into and out of the compressor cylinder is critical for optimal performance. This involves precisely engineered valves and ports.
Suction Valve:
The suction valve allows refrigerant vapor to enter the cylinder from the evaporator. A malfunctioning suction valve, whether stuck open or closed, severely impacts the compressor's ability to build pressure. This often leads to reduced cooling capacity or system failure.
Discharge Valve:
The discharge valve allows the compressed, high-pressure refrigerant to exit the cylinder and head towards the condenser. A faulty discharge valve, similar to a suction valve failure, can have catastrophic consequences, leading to high-pressure build-up and potential system damage.
Suction and Discharge Ports:
These ports connect the valves to the internal passages of the compressor, facilitating the flow of refrigerant. Obstructions or damage in these ports will hinder refrigerant flow, leading to compromised performance. Regular maintenance, specifically ensuring clean and free-flowing ports, helps prevent problems.
Lubrication System: Oil and its Management
Lubrication is crucial for the longevity and efficient operation of the compressor. The oil plays a vital role in reducing friction, preventing wear, and facilitating heat dissipation.
Oil Pump (if present):
Some belt-driven non-hermetic compressors incorporate oil pumps to ensure proper lubrication. The oil pump's role is to circulate the oil within the compressor, reaching all moving parts. A failing oil pump compromises the lubrication system, leading to increased wear and premature failure.
Oil Reservoir:
The oil reservoir stores the lubricating oil. Insufficient oil levels or contamination of the oil can quickly damage the compressor components. Regular oil level checks and oil changes are essential for preserving the compressor's health.
Mounting and External Components: Protecting the Heart
The entire compressor assembly is housed in a robust structure designed to protect the inner components. There are several external components that contribute to this protection and overall functionality.
Motor Mount:
The motor mount secures the motor to the compressor, providing stability and reducing vibrations. A worn or damaged motor mount leads to excessive vibrations, potentially damaging other components. Regular inspection and replacement when necessary are important maintenance tasks.
Compressor Housing:
The compressor housing encloses and protects the inner components from the environment. Cracks or damage to the housing can lead to oil leaks and exposure of internal components to contaminants.
Troubleshooting Common Issues
Recognizing common issues and their potential causes is crucial for timely maintenance and repairs.
-
Reduced Cooling Capacity: This could be due to low refrigerant charge, a faulty compressor, problems with the expansion valve, or a dirty condenser coil.
-
Excessive Noise or Vibration: This could indicate worn bearings, a loose mounting bracket, imbalances in the crankshaft, or a worn drive belt.
-
Oil Leaks: Oil leaks can stem from damaged seals, cracks in the compressor housing, or a faulty oil pump.
-
High Pressure Switch Activation: This often signals a problem with the compressor, condenser, or refrigerant flow.
Conclusion
Understanding the intricate workings of each part of a belt-driven non-hermetic compressor is essential for maintaining its efficiency and preventing premature failure. By conducting regular inspections, performing timely maintenance, and recognizing common issues, you can ensure the long-term reliability of your refrigeration or air conditioning system, minimizing downtime and maximizing its lifespan. Regular attention to detail in each component's function is key to preserving its overall effectiveness and preventing costly repairs. Investing in preventative maintenance will always prove more economical in the long run than emergency repairs.
Latest Posts
Latest Posts
-
Reactions Of Metals With Solutions Of Metal Ions
Apr 10, 2025
-
A Cross Connection Is A Link Between Servsafe
Apr 10, 2025
-
What Document Explains Your Rights And Res
Apr 10, 2025
-
Label The Locations Of Different Arterial Pulse Sites
Apr 10, 2025
-
Figurative Language In I Have A Dream Speech
Apr 10, 2025
Related Post
Thank you for visiting our website which covers about Which Part Of A Belt Driven Non Hermetic Compressor . We hope the information provided has been useful to you. Feel free to contact us if you have any questions or need further assistance. See you next time and don't miss to bookmark.