A Compact Disc Manufacturer Wanted To Determine
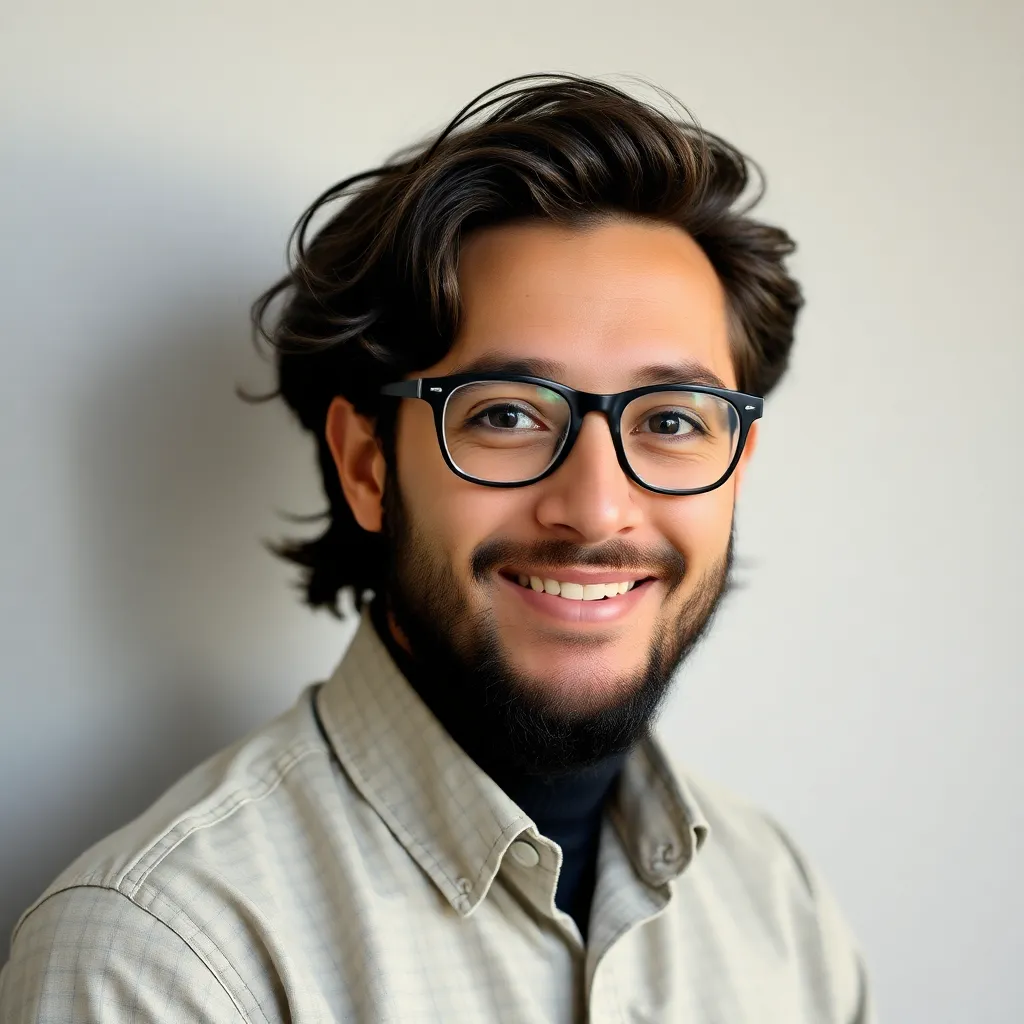
Breaking News Today
Apr 11, 2025 · 5 min read

Table of Contents
A Compact Disc Manufacturer Wanted to Determine: Optimizing Production for Maximum Profit
The world of compact discs (CDs) may seem like a relic of the past in our streaming-dominated era. However, niche markets persist, and for a CD manufacturer, understanding production optimization is crucial for survival and profitability. Let's imagine a compact disc manufacturer who wants to determine the optimal production levels to maximize profit. This scenario presents a rich opportunity to explore several key business concepts, including cost analysis, demand forecasting, and profit maximization.
Understanding the Cost Structure
Before diving into profit maximization, the manufacturer needs a clear picture of its cost structure. This typically involves two main categories:
1. Fixed Costs:
These are expenses that remain constant regardless of the number of CDs produced. Examples include:
- Rent for the manufacturing facility: This cost remains the same whether the factory produces 100 or 10,000 CDs.
- Salaries of permanent employees: The manufacturer's administrative staff and core production team have consistent salaries.
- Depreciation of machinery: The value of the CD pressing machines diminishes over time, regardless of production volume.
- Insurance and property taxes: These are fixed annual expenses.
2. Variable Costs:
These are expenses that change directly with the number of CDs produced. They include:
- Cost of raw materials: This includes the plastic for the CD cases, the aluminum for the discs themselves, and the ink for printing. The more CDs produced, the higher this cost.
- Direct labor costs (for additional workers): If production surpasses the capacity of permanent staff, the manufacturer may hire temporary workers, incurring additional labor costs.
- Packaging costs: Boxes, inserts, and other packaging materials directly correlate with the number of CDs produced.
- Utilities (electricity, water): While some base utility costs are fixed, the energy consumed for production will increase with higher output.
Calculating Total Cost: The total cost (TC) of producing CDs is the sum of fixed costs (FC) and variable costs (VC): TC = FC + VC. A precise calculation necessitates detailed financial records and analysis of historical data.
Analyzing Demand and Revenue
Understanding the demand for CDs is equally important. The manufacturer needs to estimate the number of CDs they can realistically sell at various price points. This involves:
1. Market Research:
This could include surveys, focus groups, and analysis of competitor pricing and sales. Understanding the target audience, their preferences, and price sensitivity is crucial. The manufacturer might consider specializing in niche markets like limited-edition releases, collectors' items, or specific musical genres to reduce competition.
2. Demand Function:
Based on market research, the manufacturer can develop a demand function (Q = f(P)), which describes the relationship between the price (P) of a CD and the quantity demanded (Q). This function typically shows an inverse relationship: as the price increases, the quantity demanded decreases. Different demand curves may reflect different market conditions (e.g., during peak holiday seasons).
3. Revenue Generation:
Total revenue (TR) is calculated by multiplying the price (P) by the quantity sold (Q): TR = P * Q. The manufacturer needs to find the price point that maximizes revenue without significantly reducing the quantity sold.
Maximizing Profit
The ultimate goal is to maximize profit, which is the difference between total revenue (TR) and total cost (TC): Profit = TR - TC. Several approaches can be used to find the optimal production level that yields maximum profit:
1. Break-Even Analysis:
This helps determine the minimum quantity of CDs that must be sold to cover all costs. The break-even point occurs when TR = TC. Production beyond this point generates profit.
2. Marginal Analysis:
This involves analyzing the change in cost and revenue resulting from producing one additional CD. Marginal cost (MC) is the cost of producing one more CD, and marginal revenue (MR) is the revenue generated from selling one more CD. Profit maximization occurs where MR = MC. Producing beyond this point will lead to diminishing returns.
3. Graphical Analysis:
Plotting the total revenue and total cost curves on a graph can visually identify the profit-maximizing production level. The maximum profit occurs where the vertical distance between the TR and TC curves is the greatest.
Incorporating External Factors
The CD manufacturer needs to consider external factors affecting their profitability:
1. Technological advancements:** The rise of digital music has significantly impacted the CD market. The manufacturer might need to adapt by exploring innovative technologies, like high-quality audio CDs or specialized packaging to retain customers.
2. Competition:** The manufacturer needs to monitor competitors' pricing strategies, production volumes, and market share. Understanding the competitive landscape will inform pricing and production decisions.
3. Economic conditions:** Fluctuations in the economy may affect consumer spending and demand for CDs. The manufacturer may need to adjust its production levels to respond to economic downturns or booms.
4. Material costs:** Changes in the prices of raw materials (plastic, aluminum, etc.) will directly influence production costs. The manufacturer needs to monitor material prices and consider hedging strategies to mitigate price volatility.
5. Supply chain disruptions:** Unexpected events like natural disasters or geopolitical instability can disrupt the supply chain, affecting the availability of raw materials and causing production delays.
Continuous Improvement and Data Analysis
To continuously optimize production and maximize profit, the manufacturer needs to implement a robust data analysis system. This involves:
- Regular cost accounting: Tracking all costs (fixed and variable) to identify areas for potential savings.
- Sales data analysis: Monitoring sales trends, customer preferences, and market demand to inform production planning.
- Inventory management: Optimizing inventory levels to minimize storage costs and prevent stockouts.
- Quality control: Ensuring consistent product quality to maintain customer satisfaction and minimize waste.
- Process improvement: Continuously evaluating and improving manufacturing processes to increase efficiency and reduce costs.
Conclusion
Optimizing the production of compact discs requires a multifaceted approach that balances cost analysis, demand forecasting, and a deep understanding of the market. By carefully considering fixed and variable costs, developing a strong understanding of demand, and using tools like break-even analysis and marginal analysis, the CD manufacturer can pinpoint the production level that maximizes profit. Furthermore, continuous monitoring of external factors and implementation of a data-driven approach are vital for long-term success in this evolving market. The ability to adapt to changing consumer preferences, technological advancements, and economic conditions will ultimately be crucial for survival and profitability in the competitive world of CD manufacturing.
Latest Posts
Latest Posts
-
What Is Not A Component Of Biodiversity
Apr 18, 2025
-
Hide The Column Showing 2019 Data And The Bonus Rate
Apr 18, 2025
-
Activated Cd8 Cells Form A Clone Of Blank Cells
Apr 18, 2025
-
Create An Automatic Basic Report From The Classes Table
Apr 18, 2025
-
You Are Calling Mrs Jones In Regards To An Adherence
Apr 18, 2025
Related Post
Thank you for visiting our website which covers about A Compact Disc Manufacturer Wanted To Determine . We hope the information provided has been useful to you. Feel free to contact us if you have any questions or need further assistance. See you next time and don't miss to bookmark.