A Wire Rope Sling With A Strength Of 10 000
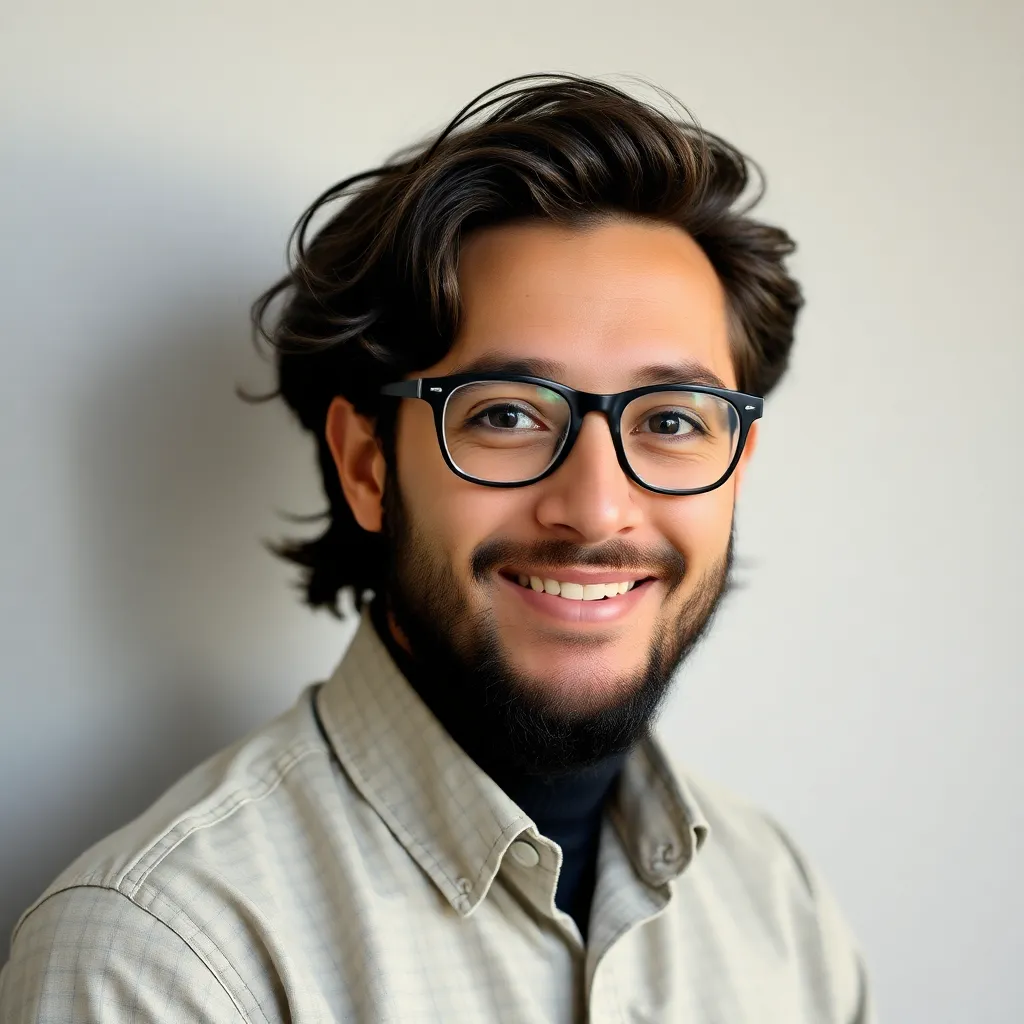
Breaking News Today
Mar 17, 2025 · 6 min read
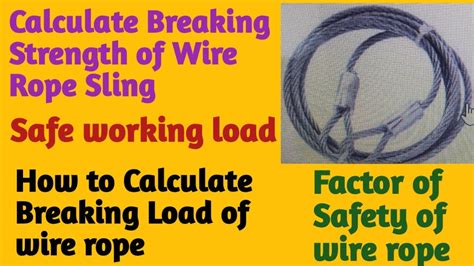
Table of Contents
A 10,000-Pound Capacity Wire Rope Sling: A Deep Dive into Strength, Safety, and Application
Wire rope slings are indispensable tools in heavy lifting operations, offering superior strength and durability compared to other lifting alternatives. Understanding the specifics of a high-capacity sling, such as a 10,000-pound capacity wire rope sling, is crucial for ensuring safe and efficient material handling. This comprehensive guide delves into the intricacies of these robust lifting devices, covering their construction, safety regulations, applications, and maintenance procedures.
Understanding the Strength of a 10,000-Pound Wire Rope Sling
A 10,000-pound capacity wire rope sling signifies its Working Load Limit (WLL). This critical value represents the maximum safe load the sling can bear under normal operating conditions. It's crucial to never exceed the WLL, as doing so dramatically increases the risk of catastrophic failure. The 10,000-pound capacity suggests the sling is designed for heavy-duty applications involving significant weight and strain. This capacity is achieved through a combination of factors:
Factors Contributing to High Capacity:
- Wire Material and Construction: High-tensile strength steel wires are used, carefully constructed into strands and then ropes, creating a robust and durable structure capable of withstanding immense forces. The specific construction (e.g., number of wires per strand, number of strands per rope) directly influences the overall strength.
- Diameter and Length: A thicker diameter wire rope provides greater strength and load-bearing capacity. The length of the sling is also a factor; longer slings can experience more elongation under load, potentially affecting their strength and safety.
- Lay and Configuration: The lay (direction of the twisting of the wires and strands) and the sling's configuration (e.g., single-leg, two-leg, three-leg, four-leg) directly impact its load distribution and overall strength. Multiple-leg slings distribute the weight across several points, increasing stability and reducing stress on individual components.
- Quality Control and Manufacturing: Reputable manufacturers adhere to stringent quality control standards throughout the production process, ensuring the sling meets its specified capacity and complies with relevant safety regulations.
Safety Regulations and Standards for Wire Rope Slings
The safe operation of a 10,000-pound wire rope sling is paramount. Several industry standards and regulations govern their use, including but not limited to:
- OSHA (Occupational Safety and Health Administration): OSHA regulations in the United States dictate strict guidelines for lifting equipment, including wire rope slings. These regulations cover aspects like inspection, maintenance, and safe operating procedures. Failure to comply can result in significant penalties.
- ASME (American Society of Mechanical Engineers): ASME standards provide technical specifications for the design, manufacturing, and testing of lifting equipment, including wire rope slings. These standards ensure consistency and quality in the manufacturing process.
- EN (European Norms): Similar standards exist in Europe and other parts of the world, guaranteeing that slings meet minimum safety and performance requirements.
- Manufacturer's Recommendations: Always consult the manufacturer's instructions and recommendations for safe use, inspection, and maintenance. These guidelines provide crucial information specific to the sling's design and materials.
Inspection and Maintenance:
Regular inspection of the 10,000-pound wire rope sling is vital for preventing accidents. Look for signs of:
- Broken or damaged wires: Even a few broken wires can significantly reduce the sling's strength.
- Corrosion or rust: Corrosion weakens the steel wires, compromising their structural integrity.
- Kinking or crushing: These deformations concentrate stress on specific areas, increasing the risk of failure.
- Excessive wear: General wear and tear over time can gradually diminish the sling's capacity.
- Abrasions: Friction and abrasion can damage the outer wires, reducing their strength.
- Heat damage: Exposure to extreme heat can weaken the steel and reduce the sling's capacity.
Regular inspections should be performed before each use. If any damage is detected, the sling must be immediately removed from service and replaced. Regular maintenance, which may include lubrication to reduce friction and wear, extends the lifespan of the sling.
Applications of a 10,000-Pound Wire Rope Sling
The high capacity of a 10,000-pound wire rope sling makes it suitable for various demanding lifting tasks in several industries:
Construction:
- Lifting heavy construction materials: Steel beams, precast concrete elements, and large machinery are frequently lifted using high-capacity slings.
- Erection of structures: In high-rise building construction, these slings are indispensable for hoisting heavy components.
- Demolition work: Controlled demolition often involves the careful removal of large sections of structures, requiring robust and reliable lifting equipment.
Manufacturing:
- Moving heavy machinery and equipment: Industrial plants and manufacturing facilities rely on such slings for transporting and positioning heavy equipment during installation or maintenance.
- Handling large components: Automotive manufacturing, aerospace, and shipbuilding industries utilize these slings for manipulating large and heavy parts.
Transportation and Logistics:
- Loading and unloading cargo: Ports and shipping terminals use high-capacity slings for handling heavy containers and goods.
- Transporting oversized loads: Specialized transportation operations often rely on these slings for securing and transporting unusually large and heavy items.
Other Applications:
- Mining and quarrying: Lifting and transporting large rocks and minerals.
- Oil and gas: Handling heavy equipment and components in offshore and onshore operations.
- Renewable energy: Installation of wind turbine components.
Choosing the Right Sling Configuration
The selection of the appropriate sling configuration depends on the specific lifting task and the nature of the load:
- Single-leg slings: Simple and efficient for lifting loads with a single point of attachment.
- Two-leg slings: Provide better stability and load distribution, suitable for lifting loads that are not perfectly symmetrical. The angle between the legs influences the load on each leg.
- Three-leg slings: Offer even greater stability and load distribution for heavy and potentially unstable loads.
- Four-leg slings: Used for lifting extremely heavy and bulky loads, providing maximum stability and support.
Proper rigging techniques are essential to ensure safe and efficient lifting. The angle of the sling legs should be carefully considered to avoid exceeding the WLL of the individual legs. A sling angle that is too shallow increases the load on each leg.
Factors Influencing Sling Selection Beyond Capacity
While a 10,000-pound WLL is significant, other factors influence sling selection:
- Type of sling: Wire rope slings come in different constructions (e.g., 6x19, 6x37) offering varying flexibility and resistance to abrasion.
- Fittings: Choosing the correct end fittings (e.g., hooks, eyes, shackles) is crucial for secure attachment to the load and lifting mechanism. Ensure the fittings are rated for the load being lifted.
- Environmental conditions: The sling's material must be suitable for the operating environment. Slings used in corrosive environments may require specialized coatings or materials.
- Load characteristics: Consider the load's shape, size, weight distribution, and potential for shifting during lifting. The sling should be appropriate for the load's characteristics.
Conclusion
A 10,000-pound capacity wire rope sling is a powerful and essential tool in heavy lifting operations. However, its safe and efficient utilization requires a thorough understanding of its capabilities, limitations, and the relevant safety regulations. Prioritizing regular inspections, proper maintenance, and adherence to best practices is crucial for preventing accidents and ensuring the longevity of the sling. By carefully considering the factors discussed in this guide, you can make informed decisions when selecting and utilizing these high-capacity lifting devices, leading to safer and more productive operations. Remember, the safety of personnel and equipment is paramount. Always prioritize safety when working with heavy lifting equipment.
Latest Posts
Latest Posts
-
The Direct Carry Is Used To Transfer A Patient
Mar 18, 2025
-
The Emancipation Proclamation Of January 1 1863 Quizlet
Mar 18, 2025
-
These Cards Will Get You Drunk Quizlet
Mar 18, 2025
-
Did Quizlet Get Rid Of Q Chat
Mar 18, 2025
-
Myasthenia Gravis Is An Autoimmune Disease In Which Quizlet
Mar 18, 2025
Related Post
Thank you for visiting our website which covers about A Wire Rope Sling With A Strength Of 10 000 . We hope the information provided has been useful to you. Feel free to contact us if you have any questions or need further assistance. See you next time and don't miss to bookmark.