____ Are Usually Either Hydraulic Or Flywheel Operated.
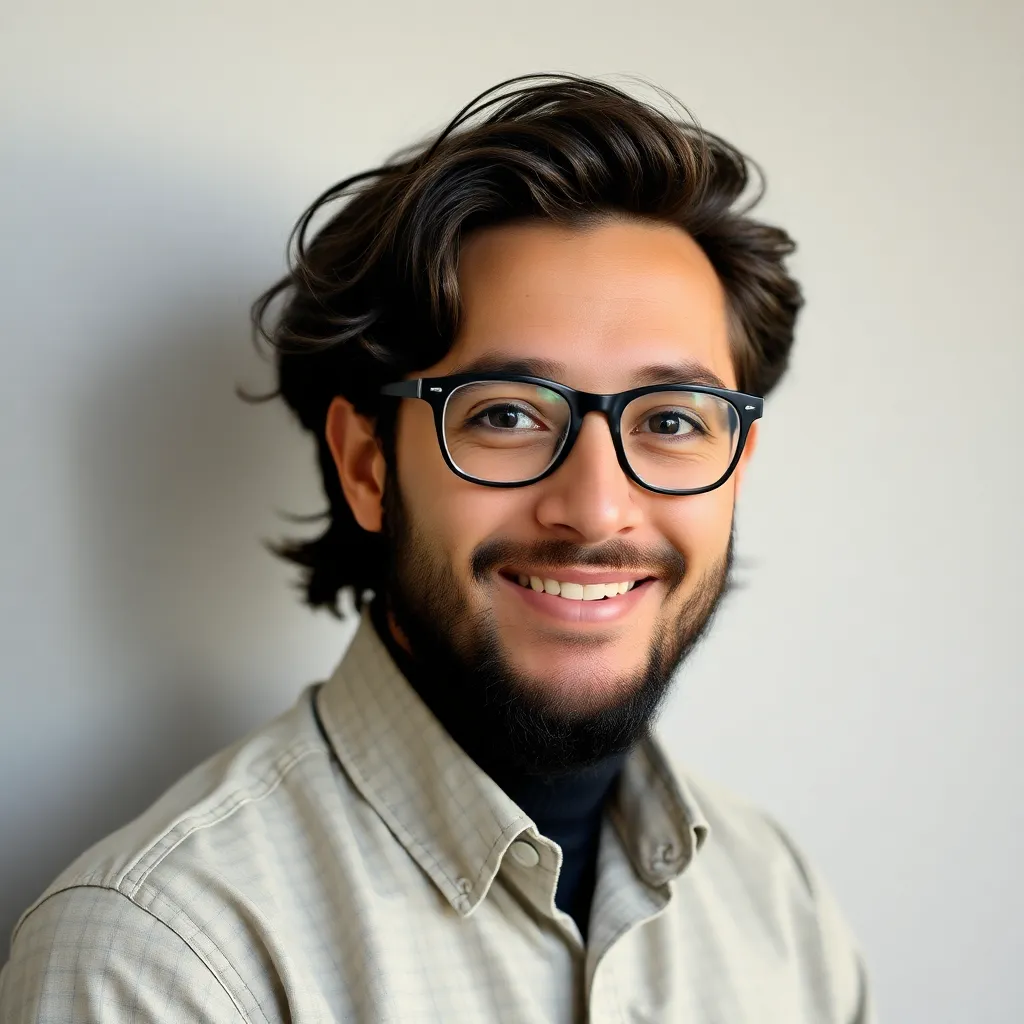
Breaking News Today
Mar 14, 2025 · 7 min read
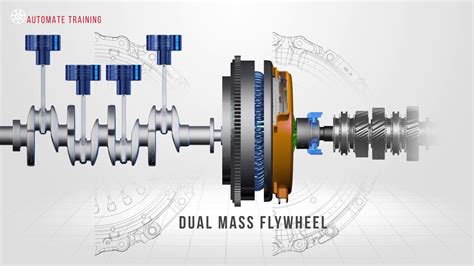
Table of Contents
Heavy-Duty Industrial Brakes: Hydraulic and Flywheel Systems Explained
Heavy-duty industrial brakes are critical safety components in various applications, from cranes and excavators to wind turbines and mining equipment. These brakes are tasked with stopping and holding massive loads, often under extreme conditions. They are usually either hydraulic or flywheel operated, each with its unique strengths and weaknesses. This article delves deep into the workings, advantages, disadvantages, and applications of both hydraulic and flywheel braking systems, providing a comprehensive understanding for engineers, technicians, and anyone interested in heavy-duty industrial machinery.
Understanding Hydraulic Brakes in Heavy-Duty Applications
Hydraulic brakes leverage the power of pressurized fluid to generate braking force. In a heavy-duty industrial context, this system utilizes a hydraulic pump, a network of pipes and hoses, and actuators (cylinders) to engage the braking mechanism. Let's break down the key components:
1. Hydraulic Pump: The Heart of the System
The hydraulic pump is the powerhouse, responsible for generating the high-pressure fluid needed to actuate the brakes. Different pump types exist, including gear pumps, vane pumps, and piston pumps, each offering varying levels of efficiency and pressure capabilities. The choice of pump depends on the specific application's demands for flow rate and pressure.
2. Control Valves: Precision and Safety
Control valves regulate the flow of hydraulic fluid, controlling the braking force and providing precise control. These valves can be mechanically operated (lever or pedal activated), electrically controlled (solenoids), or even electronically managed by sophisticated control systems. Safety features, such as pressure relief valves and emergency shut-off valves, are crucial to prevent system failures and accidents.
3. Hydraulic Actuators: Converting Pressure to Force
Hydraulic actuators, typically cylinders, transform the hydraulic pressure into mechanical force. The piston within the cylinder moves when pressurized fluid enters, causing a mechanical linkage to engage the braking mechanism – often a set of brake shoes or discs. The size and design of the actuator are directly related to the braking force required.
4. Brake Mechanism: Engaging the Stopping Power
The actual braking mechanism interacts directly with the moving parts needing to be stopped. This could involve clamping brake shoes against a rotating drum (drum brakes) or squeezing brake pads against a rotating disc (disc brakes). The design of the brake mechanism is critical for heat dissipation, as heavy-duty braking generates substantial heat.
Advantages of Hydraulic Braking Systems:
- High Force Generation: Hydraulic systems can generate immense braking forces with relatively compact components.
- Precise Control: Control valves allow for precise modulation of braking force, crucial for delicate operations.
- Relatively Simple Design: While sophisticated in their control systems, the basic hydraulic principles are relatively straightforward.
- Remote Actuation: Hydraulic systems can easily be designed for remote operation, especially advantageous in large machinery.
Disadvantages of Hydraulic Braking Systems:
- Potential for Leaks: Hydraulic systems rely on sealed components; leaks can lead to loss of braking power, posing significant safety risks.
- Maintenance Requirements: Regular maintenance, including fluid changes and inspection of components for leaks and wear, is crucial.
- Environmental Concerns: Hydraulic fluids can be harmful to the environment, requiring careful handling and disposal.
- Susceptibility to Contamination: Contamination of hydraulic fluid can significantly impair system performance.
Understanding Flywheel Brakes in Heavy-Duty Applications
Flywheel brakes utilize the stored kinetic energy of a rotating flywheel to create braking force. They are often employed in situations requiring high braking torque for short durations, especially where space constraints or the need for a self-contained system is a major factor. The key components include:
1. Flywheel: The Energy Storage Unit
The flywheel is a massive, precisely balanced disc or wheel designed to store kinetic energy during operation. The flywheel's rotational speed increases as the machine accelerates. The material and design of the flywheel determine its capacity to store energy, affecting the braking power.
2. Friction Mechanism: Transforming Kinetic to Braking Energy
The friction mechanism is what converts the flywheel’s rotational energy into braking force. This typically involves a system of brake shoes or pads that clamp against the flywheel's rim or a surface connected to it. The intensity of the braking is determined by the clamping force applied to the friction surfaces.
3. Actuation Mechanism: Engaging the Braking Force
The actuation mechanism is responsible for applying the clamping force to the friction surfaces. This could be mechanical (lever, spring, or weight-activated), hydraulic (using a hydraulic cylinder to press the brake shoes), or even electromagnetic (using electromagnets to generate the clamping force).
4. Energy Dissipation: Managing the Heat
Flywheel braking generates significant heat. Efficient energy dissipation is crucial to prevent overheating and damage to the braking components. This might involve passive cooling (through radiation and convection) or active cooling (using fans or cooling systems).
Advantages of Flywheel Braking Systems:
- High Torque for Short Durations: Flywheel brakes excel at delivering high braking torque over short periods.
- Self-Contained System: They are often self-contained, requiring minimal external power sources.
- No External Fluid Lines: Eliminates the risk of fluid leaks associated with hydraulic systems.
- Reliability in Harsh Environments: Can be more robust and reliable in demanding and harsh conditions.
Disadvantages of Flywheel Braking Systems:
- Limited Continuous Braking: Flywheel brakes are not suitable for continuous or extended braking; they need time to recharge their stored energy.
- Higher Initial Cost: The design and manufacturing of a high-capacity flywheel can be expensive.
- Size and Weight: Flywheels are typically large and heavy, requiring substantial space and robust mounting structures.
- Potential for Runaway: System failures can lead to an uncontrolled release of stored energy.
Comparing Hydraulic and Flywheel Brake Systems
Choosing between hydraulic and flywheel braking systems hinges on the specific demands of the application. Here's a comparative overview:
Feature | Hydraulic Brakes | Flywheel Brakes |
---|---|---|
Braking Force | High, continuous | Very high, short duration |
Control | Precise, adjustable | Less precise, often on/off |
Maintenance | Requires regular fluid changes & checks | Less frequent maintenance |
Size & Weight | Relatively compact | Typically larger and heavier |
Cost | Moderate | Higher initial cost |
Applications | Cranes, excavators, vehicles | Presses, shears, emergency brakes |
Environmental | Potential fluid leaks & disposal issues | Environmentally benign |
Safety | Potential for fluid leaks | Potential for runaway if it fails |
Applications of Hydraulic and Flywheel Brakes
Both hydraulic and flywheel braking systems find their place in diverse heavy-duty applications:
Hydraulic Brakes are commonly used in:
- Cranes and Hoists: Providing precise control for lifting and lowering heavy loads.
- Excavators and Construction Equipment: Ensuring safe and controlled operation during digging and movement.
- Mining Equipment: Stopping and holding heavy machinery in challenging environments.
- Vehicles (Heavy Trucks, Buses): Stopping power for large and heavy vehicles.
- Wind Turbines: Controlling the rotation of turbine blades during emergency shutdowns.
Flywheel Brakes are commonly used in:
- Presses and Shears: Delivering high braking torque for rapid stops in metalworking machinery.
- Emergency Braking Systems: Providing a backup braking system in case of hydraulic or other system failures.
- Conveyors: Bringing conveyor belts to a quick and controlled halt.
- Rolling Mills: Controlling the speed and stopping of heavy rollers in steel production.
- High-speed machinery: Providing instantaneous braking in applications requiring rapid stops.
Conclusion
Selecting the appropriate braking system for heavy-duty applications necessitates a thorough understanding of the specific operational needs, environmental factors, and safety requirements. Both hydraulic and flywheel brakes offer unique advantages and disadvantages. While hydraulic brakes offer precise, continuous control and high braking force for a wide variety of applications, flywheel brakes provide exceptionally high torque for short durations, making them suitable for specific high-impact scenarios. A careful evaluation of these factors ensures the selection of a reliable and safe braking system crucial for operational efficiency and safety in heavy-duty industrial machinery. Thorough maintenance and regular inspections for both systems are critical for ensuring continued safe operation.
Latest Posts
Latest Posts
-
Based On The Texts How Would Graeber And Wengrow
Mar 15, 2025
-
A Nail Salon Pays 2500 In Rent
Mar 15, 2025
-
What Are The Central Ideas In A Play
Mar 15, 2025
-
In Most Spanish Speaking Countries Married Women Legally
Mar 15, 2025
-
The Fed May Respond To A Recession By
Mar 15, 2025
Related Post
Thank you for visiting our website which covers about ____ Are Usually Either Hydraulic Or Flywheel Operated. . We hope the information provided has been useful to you. Feel free to contact us if you have any questions or need further assistance. See you next time and don't miss to bookmark.