Firms Are Motivated To Minimize Production Costs Because
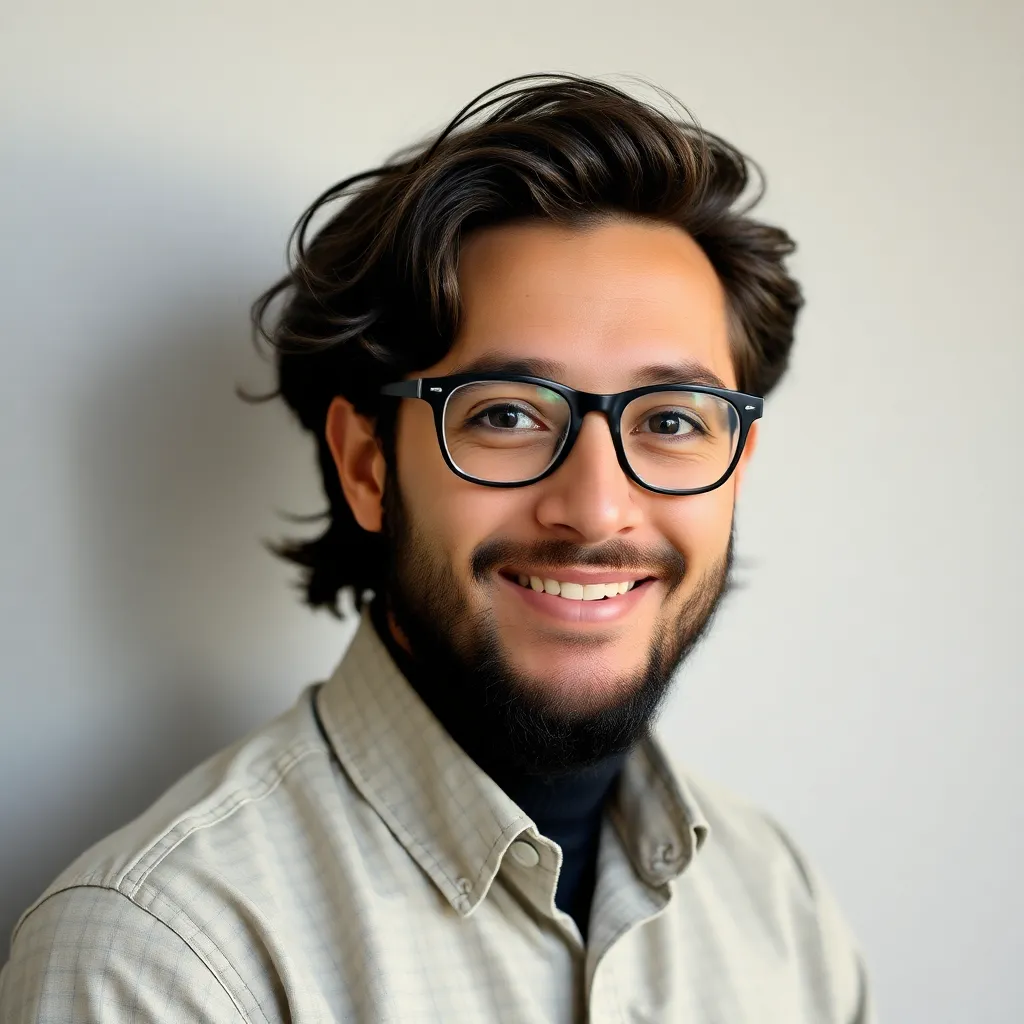
Breaking News Today
Apr 01, 2025 · 6 min read
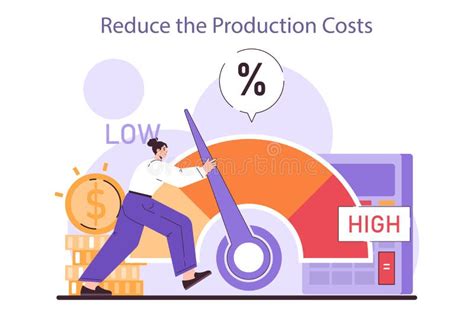
Table of Contents
Firms are Motivated to Minimize Production Costs Because… Profit Maximization!
Firms, regardless of size or industry, operate with a fundamental objective: profit maximization. While this might seem simplistic, it’s the driving force behind countless strategic decisions, and minimizing production costs is a cornerstone of this pursuit. This article delves deep into the multifaceted reasons why firms are relentlessly driven to reduce their production expenses, exploring the economic principles, competitive pressures, and strategic advantages involved.
The Economics of Cost Minimization: A Foundation of Profitability
At its core, the motivation to minimize production costs stems directly from the basic economic principle of profit = total revenue - total cost. To maximize profit, a firm needs to either increase revenue or decrease costs, or ideally, both. While revenue generation is a crucial aspect of business, cost minimization often presents a more immediate and controllable avenue for improvement.
1. Increased Profit Margins: The Direct Impact
Reducing production costs directly translates into higher profit margins. A lower cost of goods sold (COGS) means that for each unit sold, the firm retains a larger portion as profit. This increased profitability can be reinvested into further growth, innovation, or distributed to shareholders as dividends, strengthening the firm's financial position. This is a powerful incentive, especially in competitive markets where profit margins can be razor-thin.
2. Competitive Advantage: Gaining an Edge in the Marketplace
In a competitive landscape, minimizing production costs often translates into a significant competitive advantage. Firms with lower production costs can offer their products or services at more competitive prices, attracting a larger customer base and potentially gaining market share. This price advantage can be particularly effective in price-sensitive markets. Alternatively, a firm might maintain its price but enjoy higher profit margins compared to its competitors.
3. Enhanced Efficiency and Productivity: Streamlining Operations
The pursuit of cost minimization often necessitates a thorough evaluation and optimization of the entire production process. This leads to improved efficiency and productivity. Firms may implement new technologies, streamline workflows, invest in employee training, and improve supply chain management to reduce waste and increase output. These improvements are not just about short-term cost savings; they lay the foundation for long-term operational excellence.
4. Achieving Economies of Scale: The Power of Volume
As firms increase their production volume, they often experience economies of scale. This means that the average cost of producing each unit decreases as the scale of production increases. This is due to factors such as bulk purchasing discounts on raw materials, improved utilization of equipment, and specialized labor. Economies of scale represent a powerful incentive for cost minimization, as it allows firms to reduce costs while simultaneously increasing output.
5. Enhanced Financial Stability: Weathering Economic Storms
Firms with lower production costs demonstrate greater resilience to economic downturns. They can withstand periods of reduced demand or price fluctuations more effectively, as their lower costs provide a buffer against profit erosion. This financial stability is crucial for long-term survival and growth, particularly in volatile markets.
Beyond Economics: Strategic Considerations in Cost Minimization
The drive to minimize production costs extends beyond pure economic calculations. Strategic factors also play a crucial role in shaping a firm's cost-reduction strategies.
1. Innovation and Technological Advancement: Embracing New Solutions
Firms constantly seek innovative ways to reduce production costs. This might involve adopting new technologies, automating processes, or employing lean manufacturing principles. These investments, while requiring upfront capital expenditure, can yield significant long-term cost savings and improve efficiency. Investment in R&D becomes a key component of long-term cost minimization strategies.
2. Supply Chain Optimization: Managing the Flow of Goods
Efficient supply chain management is vital for cost reduction. This involves streamlining the procurement of raw materials, optimizing logistics and distribution networks, and managing inventory levels effectively to minimize storage costs and reduce waste. Developing strong relationships with reliable suppliers is crucial for negotiating favorable prices and ensuring timely delivery.
3. Human Resource Management: Investing in Employees
While seemingly counterintuitive, investment in human capital is a crucial aspect of cost minimization. Training and development programs can enhance employee skills, leading to increased productivity and reduced errors. A motivated and engaged workforce is more likely to identify inefficiencies and contribute to cost-saving initiatives. This underscores the importance of effective employee retention strategies, lowering recruitment and training costs.
4. Quality Control: Reducing Waste and Rework
Implementing rigorous quality control measures throughout the production process can significantly reduce waste and rework. Identifying and addressing defects early on prevents costly repairs or replacements later in the process. This approach improves overall efficiency and reduces material and labor costs. Investment in quality control ensures higher product quality, reducing potential returns and reputational damage.
5. Environmental Sustainability: A Growing Factor
Increasingly, firms are recognizing the link between environmental sustainability and cost reduction. Implementing environmentally friendly practices, such as reducing energy consumption, utilizing renewable resources, and minimizing waste, can lead to significant cost savings in the long run. Moreover, these initiatives can enhance a firm's reputation and attract environmentally conscious consumers.
The Challenges of Cost Minimization: Striking a Balance
While the benefits of cost minimization are undeniable, firms face various challenges in pursuing this objective.
1. The Trade-off Between Cost and Quality: Maintaining Standards
A relentless focus on cost reduction can sometimes compromise product or service quality. Cutting corners to save money can lead to dissatisfied customers, damaged reputation, and ultimately, decreased profitability. Finding the right balance between cost reduction and quality maintenance is crucial.
2. Balancing Short-Term Gains with Long-Term Investments: Strategic Planning
Some cost-saving measures might yield short-term gains but compromise long-term growth. For example, delaying investments in new technology or employee training might save money in the short term, but it could hinder the firm's ability to compete in the long run. Strategic planning is essential for balancing immediate cost reductions with investments that enhance long-term competitiveness.
3. Ethical Considerations: Avoiding Unethical Practices
In the pursuit of cost minimization, firms must adhere to ethical business practices. Exploiting workers, compromising safety standards, or engaging in unsustainable environmental practices are unacceptable means of reducing costs. Maintaining ethical standards builds trust with consumers and stakeholders, leading to long-term success.
4. Unforeseen Circumstances: Adapting to Change
Unexpected events such as natural disasters, economic crises, or supply chain disruptions can significantly impact a firm's production costs. Having contingency plans and flexible strategies is crucial for navigating these challenges and minimizing their impact on profitability.
Conclusion: A Continuous Pursuit
Minimizing production costs is not a one-time event; it's an ongoing process requiring continuous monitoring, evaluation, and adaptation. Firms must leverage a combination of economic principles, strategic planning, technological innovation, and ethical practices to achieve sustainable cost reduction. By effectively managing costs, firms enhance profitability, gain a competitive edge, and ensure long-term sustainability in a dynamic and competitive business environment. The relentless pursuit of cost minimization is, therefore, not just a financial imperative but a strategic necessity for business success.
Latest Posts
Latest Posts
-
If A Technical Rescue Team Is Required
Apr 02, 2025
-
The Concept Of Structural Social Mobility Refers To
Apr 02, 2025
-
A Flexible Budget Performance Report Combines The
Apr 02, 2025
-
The Wonderful World Of Blood Worksheet Answers
Apr 02, 2025
-
Tu Asistir Clase Historia Frances
Apr 02, 2025
Related Post
Thank you for visiting our website which covers about Firms Are Motivated To Minimize Production Costs Because . We hope the information provided has been useful to you. Feel free to contact us if you have any questions or need further assistance. See you next time and don't miss to bookmark.