Gmaw And Fcaw Are Semiautomatic Welding Processes.
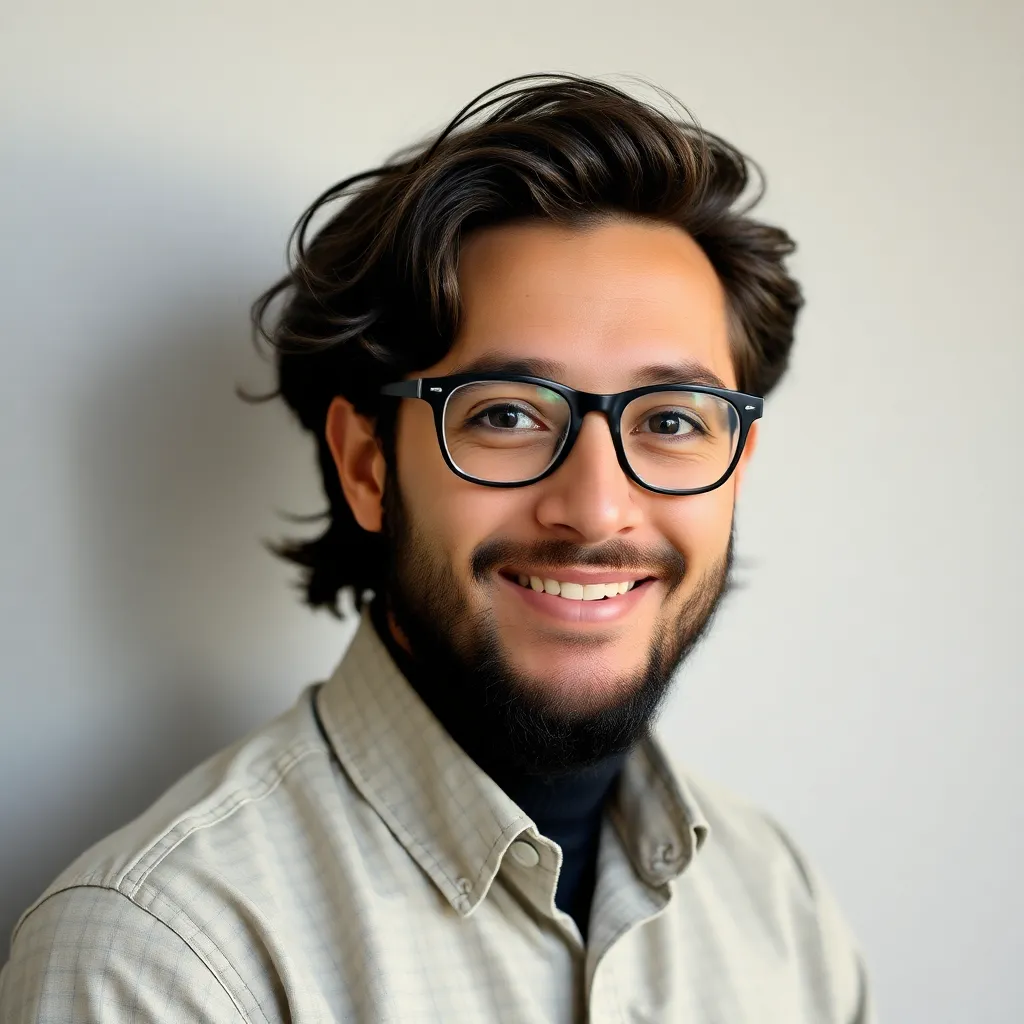
Breaking News Today
Mar 16, 2025 · 6 min read
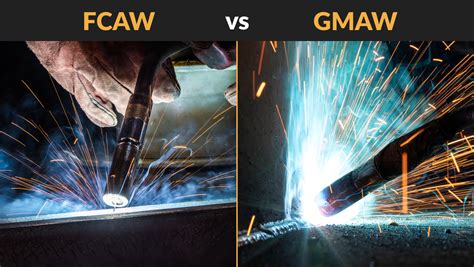
Table of Contents
GMAW and FCAW: A Deep Dive into Semiautomatic Welding Processes
Gas Metal Arc Welding (GMAW), also known as Metal Inert Gas (MIG) welding, and Flux-Cored Arc Welding (FCAW) are prominent semiautomatic welding processes widely used across various industries. Their versatility, efficiency, and relative ease of use make them indispensable in applications ranging from automotive manufacturing to pipeline construction. While both processes utilize a continuous consumable electrode, they differ significantly in their shielding methods and applications. This comprehensive article will delve into the intricacies of GMAW and FCAW, comparing and contrasting their features, benefits, and limitations.
Understanding the Semiautomatic Nature of GMAW and FCAW
Both GMAW and FCAW are classified as semiautomatic because they involve a power source that automatically feeds the welding wire, while the welder manually controls the welding gun and manipulates the weld puddle. This automation enhances speed and consistency compared to manual metal arc welding (SMAW), but it still requires skilled operators for optimal results. The semiautomatic nature of these processes makes them highly productive, particularly in high-volume applications.
Gas Metal Arc Welding (GMAW): The MIG Welding Process
GMAW relies on a continuously fed consumable electrode wire, typically solid wire, that acts as both the filler material and the electrode. The arc is generated between the wire and the workpiece, melting both to form the weld pool. A shielding gas, typically an inert gas like Argon or Helium or a mixture of Argon and CO2, protects the weld puddle from atmospheric contamination. This shielding gas prevents oxidation and porosity in the weld, resulting in a high-quality weld.
Advantages of GMAW:
- High Deposition Rates: GMAW offers significantly higher deposition rates compared to SMAW, leading to increased productivity.
- Versatile: GMAW can weld a wide range of metals including steel, aluminum, stainless steel, and copper alloys. Different shielding gases and wire compositions are used for different applications.
- Clean Welds: The shielding gas minimizes spatter and porosity, leading to cleaner and aesthetically pleasing welds.
- Easy to Learn (Relatively): While mastery requires skill, the basics of GMAW are easier to learn than SMAW, reducing training time.
- Portability: Portable GMAW machines are readily available, allowing for welding in various locations.
Disadvantages of GMAW:
- Shielding Gas Required: The need for shielding gas adds to the cost of operation.
- Sensitivity to Wind: The shielding gas can be easily disturbed by wind, potentially leading to weld defects.
- Limited Weldability of Some Materials: While versatile, GMAW may not be suitable for all materials or thicknesses.
- Equipment Cost: The initial investment for GMAW equipment can be higher than that for SMAW.
- Requires Cleanliness: The process is susceptible to contamination from dirt or moisture.
GMAW Variations:
GMAW is further categorized based on the transfer mode of the weld metal:
- Short-Circuiting Transfer: Suitable for thin materials, this mode produces small, short arcs that minimize spatter and penetrate less deeply.
- Globular Transfer: Characterized by large, unstable droplets, it's suitable for thicker materials but produces more spatter.
- Spray Transfer: This high-current mode produces a fine spray of molten metal, resulting in high deposition rates and deep penetration. It's suitable for thicker materials and requires more precise control.
- Pulsed Transfer: A combination of short-circuiting and spray transfer modes, this offers better control and reduced spatter.
Flux-Cored Arc Welding (FCAW): Shielding from Within
FCAW employs a tubular electrode filled with flux and a metallic core. The flux in the electrode core generates a shielding gas as it melts, eliminating the need for an external shielding gas supply in many instances. The flux also helps to protect the weld pool from atmospheric contamination and provides additional alloying elements.
Advantages of FCAW:
- No External Shielding Gas (in self-shielded FCAW): This eliminates the cost and inconvenience associated with external shielding gas.
- All-Position Welding: FCAW can be used in all welding positions, including overhead welding.
- Deep Penetration: FCAW typically produces welds with deeper penetration than GMAW, making it suitable for thicker materials.
- Less Sensitive to Wind: The self-generated shielding gas makes FCAW less sensitive to wind compared to GMAW.
- Higher Deposition Rates (in some cases): In certain applications, FCAW can achieve comparable or higher deposition rates than GMAW.
Disadvantages of FCAW:
- Less Clean Welds (than GMAW): The flux can create more spatter and slag, leading to less clean welds than GMAW.
- Slag Removal: The slag needs to be removed after welding, which adds to the post-weld processing time.
- Limited Material Compatibility (some fluxes): Certain flux formulations may not be compatible with all materials.
- Fume Generation: FCAW generates more fumes than GMAW, requiring proper ventilation.
- More Complex Wire (than GMAW): The wire is more complex and less versatile than the solid wire in GMAW.
FCAW Variations:
FCAW electrodes are classified based on their shielding gas requirements:
- Self-Shielded FCAW: These electrodes contain flux that generates its own shielding gas, eliminating the need for an external gas supply.
- Gas-Shielded FCAW: These electrodes require an external shielding gas for optimal performance. They often produce higher quality welds with less spatter than self-shielded FCAW.
GMAW vs. FCAW: A Comparative Analysis
Feature | GMAW | FCAW |
---|---|---|
Shielding | External shielding gas | Flux core generates shielding gas (or external) |
Electrode | Solid wire | Tubular wire with flux core |
Deposition Rate | High | High (often comparable or higher than GMAW) |
Weld Quality | Generally cleaner | Can be less clean due to slag |
Spatter | Relatively low (depending on transfer mode) | Can be higher (depending on the type of flux and process) |
Portability | Highly portable | Relatively portable |
Cost | Higher initial cost (due to gas) | Lower initial cost (no external gas needed in some cases) |
Application | Wide range of metals and thicknesses | Wide range of metals and thicknesses, often preferred for thicker materials |
Skill Level | Relatively easier to learn | Requires more skill to manage slag and achieve high-quality welds |
Versatility | High, depending on transfer modes | High, depending on flux core type |
Choosing Between GMAW and FCAW: Key Considerations
The choice between GMAW and FCAW depends on several factors, including:
- Material type and thickness: For thin materials, GMAW with short-circuiting transfer may be preferred. For thicker materials, FCAW or GMAW with spray transfer might be more suitable.
- Weld joint design: The geometry of the weld joint can influence the choice of process.
- Environmental conditions: FCAW’s self-shielded nature makes it more suitable for outdoor applications or areas with limited access to shielding gas.
- Cost considerations: GMAW may be more costly due to the shielding gas, but the higher quality welds it can produce might offset this.
- Required weld quality: If high-quality, clean welds are essential, GMAW might be preferred.
- Operator skill level: GMAW can be easier to learn, but FCAW may require more expertise for consistent high-quality results.
Conclusion: A Powerful Duo in the Welding World
GMAW and FCAW are both powerful and versatile semiautomatic welding processes that play crucial roles in various industries. Their efficiency and ability to produce high-quality welds make them indispensable for a wide range of applications. Understanding their individual strengths and weaknesses, and considering the factors outlined above, is key to selecting the appropriate process for a given welding task. Choosing the right process ultimately hinges on balancing cost-effectiveness, weld quality requirements, and the specific needs of the application. Continuous learning and practical experience are crucial for mastering both GMAW and FCAW and achieving consistently excellent results. The future of these processes lies in further advancements in technology, leading to even greater efficiency, precision, and versatility.
Latest Posts
Latest Posts
-
Letrs Unit 5 Session 4 Check For Understanding
Mar 16, 2025
-
According To Stalin What Must Soviets Do To Defeat Hitler
Mar 16, 2025
-
Cpr Test Questions And Answers American Heart Association
Mar 16, 2025
-
What Hostile Intelligence Collection Method Is The Process Of Obtaining
Mar 16, 2025
-
State Of Tennessee F Endorsement Practice Test
Mar 16, 2025
Related Post
Thank you for visiting our website which covers about Gmaw And Fcaw Are Semiautomatic Welding Processes. . We hope the information provided has been useful to you. Feel free to contact us if you have any questions or need further assistance. See you next time and don't miss to bookmark.