Load Chart Values Can Pinpoint Failures Of
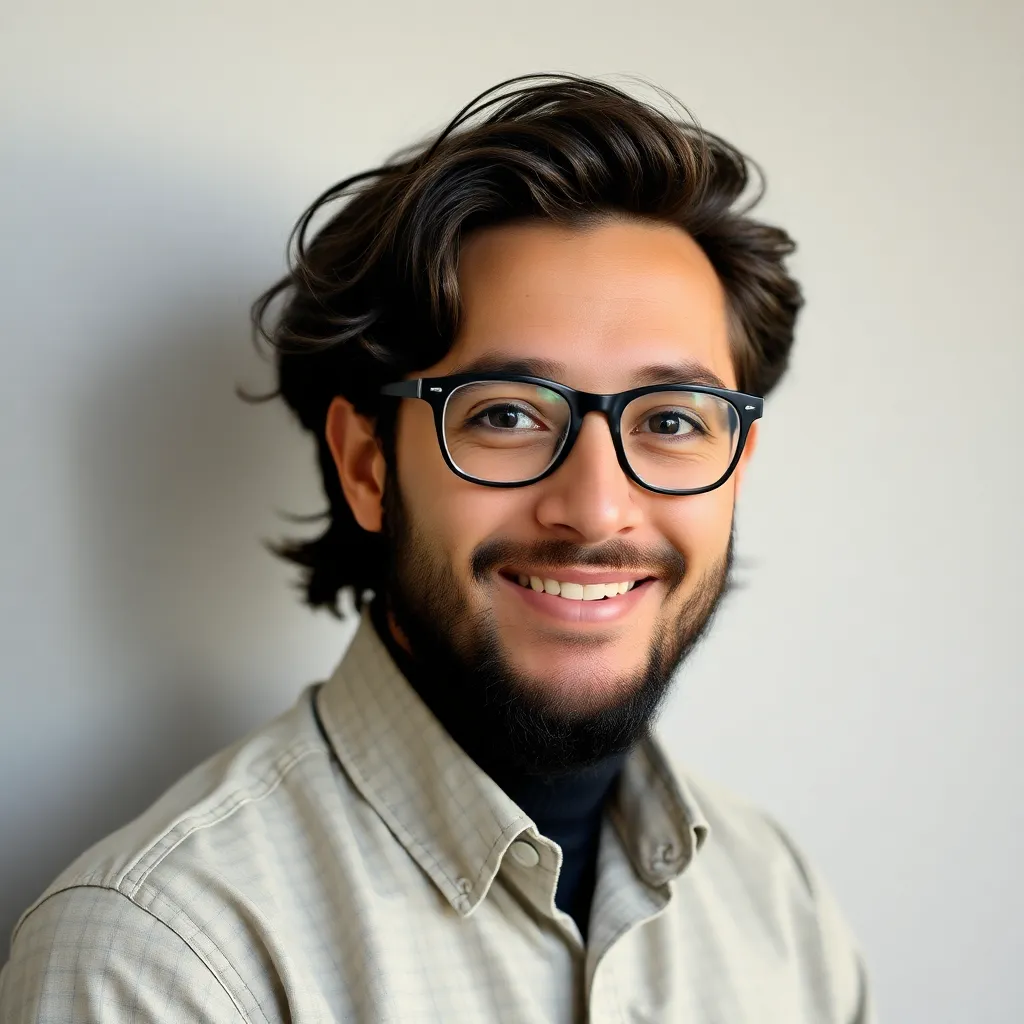
Breaking News Today
Apr 02, 2025 · 6 min read
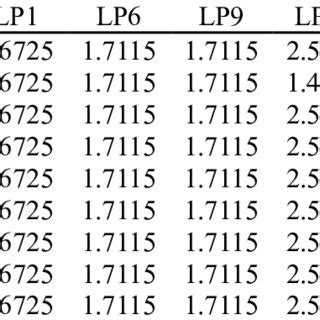
Table of Contents
Load Chart Values Can Pinpoint Failures of Rotating Equipment
Load charts, often overlooked gems in the world of industrial maintenance, offer a powerful diagnostic tool for predicting and preventing equipment failures. By meticulously tracking operational parameters like power consumption, current, vibration, and temperature, load charts provide invaluable insights into the health and performance of rotating equipment such as pumps, motors, compressors, and turbines. Analyzing these charts can reveal subtle anomalies that often precede catastrophic breakdowns, enabling proactive maintenance and minimizing downtime. This article delves into how load chart values can pinpoint various failures, highlighting the importance of data-driven predictive maintenance.
Understanding Load Charts and Their Significance
Load charts visually represent the performance of a machine over time. They plot key operational parameters against time, creating a comprehensive profile of the equipment's behaviour. This visual representation allows for easy identification of trends, anomalies, and deviations from normal operating patterns. Key parameters typically included in load charts include:
- Power Consumption (kW): A significant indicator of the energy required by the machine to perform its function. Unexpected spikes or drops can signal issues.
- Current (Amps): Measures the electrical current drawn by the motor. High current draw often indicates excessive load or impending motor failure.
- Vibration (m/s² or g): Monitors the level of vibration produced by the rotating equipment. Increased vibration levels often signify imbalances, misalignments, or bearing wear.
- Temperature (°C or °F): Tracks the operating temperature of various components. Excessive temperatures often indicate frictional losses, inadequate lubrication, or impending overheating.
- Pressure (psi or bar): Relevant for compressors, pumps, and other pressure-related equipment. Unusual pressure fluctuations can point to leakage or other problems.
- Flow Rate (GPM or LPM): Crucial for pumps and other fluid handling equipment. Changes in flow rate can suggest blockages, valve issues, or pump problems.
Why are load charts crucial for predictive maintenance?
Traditional maintenance strategies often rely on scheduled maintenance, leading to unnecessary downtime and resource consumption. Predictive maintenance, guided by data analysis, allows for timely interventions, preventing catastrophic failures and maximizing equipment lifespan. Load charts are integral to this strategy because they provide the raw data needed to anticipate problems before they occur.
Pinpointing Failures Through Load Chart Analysis
Analyzing load charts effectively requires understanding the normal operating parameters of the equipment. Establishing a baseline of normal operation is crucial for identifying deviations that could indicate problems. Here's how load chart values can pinpoint different types of failures:
1. Motor Failures
- Increased Current Draw: A consistently high current draw, exceeding the motor's rated capacity, indicates an overload. This could be due to excessive load, mechanical binding, or internal motor issues like worn bearings or winding problems. A sudden spike in current followed by a trip could indicate a short circuit.
- Increased Vibration: High vibration levels coupled with high current draw often signal bearing wear, rotor imbalance, or misalignment. The frequency of the vibration can also provide clues about the specific problem.
- Elevated Temperature: Excessive motor temperature, significantly above the normal operating range, points towards issues with ventilation, winding insulation degradation, or overloaded bearings.
2. Bearing Failures
- Increased Vibration: This is the most prominent indicator of bearing failure. An increase in vibration at specific frequencies is indicative of bearing damage, such as pitting, wear, or cage failure. The frequency content of the vibration can often pinpoint the faulty bearing.
- Elevated Temperature: Increased bearing temperature is a direct result of friction caused by wear or damage.
- Changes in Power Consumption: As bearings wear, the motor might draw more current to compensate for increased friction, resulting in increased power consumption.
3. Pump Failures
- Reduced Flow Rate: A significant decrease in flow rate, while maintaining constant power consumption, often suggests a blockage in the pipeline, a faulty valve, or impeller wear.
- Increased Power Consumption: If the pump struggles to achieve the desired flow rate, the power consumption will increase. This indicates increased friction due to wear, cavitation, or impeller problems.
- High Vibration: Similar to motor failures, increased vibration indicates imbalances, wear, or other mechanical issues within the pump.
- Pressure Fluctuations: Unusual pressure spikes or drops can be indicative of leakage or valve issues.
4. Compressor Failures
- Increased Power Consumption: Similar to pumps, increased power consumption suggests decreased efficiency and could point to internal leakage, valve problems, or excessive friction.
- Elevated Temperature: High discharge temperature points towards reduced efficiency and could signal problems with the cooling system, intercoolers, or internal components.
- Pressure Fluctuations: Unusual pressure variations, including sudden drops or surges, can indicate issues with valves, seals, or internal components.
- Increased Vibration: Elevated vibration often signals imbalance in the rotating components.
5. Gearbox Failures
- Increased Vibration: Gearbox failures are usually characterized by a distinct increase in vibration, often accompanied by specific frequency signatures indicative of gear tooth wear, misalignment, or bearing problems.
- Elevated Temperature: Increased temperature indicates excessive friction and potential gear wear or bearing failure.
- Noise: While not directly reflected in load charts, increased noise is often associated with gearbox failures and should be investigated alongside load chart analysis.
Interpreting Load Chart Data Effectively
Successfully using load charts for predictive maintenance requires a structured approach:
- Establish a Baseline: Collect data during normal operation to establish a baseline for each parameter. This baseline serves as a benchmark for future comparisons.
- Identify Deviations: Continuously monitor load chart values and identify any significant deviations from the established baseline.
- Analyze Trends: Don't just focus on individual data points; analyze trends and patterns over time. A gradual increase in a parameter might be more significant than a single spike.
- Utilize Frequency Analysis: Advanced analysis techniques, such as Fast Fourier Transform (FFT), can help identify specific frequencies in vibration data, providing valuable insights into the source of the problem.
- Correlate Data: Compare data from different parameters. For instance, a combination of increased current draw, elevated temperature, and increased vibration strongly suggests a motor or bearing problem.
- Implement an Alert System: Set thresholds for each parameter. When a parameter exceeds the predefined threshold, an alert system should be triggered to notify maintenance personnel.
Advanced Techniques and Considerations
- Data Acquisition Systems: Modern data acquisition systems automatically collect and store data from various sensors, making load chart analysis more efficient and effective.
- Machine Learning: Machine learning algorithms can analyze vast amounts of data from load charts to identify subtle patterns and predict potential failures with greater accuracy.
- Data Visualization Tools: Utilizing effective visualization tools can significantly improve the understanding and interpretation of load chart data.
- Expert Knowledge: While technology is valuable, the expertise of experienced technicians is still crucial for accurately interpreting load chart data and making informed decisions.
Conclusion
Load chart values are invaluable indicators of the health and performance of rotating equipment. By carefully monitoring and analyzing these values, organizations can transition from reactive to predictive maintenance, significantly reducing downtime, optimizing maintenance schedules, and extending the lifespan of their critical assets. Effective use of load charts, combined with advanced analytical techniques and expert knowledge, empowers organizations to proactively address potential problems, preventing costly failures and ensuring operational efficiency. This data-driven approach to maintenance is no longer a luxury, but a necessity for modern industrial operations. Embracing load chart analysis is a crucial step towards establishing a robust and reliable predictive maintenance program.
Latest Posts
Latest Posts
-
How Is Carbon Reintroduced Into The Atmosphere
Apr 03, 2025
-
Limestone And Marble Weather Faster Than Granite Because
Apr 03, 2025
-
Which Relationships Could Have A Negative Correlation Select Three Options
Apr 03, 2025
-
The Century Americas Time Happy Days Worksheet Answer Key
Apr 03, 2025
-
An Annuity Pays Benefits Based On Units
Apr 03, 2025
Related Post
Thank you for visiting our website which covers about Load Chart Values Can Pinpoint Failures Of . We hope the information provided has been useful to you. Feel free to contact us if you have any questions or need further assistance. See you next time and don't miss to bookmark.