Most Modern Plcs Can Connect To Building Networks Using
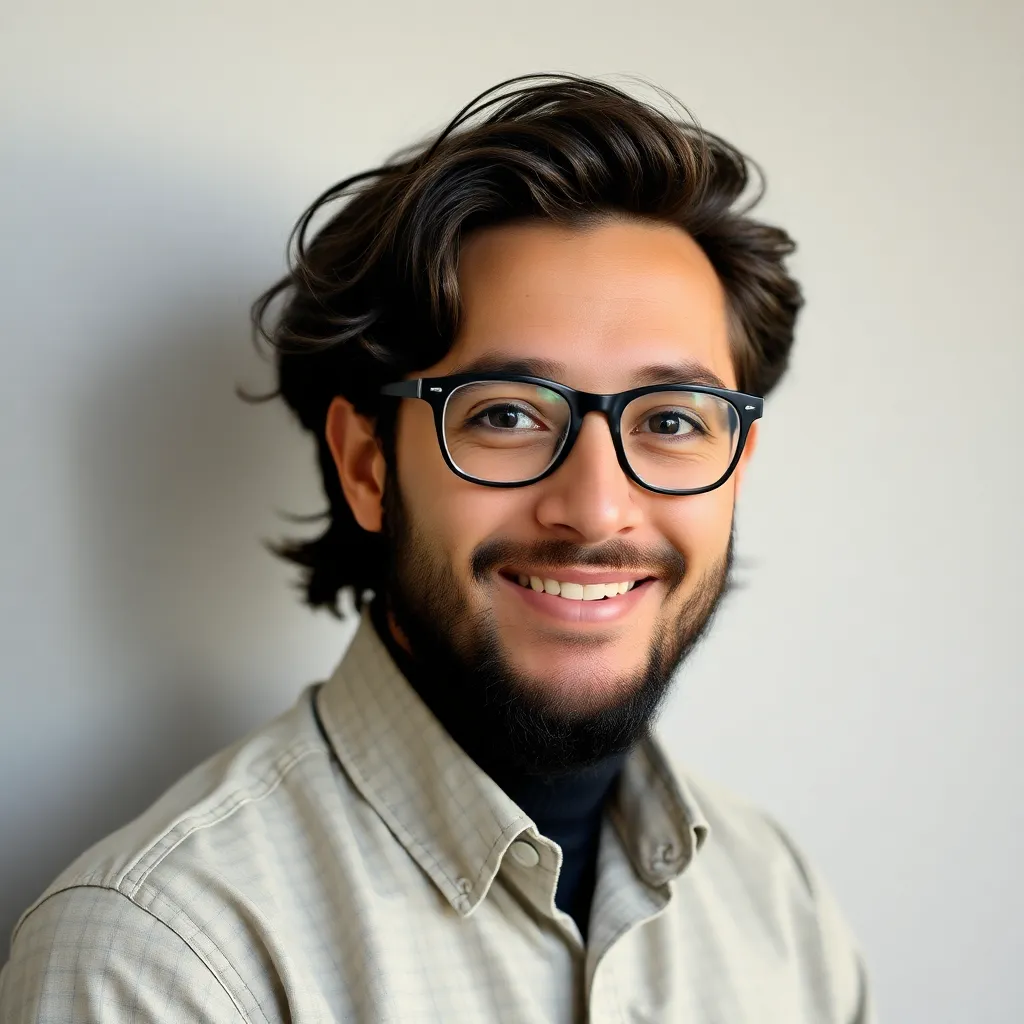
Breaking News Today
Apr 01, 2025 · 6 min read
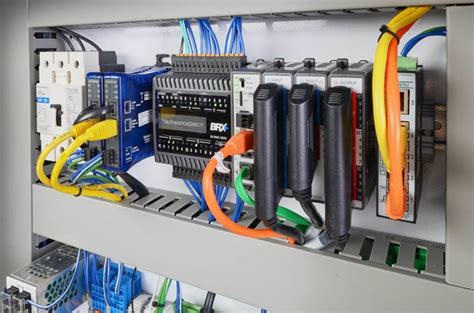
Table of Contents
Most Modern PLCs Can Connect to Building Networks Using: A Comprehensive Guide to PLC Network Connectivity
Modern Programmable Logic Controllers (PLCs) are no longer isolated islands of automation. Their ability to seamlessly integrate with building networks is revolutionizing industrial control systems, offering unprecedented levels of efficiency, monitoring, and control. This integration enables real-time data exchange, centralized management, and improved decision-making across various building systems. This article will explore the various ways modern PLCs connect to building networks, the advantages they offer, and the key considerations for successful implementation.
The Evolution of PLC Network Connectivity
The journey of PLCs from standalone devices to networked components has been remarkable. Initially, PLCs communicated primarily through proprietary protocols within limited ranges. This restricted data exchange and hindered integration with other building systems. The emergence of open communication protocols and standardized network technologies has dramatically changed this landscape. Today, PLCs leverage diverse network technologies to connect to building networks, enabling advanced functionalities and greater flexibility.
Common Network Protocols Used by Modern PLCs
Modern PLCs boast compatibility with a wide array of network protocols, enabling seamless integration with various building systems. Here are some of the most prevalent protocols:
-
Ethernet/IP: A popular industrial Ethernet protocol developed by Rockwell Automation, Ethernet/IP is renowned for its speed, reliability, and ability to handle large amounts of data. Its widespread adoption in industrial settings makes it a preferred choice for many PLC manufacturers. Its robust nature allows for reliable communication even in demanding industrial environments.
-
PROFINET: Developed by Siemens, PROFINET is another dominant industrial Ethernet protocol offering high speed and deterministic communication. This makes it highly suitable for real-time control applications. Its ability to support various network topologies adds to its flexibility.
-
Modbus TCP/IP: A widely used open standard, Modbus TCP/IP is known for its simplicity and interoperability. Its compatibility across various PLC brands and devices makes it an excellent choice for integrating legacy systems with newer technologies. Its open nature fosters greater flexibility and reduced vendor lock-in.
-
EtherCAT: A high-performance Ethernet protocol, EtherCAT (Ethernet for Control Automation Technology) is specifically designed for real-time applications. Its low latency and high bandwidth make it ideal for applications requiring precise and rapid control. Its deterministic nature is crucial for demanding applications.
-
Profibus: While slightly older, Profibus (Process Field Bus) remains relevant, particularly in legacy systems. It offers robust performance and is widely compatible with various industrial devices. Although newer protocols are gaining ground, Profibus’s established presence ensures its continued relevance in many settings.
Building Network Types and PLC Integration
PLCs can seamlessly integrate with diverse building networks, including:
-
Building Automation Systems (BAS): PLCs are increasingly incorporated into BAS to control and monitor various aspects of building infrastructure. This includes HVAC systems, lighting, security systems, and fire protection. The centralized monitoring and control capabilities of PLCs significantly enhance BAS efficiency and responsiveness.
-
Supervisory Control and Data Acquisition (SCADA) Systems: SCADA systems are powerful tools for managing large-scale industrial processes, and PLCs are essential components within these systems. They provide real-time data acquisition, process monitoring, and control, all essential aspects of SCADA functionality. The PLC’s role in SCADA extends to remote monitoring and control capabilities.
-
Internet of Things (IoT) Platforms: The integration of PLCs with IoT platforms allows for remote monitoring, data analytics, and predictive maintenance. This capability enhances operational efficiency and reduces downtime. Data collected from PLCs can be used to optimize building performance and resource allocation.
-
Cloud-Based Systems: Cloud connectivity enables remote access, data storage, and sophisticated analytics capabilities. This facilitates improved decision-making and proactive maintenance. The secure transfer of data to the cloud is essential for these applications.
Advantages of Connecting PLCs to Building Networks
The benefits of connecting PLCs to building networks are substantial and span several aspects of building management:
-
Centralized Monitoring and Control: A networked PLC system provides a centralized view of the entire building automation system. This allows operators to monitor and control multiple devices and systems from a single location, leading to improved efficiency and reduced operational costs.
-
Enhanced Data Acquisition and Analysis: PLCs can collect vast amounts of data from various building systems. This data can be analyzed to optimize building performance, identify potential problems, and improve energy efficiency. This data-driven approach allows for proactive problem-solving.
-
Improved Energy Efficiency: Real-time data from PLCs enables optimized control of HVAC systems, lighting, and other energy-consuming devices. This contributes to significant energy savings and reduces the building’s environmental impact.
-
Predictive Maintenance: Data analysis from PLCs can be used to predict potential equipment failures. This allows for proactive maintenance, minimizing downtime and extending the lifespan of building equipment.
-
Increased Security: Modern PLCs incorporate advanced security features to protect against unauthorized access and cyber threats. This ensures the integrity and security of building systems.
Key Considerations for PLC Network Integration
Successful integration of PLCs into building networks requires careful planning and consideration:
-
Network Infrastructure: The existing network infrastructure must be capable of supporting the additional traffic generated by the PLC system. This includes sufficient bandwidth and robust security measures. A thorough network assessment is crucial before implementation.
-
Network Security: Security is paramount, particularly when connecting to external networks. Firewalls, intrusion detection systems, and strong password policies are crucial to prevent unauthorized access and cyber threats. Regular security audits are also recommended.
-
Protocol Compatibility: Ensure that the PLCs and other building systems use compatible communication protocols. Incompatibility can lead to significant integration challenges.
-
Data Management: Develop a robust data management strategy to handle the large amounts of data generated by the PLC system. This includes data storage, retrieval, and analysis. Proper data management is essential for effective decision-making.
-
Scalability: The network infrastructure should be scalable to accommodate future expansion and upgrades. This avoids costly network overhauls as the building automation system evolves.
Future Trends in PLC Network Connectivity
The future of PLC network connectivity promises even greater integration and sophistication:
-
Increased use of cloud computing: Cloud-based platforms will play an increasingly important role in managing and analyzing data from PLC systems. This enables remote access, sophisticated analytics, and predictive maintenance capabilities.
-
Advancements in wireless technologies: Wireless technologies like 5G and Wi-Fi 6 will facilitate more flexible and cost-effective deployment of PLC networks. Wireless connectivity expands the possibilities for remote monitoring and control.
-
Artificial Intelligence (AI) and Machine Learning (ML): AI and ML algorithms will enhance data analysis capabilities, enabling improved decision-making and more efficient building automation. AI-driven predictive maintenance and optimization strategies will become increasingly prevalent.
-
Edge Computing: Processing data closer to the source (the edge) reduces latency and bandwidth requirements, optimizing the performance of building automation systems. Edge computing enhances the responsiveness of the system.
Conclusion
The ability of modern PLCs to connect to building networks represents a significant advancement in building automation. The benefits are numerous, ranging from improved energy efficiency and reduced operational costs to enhanced security and predictive maintenance. However, successful integration requires careful planning, consideration of network infrastructure, security protocols, and data management strategies. As technology continues to advance, we can expect even greater sophistication and integration in the future, driving efficiency and optimization across various building systems. The future of building automation is inextricably linked to the power and flexibility of networked PLCs.
Latest Posts
Latest Posts
-
What Is The Definition Of Distracted Driving
Apr 02, 2025
-
Which Factor Is A Component Of Mental Health
Apr 02, 2025
-
If A Technical Rescue Team Is Required
Apr 02, 2025
-
The Concept Of Structural Social Mobility Refers To
Apr 02, 2025
-
A Flexible Budget Performance Report Combines The
Apr 02, 2025
Related Post
Thank you for visiting our website which covers about Most Modern Plcs Can Connect To Building Networks Using . We hope the information provided has been useful to you. Feel free to contact us if you have any questions or need further assistance. See you next time and don't miss to bookmark.