Ordering Cost Is Which Type Of Cost
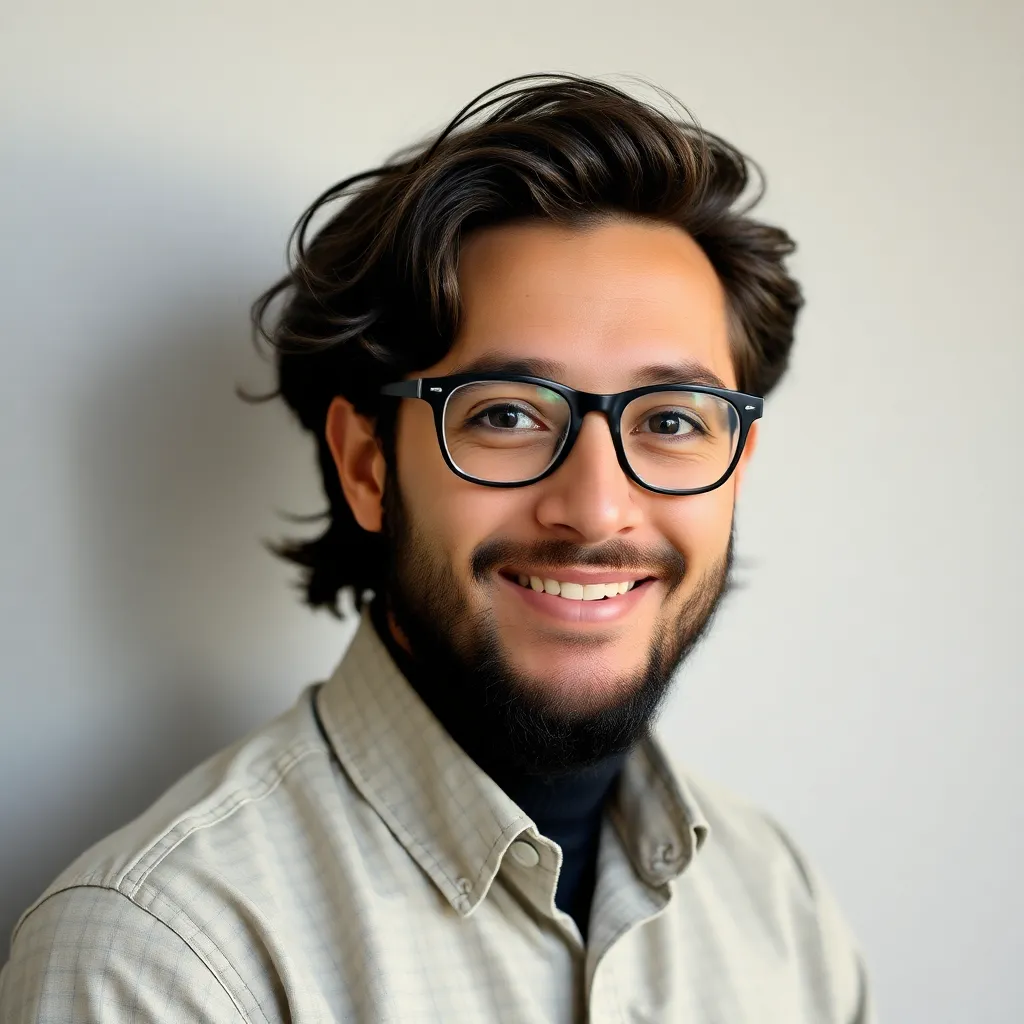
Breaking News Today
Apr 11, 2025 · 6 min read

Table of Contents
Ordering Cost: A Deep Dive into This Crucial Inventory Management Expense
Ordering cost, a critical component of inventory management, often gets overlooked amidst the focus on production, storage, and carrying costs. Understanding its nature and impact is crucial for optimizing supply chain efficiency and profitability. This comprehensive guide will delve into the intricacies of ordering cost, exploring its classification, calculation, and strategic implications for businesses of all sizes.
What is Ordering Cost?
Ordering cost, also known as procurement cost or setup cost, encompasses all expenses associated with placing and receiving an order for inventory. It's not simply the price of the goods themselves; rather, it's the cost of acquiring those goods. This includes a wide range of expenses, from initial requisition to final receipt and inspection. Failing to accurately account for ordering costs can lead to inefficient inventory management and ultimately, reduced profitability.
Key Components of Ordering Cost:
- Order preparation: This includes time spent creating purchase orders, contacting suppliers, negotiating prices, and finalizing order specifications. The cost here reflects employee salaries and associated administrative overhead.
- Order transmission: Costs associated with transmitting the order, whether it’s through mail, fax, email, or electronic data interchange (EDI). While seemingly minor, these costs can accumulate significantly with high order frequency.
- Receiving and inspection: Upon delivery, costs are incurred in inspecting the goods for quality and quantity, checking against the purchase order, and processing the paperwork associated with receiving the shipment. This includes labor costs and potential disposal fees for damaged or defective items.
- Supplier interaction: This involves communication with suppliers regarding order status, resolving discrepancies, and managing supplier relationships. The cost encompasses the time spent by employees and any associated travel expenses.
- Expediting: In situations where orders are delayed, expediting costs can arise, involving additional communication, transportation fees for faster delivery, and potential penalties for late delivery.
- Quality control: Inspecting materials upon arrival, identifying defective items, and possibly returning them to the supplier.
Classifying Ordering Cost: Fixed vs. Variable
Understanding the behavior of ordering costs is paramount for effective inventory management. Ordering costs are primarily considered variable costs. This means they directly correlate with the number of orders placed. The more orders you place, the higher your ordering costs will be.
However, there's a subtle nuance. While the bulk of ordering cost is variable, a small portion can be considered semi-variable or even slightly fixed. This stems from the administrative overhead related to the ordering process. Regardless of the number of orders, certain administrative tasks will always need to be performed. For instance, maintaining supplier relationships requires a certain level of ongoing communication and interaction, regardless of order frequency.
The variable nature of ordering costs is significantly impacted by the order size. Larger orders, while potentially reducing the number of orders placed, might increase other aspects of the ordering cost (e.g., transportation). This interplay between order size and ordering cost is a key consideration in determining the economic order quantity (EOQ) – a crucial concept in inventory management that minimizes the total cost of inventory.
Ordering Cost vs. Other Inventory Costs
It's essential to distinguish ordering cost from other inventory-related expenses:
- Holding cost (Carrying cost): This encompasses all expenses associated with storing inventory, including warehouse rent, insurance, taxes, obsolescence, and the cost of capital tied up in inventory. This is often a significant portion of total inventory costs. Unlike ordering cost, which increases with order frequency, holding cost increases with inventory levels.
- Production cost: This is the cost of manufacturing the goods, including raw materials, labor, and overhead. It's distinct from ordering cost, which arises after the decision to purchase has been made.
- Shortage cost: This represents the expenses incurred when inventory runs out, such as lost sales, expedited shipping, and potential damage to customer relationships. Effective inventory management aims to balance ordering costs and holding costs to minimize shortage costs.
Calculating Ordering Cost: A Practical Approach
Accurately calculating ordering cost requires meticulous record-keeping and a clear understanding of all contributing factors. There's no single formula; the method will vary depending on the specific business and its ordering processes. However, a common approach involves breaking down the cost into its individual components and then summing them up.
For example:
Let's say a company places 100 orders per year. The breakdown might look like this:
- Order preparation: $10 per order ($1000 total) – This includes staff time for order creation and review.
- Order transmission: $2 per order ($200 total) – This includes the cost of online order placement, postage for a physical order (if required), phone calls to the supplier, etc.
- Receiving and inspection: $5 per order ($500 total) – This is the employee time in receiving the goods and inspecting for defects.
- Supplier interaction: $3 per order ($300 total) – This accounts for the employee time spent communicating with the supplier.
Total Ordering Cost: $1000 + $200 + $500 + $300 = $2000 per year
This calculation is a simplified example. In reality, many more factors could be included, such as expediting costs, transportation fees, and potential costs associated with defective goods.
The Impact of Ordering Cost on Inventory Management Strategies
Efficient inventory management hinges on balancing ordering costs and holding costs. High ordering costs incentivize fewer, larger orders, leading to higher holding costs. Conversely, low ordering costs may encourage more frequent, smaller orders, reducing holding costs but increasing ordering costs. The optimal balance is achieved through strategies like:
- Economic Order Quantity (EOQ): A mathematical model that determines the optimal order size that minimizes the total inventory costs (ordering cost + holding cost).
- Just-in-Time (JIT) Inventory: A system that aims to minimize inventory levels by receiving goods only when needed. This reduces holding costs but increases the risk of shortages and may increase ordering frequency and therefore ordering costs.
- Vendor-Managed Inventory (VMI): A system where the supplier manages the inventory levels for the buyer. This can reduce ordering costs and improve efficiency.
- Efficient Procurement Processes: Streamlining the ordering process through automation, improved communication, and efficient supplier relationships can significantly reduce ordering costs.
- Strategic Supplier Selection: Choosing reliable suppliers with efficient delivery systems can minimize delays and associated expediting costs.
Technological Advancements and Ordering Cost Reduction
Technology plays a crucial role in mitigating ordering costs. Software solutions such as Enterprise Resource Planning (ERP) systems automate many aspects of the ordering process, including purchase order generation, order tracking, and inventory management. Automated systems can significantly reduce the labor costs associated with order placement and management, minimizing ordering costs and enhancing efficiency. Furthermore, the use of electronic data interchange (EDI) streamlines communication with suppliers, reducing errors and expediting the ordering process.
Conclusion: Mastering Ordering Cost for Profit Optimization
Understanding and managing ordering costs is vital for any business seeking to optimize its supply chain and maximize profitability. By accurately calculating these costs, implementing effective inventory management strategies, and leveraging technological advancements, businesses can significantly reduce unnecessary expenditures and enhance their overall financial performance. Remember, a comprehensive understanding of all cost components and their interplay allows for data-driven decisions that lead to improved inventory control and a stronger bottom line. Continuous monitoring and adjustments to your ordering processes are crucial for long-term success in managing this often overlooked yet critical aspect of inventory management.
Latest Posts
Latest Posts
-
A Researcher Asks An Irb To Waive The Requirement
Apr 18, 2025
-
What Is Not A Component Of Biodiversity
Apr 18, 2025
-
Hide The Column Showing 2019 Data And The Bonus Rate
Apr 18, 2025
-
Activated Cd8 Cells Form A Clone Of Blank Cells
Apr 18, 2025
-
Create An Automatic Basic Report From The Classes Table
Apr 18, 2025
Related Post
Thank you for visiting our website which covers about Ordering Cost Is Which Type Of Cost . We hope the information provided has been useful to you. Feel free to contact us if you have any questions or need further assistance. See you next time and don't miss to bookmark.