Points Of Distribution Are Strategically Placed Facilities Where
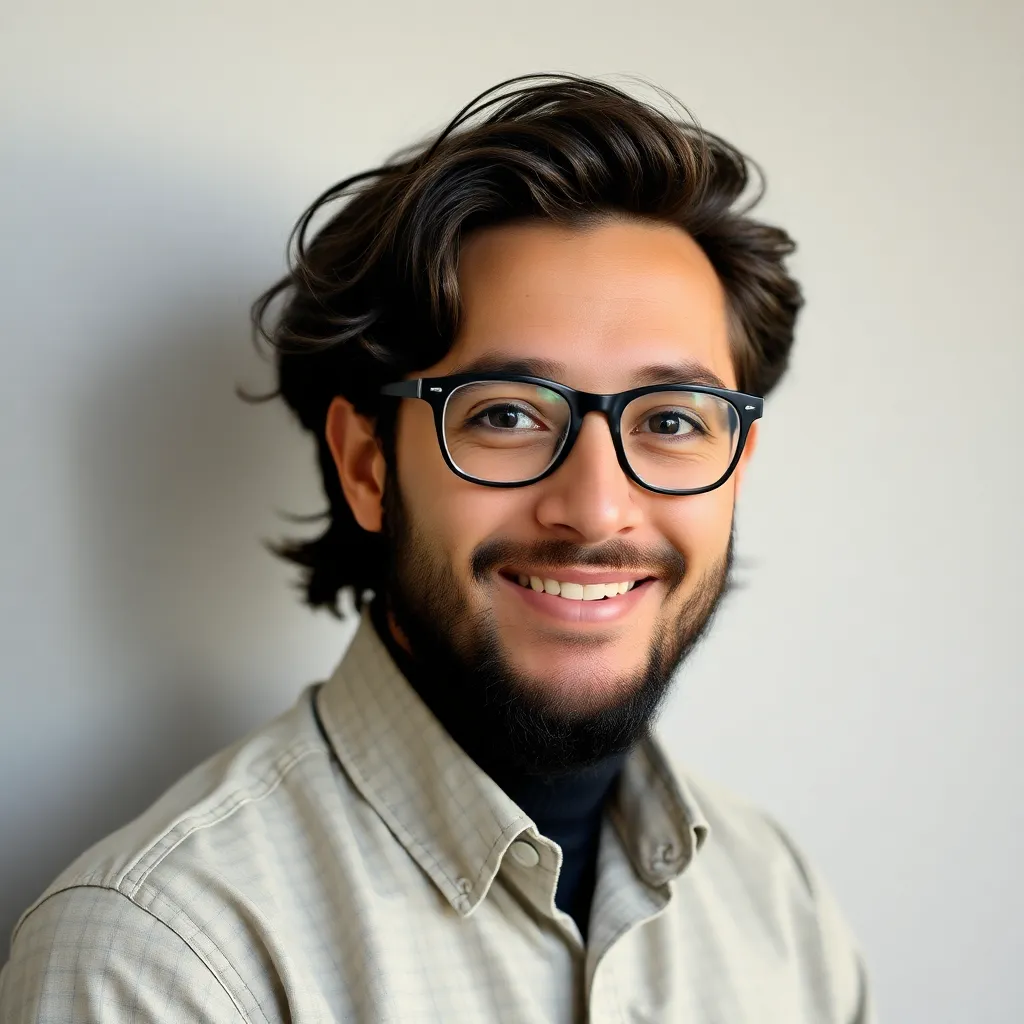
Breaking News Today
Apr 04, 2025 · 8 min read

Table of Contents
Points of Distribution: Strategically Placed Facilities Where Goods and Services Meet Consumers
Points of distribution (PODs) are strategically placed facilities that play a crucial role in the efficient and effective flow of goods and services from producers to consumers. These facilities are more than just warehouses; they are vital nodes within a supply chain, impacting everything from delivery times and costs to customer satisfaction and overall business profitability. Understanding the strategic placement and functionality of PODs is critical for businesses seeking to optimize their operations and gain a competitive edge.
What Are Points of Distribution (PODs)?
PODs are the locations where products are stored, sorted, and prepared for final delivery to the end consumer or the next stage in the supply chain. This encompasses a wide range of facilities, including:
- Warehouses: Large-scale storage facilities used for bulk storage and distribution.
- Distribution Centers (DCs): More sophisticated facilities that handle inventory management, order fulfillment, and value-added services like packaging and labeling.
- Retail Stores: The most direct point of distribution for many businesses, where consumers can purchase products directly.
- Pop-up Shops: Temporary retail locations used for promotions or reaching specific customer segments.
- Micro-fulfillment Centers (MFCs): Smaller, localized facilities designed to serve a specific geographic area, optimizing last-mile delivery.
- Cross-docks: Facilities designed for efficient transfer of goods between transportation modes, minimizing storage time.
The type of POD used depends heavily on the nature of the business, the type of products being distributed, and the target market. A large e-commerce retailer might utilize a network of DCs and MFCs, whereas a small local business might rely solely on its retail store.
Strategic Placement: The Key to Efficiency
The strategic placement of PODs is paramount for success. An inefficiently located POD can lead to increased transportation costs, longer delivery times, and ultimately, dissatisfied customers. Several factors must be considered when choosing POD locations:
1. Proximity to Customers: Minimizing Last-Mile Costs
A core principle of POD placement is minimizing the distance between the POD and the end consumer. This is particularly crucial for businesses focusing on speed of delivery, such as those in the e-commerce sector. Locating PODs closer to high-density population centers reduces transportation costs and delivery times, improving customer satisfaction. This often involves using advanced analytics and geographic information systems (GIS) to identify optimal locations based on population density, purchasing patterns, and traffic flow.
2. Transportation Infrastructure: Ensuring Seamless Connectivity
Efficient transportation infrastructure is essential for smooth operation of PODs. Easy access to major highways, railways, and airports is vital for the timely movement of goods. Considering proximity to major transportation hubs allows for efficient inbound and outbound logistics, reducing delays and transportation costs. This includes analyzing the availability of different transportation modes (truck, rail, air) and their associated costs and transit times.
3. Labor Availability and Costs: Finding the Right Workforce
The availability of a skilled and reliable workforce is another critical factor. PODs require personnel for tasks such as receiving, storing, picking, packing, and shipping goods. Locating PODs in areas with a readily available workforce at a competitive wage reduces labor costs and ensures efficient operations. This necessitates research into local labor markets, including wage rates, unemployment rates, and the availability of skilled workers in logistics and warehousing.
4. Land Costs and Availability: Balancing Cost and Location
The cost of land varies significantly depending on location. While proximity to customers is desirable, it often comes with higher land costs. Businesses must balance the benefits of prime locations with the cost of land acquisition and construction. A thorough cost-benefit analysis is crucial, considering the long-term implications of land acquisition and operational expenses. This might involve exploring less expensive areas slightly further from high-density populations, finding a balance between proximity and cost-effectiveness.
5. Regulatory and Tax Considerations: Navigating Local Laws
Local regulations and tax policies can significantly impact POD operations. Factors such as zoning laws, building codes, and property taxes need to be considered when selecting a location. Understanding the regulatory environment ensures compliance and minimizes potential legal issues. Consultations with legal and tax professionals are essential to understand the implications of different locations and comply with all applicable laws.
6. Scalability and Future Growth: Planning for Expansion
When choosing a POD location, businesses should also consider future scalability and growth potential. The chosen location should have sufficient space and infrastructure to accommodate future expansion. This includes assessing the available land area, potential for expansion, and accessibility for future infrastructure improvements. Long-term planning is crucial to avoid future limitations and ensure the POD can adapt to changes in demand.
7. Security Considerations: Protecting Valuable Inventory
Security is a major concern for PODs, particularly those storing high-value goods. The chosen location should have adequate security measures, including fencing, lighting, surveillance systems, and security personnel. This ensures the protection of inventory from theft and damage, minimizing losses and maintaining operational efficiency. A robust security plan should be integral to the POD's design and operation, balancing cost and effectiveness.
Optimizing POD Operations for Maximum Efficiency
Strategic placement is only one aspect of optimizing POD operations. Efficient internal processes are also crucial:
1. Inventory Management: Utilizing Technology for Efficiency
Efficient inventory management is essential for preventing stockouts and minimizing waste. Utilizing technologies like Warehouse Management Systems (WMS) and Radio Frequency Identification (RFID) allows for real-time tracking of inventory levels, improving accuracy and streamlining picking and packing processes. This allows for precise forecasting of demand, optimizing stock levels and reducing storage costs.
2. Order Fulfillment: Streamlining the Picking and Packing Process
Streamlining the order fulfillment process is key to reducing delivery times and improving customer satisfaction. Utilizing optimized picking strategies, such as wave picking or zone picking, along with efficient packaging techniques, can significantly increase throughput. Investing in automation, such as automated guided vehicles (AGVs) or robotic picking systems, can further enhance efficiency and reduce labor costs.
3. Transportation Management: Optimizing Routes and Carrier Selection
Efficient transportation management involves optimizing delivery routes, selecting appropriate carriers, and tracking shipments in real-time. Utilizing Transportation Management Systems (TMS) allows for efficient route planning, carrier selection based on cost and delivery time, and real-time tracking of shipments, ensuring timely delivery and minimizing transportation costs. This also involves considering sustainable transportation options to reduce environmental impact.
4. Technology Integration: Connecting Systems for Seamless Operations
Integrating various technologies across the supply chain is crucial for seamless POD operations. This involves connecting WMS, TMS, and other systems to provide real-time visibility into inventory levels, order status, and shipment tracking. This integrated approach enhances efficiency, reduces errors, and improves decision-making. Investing in robust data analytics capabilities allows for data-driven insights to further optimize operations.
5. Workforce Management: Empowering Employees Through Training
A well-trained and motivated workforce is essential for efficient POD operations. Investing in employee training and development programs ensures staff are equipped with the necessary skills and knowledge to perform their tasks efficiently and safely. A positive work environment and opportunities for advancement boost employee morale and productivity. This also necessitates adhering to safety standards and regulations to minimize workplace accidents.
The Future of Points of Distribution
The landscape of points of distribution is constantly evolving, driven by technological advancements and changing consumer expectations. Several key trends are shaping the future of PODs:
-
Growth of E-commerce and Last-Mile Delivery: The rapid growth of e-commerce is driving the need for more localized PODs, such as MFCs, to optimize last-mile delivery. This trend will continue to accelerate, requiring businesses to adapt their distribution networks to meet the demands of faster and more convenient delivery.
-
Automation and Robotics: Automation and robotics are becoming increasingly prevalent in PODs, automating tasks such as picking, packing, and sorting. This improves efficiency, reduces labor costs, and increases accuracy. Further advancements in robotics and AI will continue to transform POD operations.
-
Data Analytics and AI-driven Optimization: Data analytics and artificial intelligence are playing a crucial role in optimizing POD operations. Analyzing data on inventory levels, order patterns, and delivery times allows businesses to make data-driven decisions to improve efficiency and reduce costs. AI-powered systems can optimize route planning, predict demand, and automate decision-making.
-
Sustainability and Green Logistics: There is a growing emphasis on sustainability in logistics, with businesses seeking to reduce their environmental impact. This involves using more fuel-efficient vehicles, optimizing delivery routes to reduce mileage, and adopting eco-friendly packaging materials. Sustainable practices are becoming increasingly important considerations in POD operations.
-
Omnichannel Distribution: Businesses are increasingly adopting omnichannel strategies, integrating online and offline channels to provide a seamless customer experience. This requires a flexible and adaptable distribution network, capable of handling orders from various channels. PODs must be able to support various fulfillment models, including in-store pickup, home delivery, and click-and-collect.
In conclusion, points of distribution are essential components of a successful supply chain. Strategic placement, optimized operations, and a forward-looking approach are key to maximizing efficiency, reducing costs, and delivering an exceptional customer experience. By embracing technological advancements and adapting to evolving market demands, businesses can leverage their PODs to gain a competitive advantage in the ever-changing landscape of commerce.
Latest Posts
Latest Posts
-
Need For Refers To Maintaining Positive Relationships With Others
Apr 05, 2025
-
La Maison Es Un Mercado Al Aire Libre
Apr 05, 2025
-
Which Action Is One Role Of Rna Polymerase During Transcription
Apr 05, 2025
-
What Is Most Significant About This Quote By Raphael Lemkin
Apr 05, 2025
-
The Ich E6 Guideline Should Be Followed When
Apr 05, 2025
Related Post
Thank you for visiting our website which covers about Points Of Distribution Are Strategically Placed Facilities Where . We hope the information provided has been useful to you. Feel free to contact us if you have any questions or need further assistance. See you next time and don't miss to bookmark.