Sae Flare Fittings Used On Hydraulic Brake Systems Must ________.
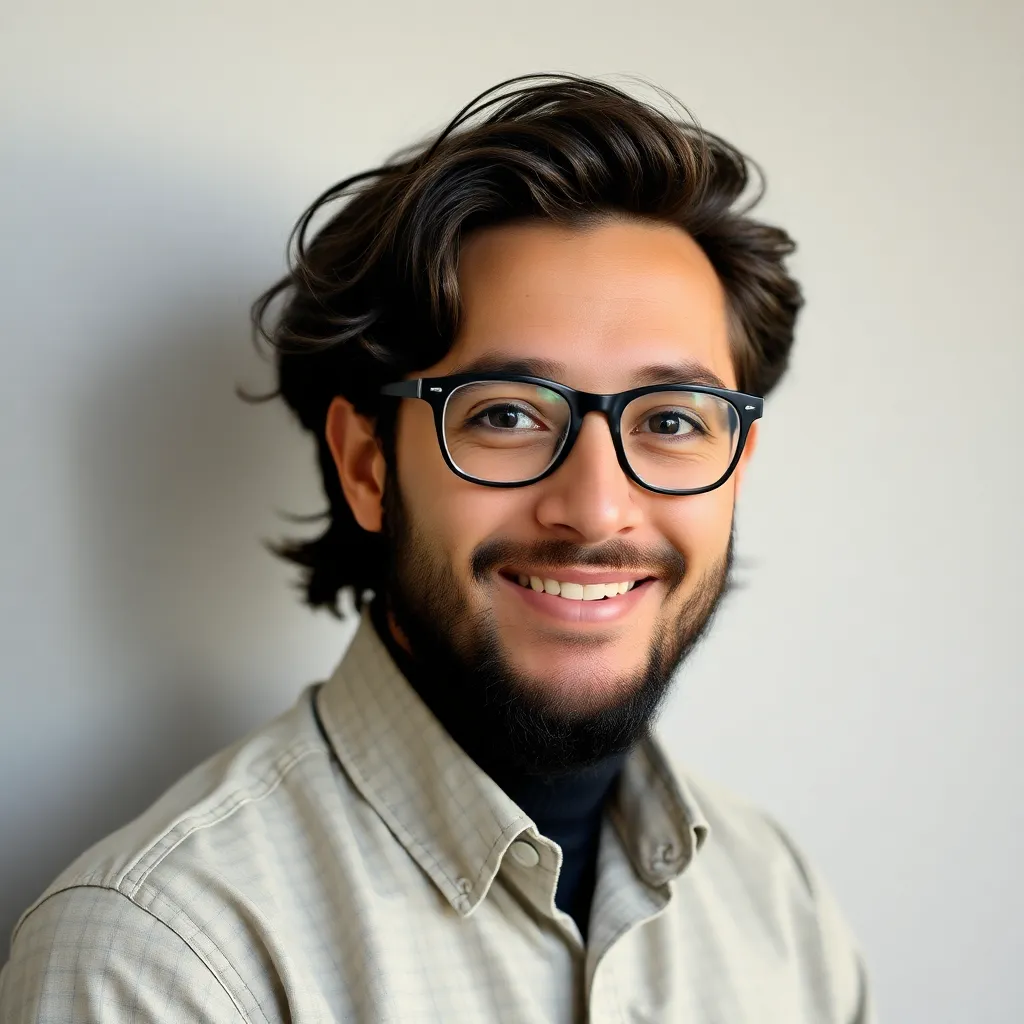
Breaking News Today
Apr 10, 2025 · 6 min read

Table of Contents
SAE Flare Fittings Used on Hydraulic Brake Systems Must Seal Properly
Hydraulic brake systems are critical for vehicle safety. Their effectiveness hinges on the integrity of every component, and a crucial element is the proper sealing of SAE flare fittings. These fittings, ubiquitous in automotive and industrial hydraulic applications, must create a leak-free connection to prevent brake failure and ensure reliable performance. This article delves into the importance of proper sealing in SAE flare fittings used in hydraulic brake systems, exploring the various factors that contribute to successful sealing, potential failure points, and best practices for installation and maintenance.
The Critical Role of SAE Flare Fittings in Hydraulic Brake Systems
SAE (Society of Automotive Engineers) flare fittings are a common type of compression fitting used to connect hydraulic lines and components. They utilize a flared end on the tubing, which is compressed against a mating seat in the fitting body, creating a seal. This design is simple, reliable, and relatively inexpensive, making it a popular choice for braking systems and other hydraulic applications. However, the effectiveness of the seal is paramount. A leak in the brake system, even a small one, can compromise stopping power, leading to dangerous consequences.
Understanding the Sealing Mechanism
The sealing mechanism of an SAE flare fitting relies on the precise deformation of the flared tubing against the fitting's cone seat. This creates a metal-to-metal seal, preventing the escape of hydraulic fluid. The process involves several key factors:
-
Flare Angle: The precise angle of the flare on the tubing is critical. A deviation from the specified angle (typically 37° or 45°) can lead to incomplete contact with the seating surface, resulting in a leak.
-
Flare Quality: A properly formed flare is crucial. An uneven, damaged, or improperly sized flare will not create a sufficient seal. Imperfections such as cracks or burrs can compromise the seal's integrity.
-
Seating Surface: The fitting's seating surface must be clean, smooth, and undamaged. Any debris, corrosion, or damage to this surface will prevent proper contact with the flared tubing.
-
Tightening Torque: The fitting must be tightened to the manufacturer's specified torque. Over-tightening can damage the flare, while under-tightening won't create a sufficient seal. Using a torque wrench is essential for consistent and accurate tightening.
Potential Causes of Leaks in SAE Flare Fittings
Leaks in SAE flare fittings are a serious concern. Identifying the root cause is crucial for effective repair and prevention. Common culprits include:
1. Improper Flare Preparation:
-
Incorrect Flare Angle: As mentioned above, an improperly formed flare angle directly impacts the seal.
-
Damaged Flare: A damaged flare, whether from improper flaring tools, bending, or mishandling, prevents proper sealing.
-
Tube Burrs: Burrs inside the tubing can damage the fitting's seating surface, preventing a proper seal.
2. Fitting Issues:
-
Damaged or Corroded Seating Surface: Dirt, corrosion, or damage to the seating surface within the fitting prevents proper contact and sealing.
-
Improper Fitting Selection: Using an incompatible fitting, one that doesn't match the tubing size or flare angle, will prevent a reliable seal.
-
Damaged Fitting Threads: Damaged or cross-threaded fittings create leaks and structural weakness.
3. Installation Errors:
-
Over-tightening: This can crush or damage the flare, leading to leaks.
-
Under-tightening: Insufficient tightening results in an incomplete seal.
-
Cross-threading: Misaligned threads prevent proper engagement and sealing.
-
Contamination: Dirt or debris on the tubing or fitting's threads will prevent proper sealing.
4. Material Degradation:
-
Corrosion: Over time, corrosion can weaken the flare, the fitting, or the tubing, leading to leaks. This is particularly true in environments exposed to moisture or harsh chemicals.
-
Material Fatigue: Repeated flexing or vibration can weaken the tubing and fitting, ultimately leading to failure.
Best Practices for Installation and Maintenance of SAE Flare Fittings
Preventing leaks in SAE flare fittings requires careful attention to detail throughout the entire process, from preparation to installation.
1. Proper Tube Preparation:
-
Cleanliness: Thoroughly clean the tubing before flaring to remove any dirt, grease, or debris. This ensures a clean, accurate flare.
-
Cutting: Use a sharp tubing cutter to ensure a clean, square cut. A jagged or uneven cut can lead to a poorly formed flare.
-
Deburring: Remove any burrs from the inside and outside of the cut tubing to prevent damage to the flare and the fitting.
-
Flaring: Use the correct flaring tool for the tubing size and desired flare angle. Ensure the flare is properly formed and free from imperfections.
2. Fitting Preparation:
-
Cleanliness: Clean the fitting threads and seating surface to remove any dirt, grease, or debris.
-
Inspection: Carefully inspect the fitting for any damage or defects before installation.
-
Lubrication: Apply a small amount of thread sealant (compatible with the hydraulic fluid) to the fitting threads to ensure proper sealing and prevent galling.
3. Installation Procedure:
-
Proper Alignment: Ensure the fitting is properly aligned with the tubing before tightening.
-
Torque Specifications: Use a torque wrench to tighten the fitting to the manufacturer's specified torque. Never exceed the recommended torque.
-
Leak Testing: After installation, thoroughly test the fitting for leaks using appropriate methods. Pressure testing is often necessary to ensure a leak-free connection.
4. Regular Maintenance:
-
Inspection: Regularly inspect fittings for leaks, corrosion, or damage.
-
Replacement: Replace any damaged or suspect fittings promptly.
-
Fluid Condition: Monitor the condition of the hydraulic fluid. Contaminated fluid can contribute to corrosion and seal failure.
Consequences of Improper Sealing and Necessary Preventative Measures
The consequences of improperly sealed SAE flare fittings in a hydraulic brake system are severe and can have catastrophic results. Even a minor leak can lead to:
-
Reduced Braking Performance: A leak reduces the hydraulic pressure available to actuate the brakes, resulting in a longer stopping distance and reduced braking effectiveness.
-
Brake Failure: A significant leak can lead to complete brake failure, resulting in a loss of control and a potential accident.
-
Corrosion: Hydraulic fluid leakage can accelerate corrosion on surrounding components.
-
Fluid Loss: Leakage leads to a loss of brake fluid, which needs to be regularly topped up, a clear indicator of a problem.
Preventative measures are essential for maintaining the integrity of your braking system. These include:
-
Regular Inspections: Regularly inspect your brake system for leaks and signs of damage.
-
Professional Service: If you are unsure about any aspect of your brake system, seek professional help from a qualified mechanic.
-
Proper Maintenance: Follow the manufacturer's recommendations for brake fluid changes and maintenance.
-
Quality Components: Use high-quality SAE flare fittings and tubing to ensure optimal performance and longevity.
Advanced Considerations: Different Types of SAE Flare Fittings
While the general principles of sealing apply across the board, understanding the nuances of different SAE flare fitting types can further enhance your understanding and maintenance practices. These include:
-
Single Flare: The most common type, featuring a single flare on the tubing.
-
Double Flare: Offers increased sealing surface area and strength compared to single flares, providing enhanced robustness.
-
Inverted Flare: The flare is formed on the inside of the tubing, offering improved resistance to damage.
Each type has its own specific installation requirements and torque specifications, which should be strictly adhered to. Choosing the right fitting type for the application is critical for optimal performance and safety.
In conclusion, SAE flare fittings used on hydraulic brake systems must seal properly to ensure the safety and reliability of the braking system. Understanding the sealing mechanism, potential failure points, and best practices for installation and maintenance are essential for preventing leaks and maintaining optimal braking performance. Regular inspection, proper maintenance, and the use of high-quality components are critical for ensuring the safety and effectiveness of your vehicle's braking system. Never compromise on safety; prioritize proper installation and regular inspection to prevent catastrophic consequences.
Latest Posts
Latest Posts
-
Vocabulary Power Plus Level 11 Answer Key Pdf
Apr 18, 2025
-
A Food Handler Cleans Up A Spill
Apr 18, 2025
-
Unit 6 Progress Check Frq Ap Bio
Apr 18, 2025
-
Incorrect Horizontal Angulation Of The Pid Results In
Apr 18, 2025
-
Based On What You See In The Employee Complaint Log
Apr 18, 2025
Related Post
Thank you for visiting our website which covers about Sae Flare Fittings Used On Hydraulic Brake Systems Must ________. . We hope the information provided has been useful to you. Feel free to contact us if you have any questions or need further assistance. See you next time and don't miss to bookmark.