The Installation Of Production Improvement Option D
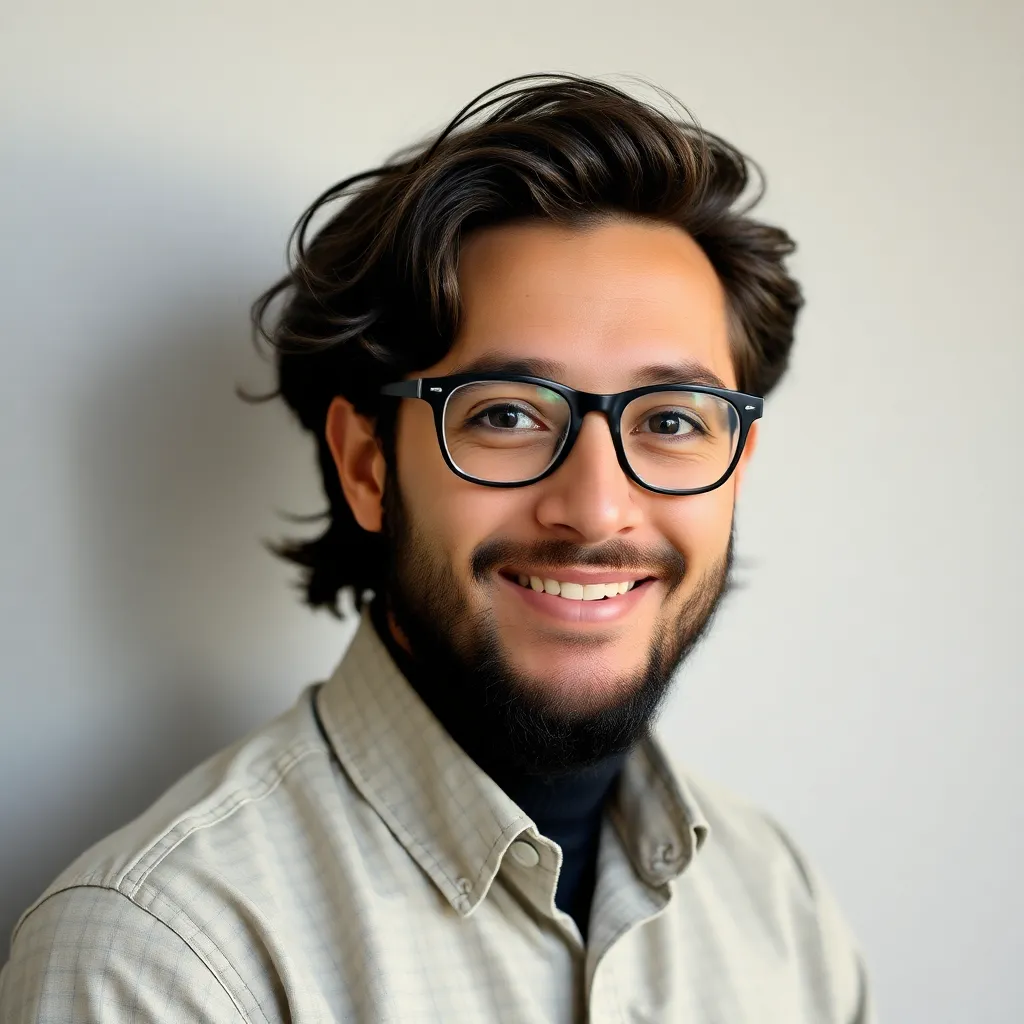
Breaking News Today
May 09, 2025 · 6 min read
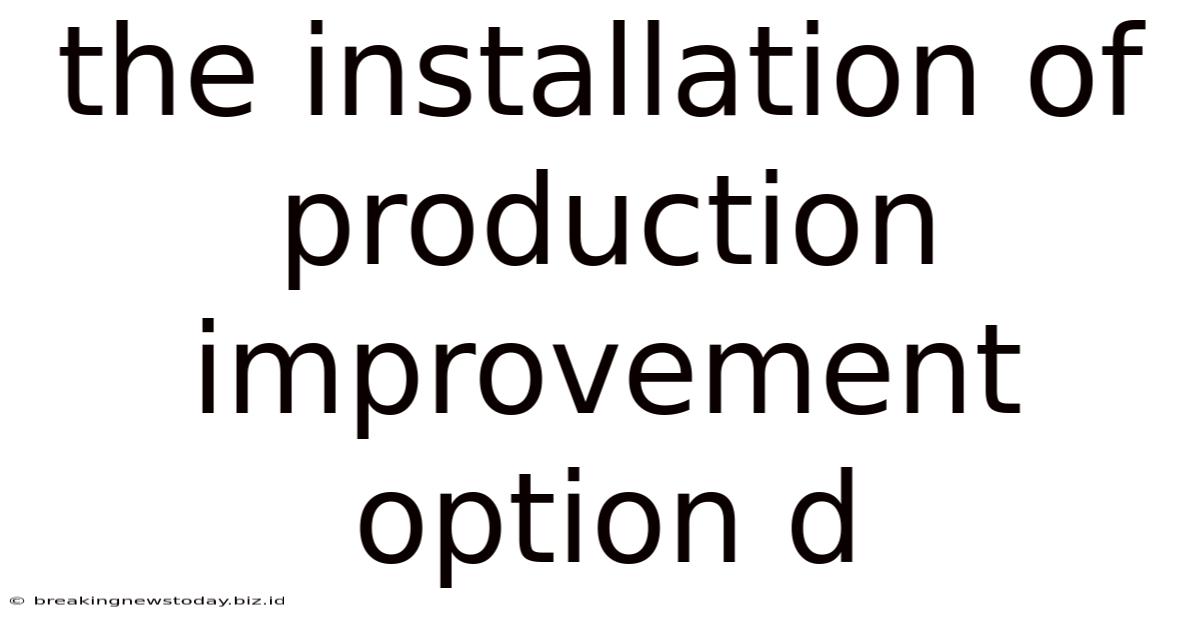
Table of Contents
The Installation of Production Improvement Option D: A Comprehensive Guide
Production Improvement Option D (PIO-D) represents a significant upgrade for many manufacturing processes. Its installation, however, requires careful planning and execution to ensure seamless integration and maximum performance gains. This comprehensive guide details the entire process, from initial assessment to post-installation verification. We'll cover everything you need to know for a successful PIO-D implementation.
Phase 1: Pre-Installation Assessment and Planning
Before even considering the physical installation, a thorough pre-installation assessment is crucial. This phase sets the foundation for a smooth and efficient process. Neglecting this step often leads to unforeseen complications and delays.
1.1 Needs Analysis and Justification:
- Identify Bottlenecks: Pinpoint the specific areas of your production line where PIO-D will deliver the most significant improvements. This might involve analyzing production data, identifying bottlenecks, and assessing current efficiency levels. Quantifiable data is essential here – showing a clear ROI is critical for securing approval for the project.
- Defining Objectives: Clearly articulate the specific goals you aim to achieve with PIO-D. These might include increased production output, reduced downtime, improved product quality, or lower operating costs. Specific, Measurable, Achievable, Relevant, and Time-bound (SMART) goals are essential.
- Resource Allocation: Determine the resources needed for the installation, including personnel, tools, materials, and budget. This includes allocating sufficient time for training staff on the new system. Underestimating resource requirements is a common mistake.
1.2 Site Preparation and Infrastructure Review:
- Space Requirements: Ensure adequate space is available for the installation and subsequent operation of PIO-D. This involves considering physical dimensions, accessibility, and potential interference with existing equipment. Detailed floor plans and 3D models can be incredibly helpful.
- Power and Utilities: Verify that sufficient power, compressed air, and other utilities are available to support the new system. This might require upgrades to your existing infrastructure, including electrical panels, wiring, and air compressor capacity. Consult with a qualified electrician and other relevant specialists.
- Safety Assessment: Conduct a thorough risk assessment to identify potential safety hazards during the installation process. Implement appropriate safety measures, including personal protective equipment (PPE), lockout/tagout procedures, and emergency response plans. Safety should be paramount throughout the entire project.
1.3 Team Formation and Training:
- Assemble the Right Team: Form a dedicated team consisting of experienced technicians, engineers, and project managers. The team's composition should reflect the diverse skill sets needed for a smooth installation. Clear roles and responsibilities must be defined.
- Comprehensive Training: Provide comprehensive training to all team members involved in the installation and operation of PIO-D. This should cover the system's technical aspects, safety procedures, and troubleshooting techniques. Hands-on training is often the most effective approach.
- Documentation: Thoroughly document all aspects of the pre-installation phase, including needs analysis, site preparation, team assignments, and training records. This documentation will serve as a valuable reference throughout the installation process and beyond.
Phase 2: Installation and Integration
This phase involves the physical installation of PIO-D and its integration into your existing production system. Precision and meticulousness are crucial to prevent errors and delays.
2.1 Unpacking and Inspection:
- Careful Unpacking: Unpack all components of PIO-D carefully and systematically. Check for any damage incurred during shipping and report any discrepancies immediately to the supplier. Photos and detailed reports are essential.
- Component Verification: Verify that all components are present and match the specifications outlined in the installation manual. Compare the received components against the original order and ensure everything is accounted for.
- Quality Control: Conduct a thorough inspection of all components to ensure they meet the required quality standards. This is a critical step in preventing future problems.
2.2 Physical Installation:
- Follow Installation Manual: Strictly adhere to the manufacturer's installation manual. Deviating from these instructions can lead to malfunction, safety hazards, and voiding the warranty.
- Sequential Installation: Install the components in the correct sequence as outlined in the manual. This ensures proper functionality and prevents potential conflicts between different parts of the system.
- Precise Alignment: Ensure precise alignment and positioning of all components. Improper alignment can affect the system's performance and may cause damage. Use precise measuring tools and levelers.
2.3 System Integration:
- Connect to Existing Systems: Carefully connect PIO-D to your existing production systems, including control systems, power supplies, and communication networks. This may involve electrical wiring, network cabling, and software configuration.
- Software Configuration: Configure the software settings of PIO-D to match your specific production requirements. This might involve setting parameters, defining production schedules, and configuring data logging features. Expert assistance may be required for this step.
- Testing and Calibration: Thoroughly test and calibrate the newly installed system to ensure it's functioning correctly and meeting performance specifications. This may involve running test batches, collecting data, and fine-tuning settings.
Phase 3: Post-Installation Verification and Optimization
After the installation, a rigorous verification and optimization phase is critical for maximizing the benefits of PIO-D.
3.1 Performance Testing:
- Comprehensive Testing: Conduct comprehensive performance testing to verify that PIO-D is meeting its specified performance targets. This might involve measuring production rates, assessing product quality, and analyzing energy consumption.
- Data Analysis: Analyze the collected data to identify any areas for improvement. This might involve identifying bottlenecks, optimizing settings, or addressing any unforeseen issues.
- Comparative Analysis: Compare the performance of the production line before and after the installation of PIO-D to quantify the improvements achieved. This demonstrates the ROI of the project.
3.2 Operator Training and Support:
- Hands-on Training: Provide hands-on training to operators on how to use and maintain PIO-D. This should cover basic operation, troubleshooting procedures, and safety protocols.
- Ongoing Support: Provide ongoing technical support and maintenance to ensure the system continues to function efficiently. This might involve regular maintenance checks, software updates, and troubleshooting assistance.
- Feedback Mechanisms: Establish feedback mechanisms to gather input from operators and other stakeholders. This input can help identify areas for improvement and ensure the system meets the needs of the users.
3.3 Ongoing Monitoring and Maintenance:
- Regular Monitoring: Regularly monitor the performance of PIO-D to identify any potential issues and address them promptly. This may involve using monitoring software, collecting data, and conducting routine inspections.
- Preventative Maintenance: Implement a preventative maintenance program to minimize downtime and extend the lifespan of the system. This might involve regular cleaning, lubrication, and part replacements.
- Continuous Improvement: Continuously strive to optimize the performance of PIO-D through ongoing monitoring, data analysis, and process improvements. This ensures maximum return on investment and sustained performance gains.
Conclusion:
The successful installation of Production Improvement Option D requires meticulous planning, careful execution, and a commitment to continuous improvement. By following the steps outlined in this guide, you can ensure a smooth installation, maximize performance gains, and achieve a significant return on your investment. Remember that thorough documentation and a proactive approach to maintenance are crucial for long-term success. Always prioritize safety throughout the entire process. The result will be a more efficient, productive, and profitable operation.
Latest Posts
Latest Posts
-
Arkansas Notary Public Test Questions And Answers
May 11, 2025
-
The Us Public Health Service Requires Institutions To
May 11, 2025
-
In 1921 Picric Acid Was Used As A
May 11, 2025
-
Which Best Describes The Protein Requirement During Pregnancy
May 11, 2025
-
Optical Scanners Recognize Individual Letters Or Images
May 11, 2025
Related Post
Thank you for visiting our website which covers about The Installation Of Production Improvement Option D . We hope the information provided has been useful to you. Feel free to contact us if you have any questions or need further assistance. See you next time and don't miss to bookmark.