The Quality Control Manager Of A Large Factory
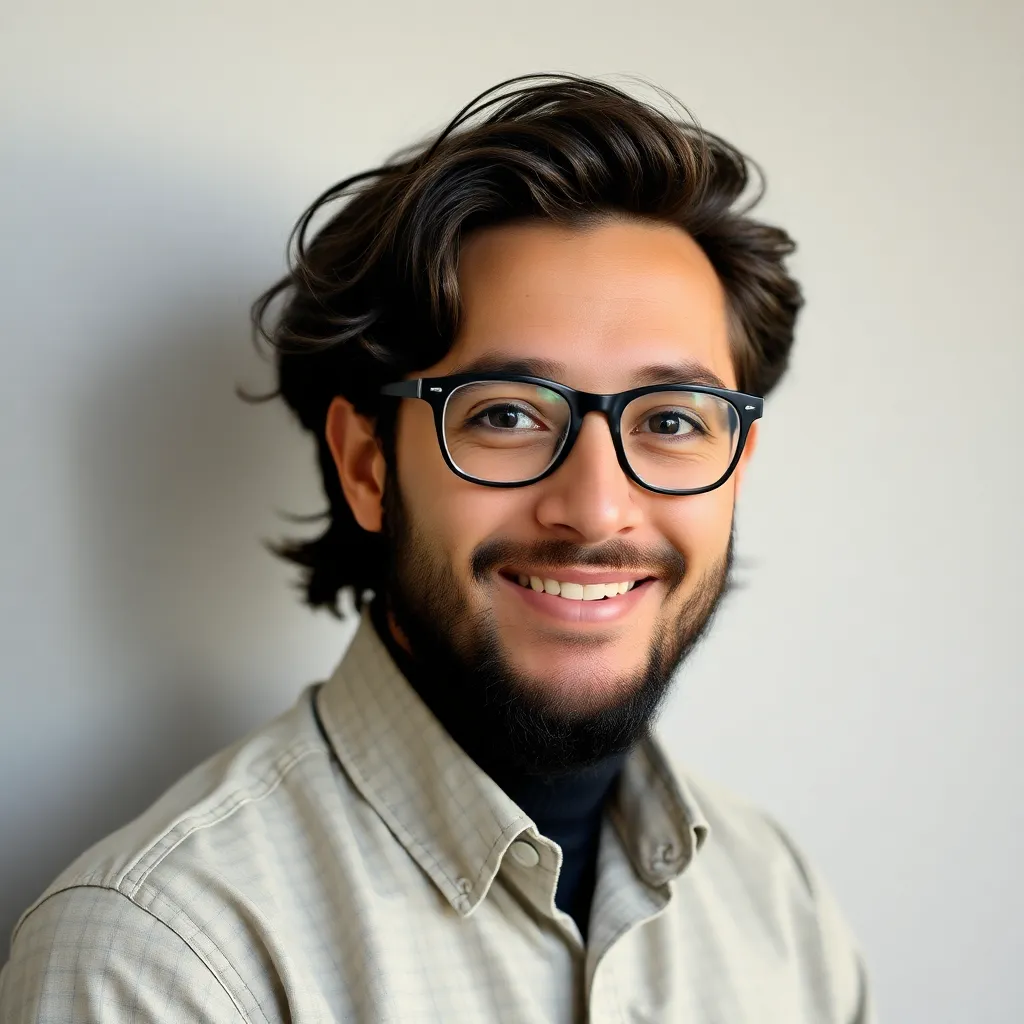
Breaking News Today
Mar 14, 2025 · 6 min read
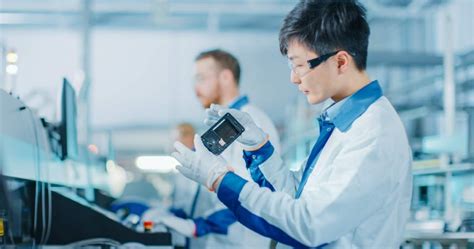
Table of Contents
A Day in the Life: The Quality Control Manager of a Large Factory
The hum of machinery, the rhythmic clatter of production, the constant flow of materials – these are the soundscapes of a large factory. But behind the scenes, ensuring the smooth operation and the unwavering quality of the output, is a critical role: the Quality Control Manager. This individual is the guardian of standards, the champion of excellence, and the silent force behind the success of the entire operation. This in-depth article will explore the multifaceted responsibilities, challenges, and rewards of this demanding yet vital position.
The Scope of Responsibilities: Beyond Simple Inspection
The role of a Quality Control (QC) Manager in a large factory extends far beyond simple product inspection. It's a multifaceted role encompassing strategic planning, team management, problem-solving, and continuous improvement. Let's delve into the key areas:
1. Setting and Maintaining Quality Standards: The Foundation of Excellence
The QC Manager is responsible for establishing and enforcing rigorous quality standards across all aspects of the production process. This involves:
- Defining Specifications: Working closely with engineering, design, and procurement teams to define clear, measurable, achievable, relevant, and time-bound (SMART) quality specifications for raw materials, work-in-progress, and finished goods.
- Developing Quality Control Plans: Creating comprehensive plans that outline the methods and procedures for inspecting and testing products at various stages of production. These plans must be meticulously documented and easily accessible to all relevant personnel.
- Implementing Quality Management Systems (QMS): Implementing and maintaining a robust QMS, such as ISO 9001, to ensure consistent adherence to quality standards and regulatory requirements. This involves regular audits, documentation reviews, and corrective action plans.
- Staying Updated on Industry Best Practices: The QC Manager must remain abreast of the latest advancements in quality control techniques, technologies, and industry standards to maintain a competitive edge and ensure the company's products meet or exceed expectations.
2. Leading and Managing the Quality Control Team: Fostering a Culture of Quality
Effective leadership is crucial in a QC department. The manager is responsible for:
- Recruiting and Training: Selecting qualified personnel, providing comprehensive training on quality control procedures, and fostering a culture of continuous learning and development.
- Performance Management: Setting clear performance goals, providing regular feedback, and conducting performance evaluations to ensure team members meet expectations and contribute to the overall success of the department.
- Team Motivation and Collaboration: Creating a positive and supportive work environment where team members feel valued, respected, and empowered to contribute their best work. This often involves cross-departmental collaboration to proactively identify and address potential quality issues.
- Conflict Resolution: Addressing conflicts and disagreements effectively and fairly, ensuring the smooth operation of the QC team and its interaction with other departments.
3. Proactive Problem Solving and Continuous Improvement: The Engine of Efficiency
The QC Manager is not just reactive; they are proactive in identifying and resolving quality issues. This involves:
- Root Cause Analysis: Employing techniques such as the "5 Whys" or fishbone diagrams to identify the root causes of quality defects and implement corrective actions to prevent recurrence.
- Data Analysis and Reporting: Analyzing quality data to identify trends, patterns, and areas for improvement. Regular reporting to management on key quality metrics is crucial for informed decision-making.
- Implementing Corrective and Preventive Actions (CAPA): Developing and implementing effective CAPA plans to address identified quality issues and prevent them from happening again. This is a critical aspect of maintaining a robust QMS.
- Lean Manufacturing Principles: Applying Lean manufacturing principles to identify and eliminate waste, streamline processes, and improve overall efficiency.
4. Supplier Management: Ensuring Consistent Quality from the Source
The quality of raw materials and components significantly impacts the final product. The QC Manager plays a vital role in:
- Supplier Audits: Conducting regular audits of suppliers to assess their quality management systems and ensure they meet the company's requirements.
- Supplier Performance Monitoring: Tracking supplier performance, identifying areas for improvement, and working collaboratively with suppliers to address any quality concerns.
- Supplier Selection and Development: Participating in the selection process of new suppliers and providing support to help existing suppliers improve their quality systems.
5. Regulatory Compliance and Safety: Meeting Legal and Ethical Standards
The QC Manager is responsible for ensuring the company's products meet all relevant regulatory requirements and safety standards. This involves:
- Staying Informed on Regulations: Staying updated on changes in industry regulations, safety standards, and legal requirements.
- Implementing Compliance Programs: Developing and implementing programs to ensure compliance with relevant regulations and standards.
- Handling Non-Compliance Issues: Addressing any instances of non-compliance promptly and effectively, ensuring the company operates within the legal and ethical framework.
The Challenges Faced by a Quality Control Manager
The role of a QC Manager is not without its challenges. These include:
- Balancing Quality and Productivity: The constant tension between maintaining high quality standards and meeting production targets requires skillful negotiation and prioritization.
- Managing Conflicting Priorities: Juggling multiple tasks and priorities, often with tight deadlines and limited resources.
- Dealing with Resistance to Change: Overcoming resistance to change from employees who may be resistant to new quality control procedures or technologies.
- Maintaining Employee Morale: Keeping the team motivated and engaged, especially in the face of challenging situations.
- Managing Budget Constraints: Operating within a budget and making strategic decisions about resource allocation.
- Technological Advancements: Staying current with rapid technological changes in quality control equipment and software.
The Rewards of a Rewarding Career
Despite the challenges, the role of a QC Manager offers significant rewards:
- Making a Tangible Difference: The opportunity to directly impact the quality and safety of products used by people worldwide.
- Continuous Learning and Development: The constant exposure to new technologies, techniques, and industry best practices keeps the role intellectually stimulating.
- Leadership Opportunities: The chance to lead and mentor a team, fostering a culture of excellence and continuous improvement.
- Problem-Solving and Critical Thinking: The ability to apply analytical skills and critical thinking to solve complex problems and improve processes.
- Job Security: High demand for qualified QC Managers in various industries, ensuring job security and career growth.
Skills and Qualifications: The Essential Toolkit
To excel in this role, a QC Manager needs a blend of technical skills, leadership qualities, and soft skills. These include:
- Strong understanding of quality management principles and methodologies (e.g., Six Sigma, Lean Manufacturing).
- Proficiency in statistical process control (SPC) and data analysis techniques.
- Experience with quality management systems (e.g., ISO 9001).
- Excellent communication, interpersonal, and teamwork skills.
- Strong leadership and management skills.
- Problem-solving and analytical skills.
- Experience with various quality control tools and techniques.
- Knowledge of relevant industry regulations and safety standards.
- Proficiency in relevant software applications (e.g., ERP systems, statistical software).
Conclusion: The Unsung Hero of Factory Success
The Quality Control Manager is the unsung hero of a large factory. Their work, though often unseen, is crucial to the success and reputation of the organization. They ensure that products meet the highest quality standards, comply with regulations, and ultimately contribute to the satisfaction of customers. This demanding yet fulfilling role requires a unique blend of technical expertise, leadership skills, and a dedication to excellence. The impact of their efforts extends far beyond the factory floor, touching the lives of countless individuals who use the products they help to create. The QC Manager is the silent guardian of quality, ensuring that every product leaving the factory represents the pinnacle of the company's commitment to excellence.
Latest Posts
Latest Posts
-
Life Insurance Exam Questions And Answers Pdf
Mar 18, 2025
-
The Direct Carry Is Used To Transfer A Patient
Mar 18, 2025
-
The Emancipation Proclamation Of January 1 1863 Quizlet
Mar 18, 2025
-
These Cards Will Get You Drunk Quizlet
Mar 18, 2025
-
Did Quizlet Get Rid Of Q Chat
Mar 18, 2025
Related Post
Thank you for visiting our website which covers about The Quality Control Manager Of A Large Factory . We hope the information provided has been useful to you. Feel free to contact us if you have any questions or need further assistance. See you next time and don't miss to bookmark.