Too Much Primary Air Or Will Cause
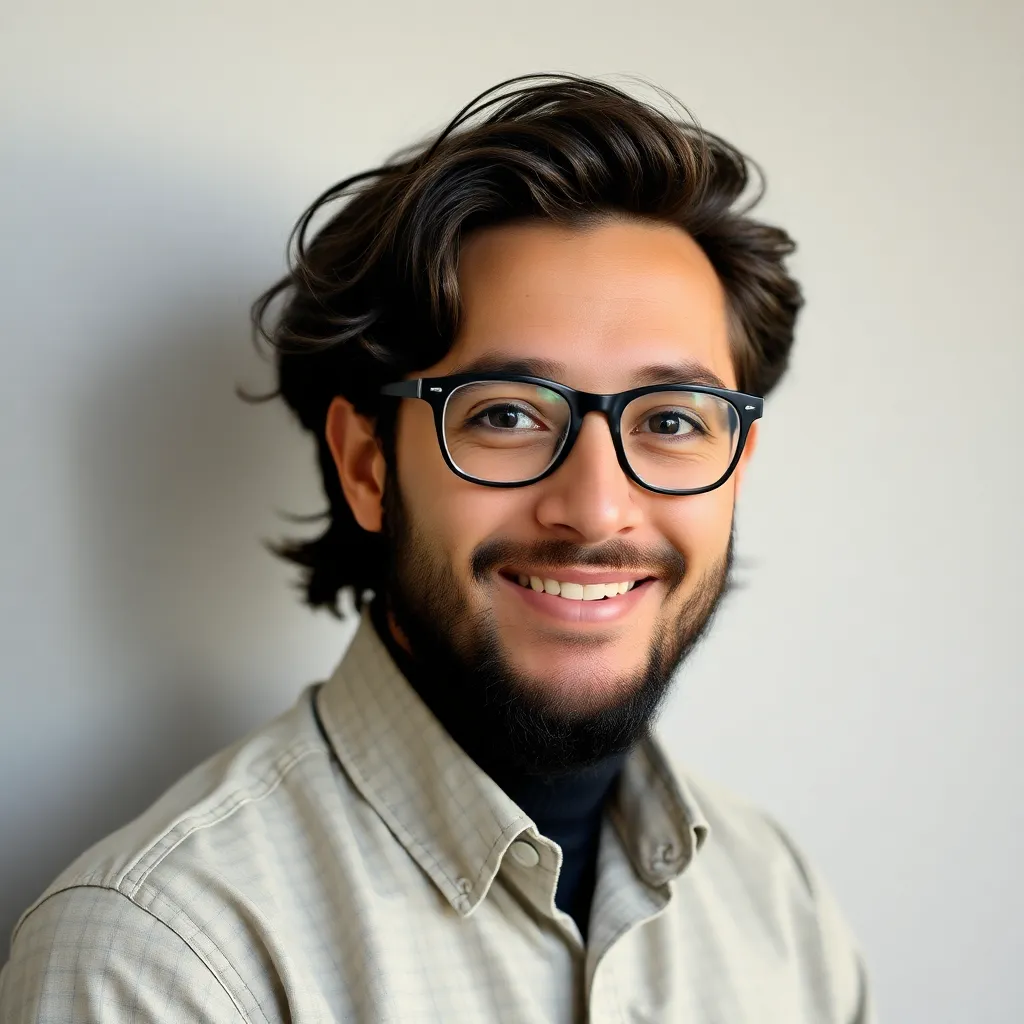
Breaking News Today
Mar 26, 2025 · 6 min read
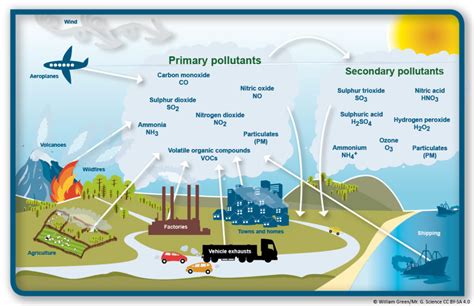
Table of Contents
Too Much Primary Air: Causes, Effects, and Solutions Across Various Systems
Primary air, while essential for various processes, can become detrimental when excessive. This article explores the consequences of excessive primary air across different applications, examining its causes, effects, and potential solutions. We will cover diverse fields, ensuring a comprehensive understanding of this often-overlooked issue.
Understanding Primary Air: A Quick Overview
Before delving into the problems associated with excess primary air, let's establish a basic understanding of its role. Primary air refers to the air introduced into a system before a fuel source is added. This pre-mixed air plays a crucial role in combustion processes, influencing efficiency, emissions, and overall system performance. The optimal amount varies considerably depending on the specific application. Too little, and combustion is incomplete, leading to inefficiency and harmful emissions. Too much, and we encounter the problems discussed below.
The Negative Impacts of Excessive Primary Air: A Cross-Sectional Analysis
The consequences of introducing excessive primary air are far-reaching and impact numerous systems. Let's explore these consequences across various sectors:
1. Combustion Systems (Boilers, Furnaces, Engines):
-
Reduced Combustion Efficiency: Excess primary air dilutes the fuel-air mixture, leading to incomplete combustion. This results in wasted fuel and reduced thermal efficiency. The heat generated is lower than it should be for the amount of fuel consumed. This directly impacts operating costs and potentially leads to higher energy bills.
-
Increased Emissions: Incomplete combustion produces more pollutants. These include carbon monoxide (CO), unburnt hydrocarbons (UHCs), and particulate matter (PM), all harmful to the environment and human health. Regulations regarding emissions are becoming stricter, making managing primary air crucial for compliance.
-
Higher Operating Costs: The combined effects of reduced efficiency and increased maintenance (due to potential fouling and corrosion discussed below) translate directly into higher operating costs for industrial and commercial applications.
-
Increased Heat Loss: The excess air cools the combustion chamber, reducing the overall heat transfer to the working fluid (water in boilers, for instance). This further reduces efficiency.
-
Fouling and Corrosion: Excessive air can increase the rate of corrosion and fouling in combustion chambers and heat exchangers. This necessitates more frequent maintenance and cleaning, further increasing operational expenses and downtime.
Solutions: Implementing advanced combustion controls, such as air-fuel ratio controllers and oxygen sensors, are key to maintaining optimal primary air levels. Regularly scheduled inspections and maintenance of the system are also crucial.
2. Metallurgical Processes (Smelting, Refining):
-
Oxidative Reactions: In metallurgical processes, excess primary air can lead to undesired oxidation reactions. This can alter the chemical composition of the metal, impacting its properties and quality. This is especially critical in the production of high-quality alloys.
-
Increased Energy Consumption: Similar to combustion systems, excess air leads to energy losses due to incomplete reactions and increased cooling of the reaction zone. This translates to higher energy costs and reduced productivity.
-
Material Degradation: The increased oxidation can also lead to the degradation of the furnace lining and other components, requiring expensive repairs and replacements.
Solutions: Precise control of airflow is essential, often requiring sophisticated automation and monitoring systems. Selecting appropriate refractory materials that can withstand the harsh environment created by high temperatures and oxidative reactions is critical.
3. Powder Handling and Processing:
-
Dust Dispersion: Excessive airflow in powder handling systems can lead to increased dust dispersion, creating a hazardous workplace environment and potential for explosions.
-
Equipment Wear: High-velocity airflow caused by excessive primary air can accelerate the wear and tear on equipment components like valves, pipes, and conveying systems.
-
Reduced Process Efficiency: Inaccurate airflow can affect the overall consistency and efficiency of powder processing operations, leading to material losses and reduced product quality.
Solutions: Employing effective dust collection and control mechanisms, such as baghouses or cyclones, is crucial. Regular maintenance and inspections of the equipment, coupled with careful airflow control, are essential for preventing issues.
4. Industrial Drying Processes:
-
Reduced Drying Efficiency: While air is essential in drying, too much can lead to reduced efficiency by excessive cooling and prolonged drying times.
-
Increased Energy Consumption: The prolonged drying times translate into higher energy consumption, increasing operating costs.
-
Product Damage: Overly aggressive airflow can damage delicate products during the drying process.
Solutions: Implementing efficient airflow control systems, and using the correct type of drying equipment (e.g., fluidized bed dryers, spray dryers) that can precisely control airflow are critical. Optimizing the drying process parameters based on the product characteristics is crucial.
5. Wastewater Treatment:
-
Reduced Aeration Efficiency: In wastewater treatment, primary air provides oxygen for aerobic microorganisms. Excess air can lead to inefficient aeration, causing incomplete treatment.
-
Increased Energy Costs: Inefficient aeration translates into higher energy consumption, increasing operational costs.
-
Equipment Damage: High-velocity air can damage aeration equipment.
Solutions: Careful monitoring and control of the aeration process are key. Regular maintenance of the aeration system, alongside the use of efficient aeration equipment, is important. Employing advanced control systems that optimize air flow based on dissolved oxygen levels is vital for optimal performance.
Diagnosing Excess Primary Air: Identifying the Problem
Identifying the problem of excess primary air requires a multi-pronged approach. Common indicators include:
-
High stack temperatures: In combustion processes, higher-than-expected exhaust gas temperatures often indicate inefficient combustion due to excess air.
-
Lower-than-expected heat transfer: If the system isn't producing the expected amount of heat for the fuel consumed, it suggests inefficient combustion.
-
Increased emissions: Higher levels of CO, UHCs, and PM indicate incomplete combustion. Regular emissions monitoring is crucial.
-
Excessive wear and tear on equipment: Damage to equipment components can point to issues with airflow.
-
Operational inefficiencies: Increased downtime, higher energy consumption, and lower product quality point towards underlying problems that may be related to incorrect primary airflow.
-
Visual Inspection: Visible signs of incomplete combustion, like soot or excessive smoke, can help in diagnosing the issue.
Addressing the Issue: Mitigation and Prevention Strategies
Addressing the issue of excessive primary air requires a proactive approach that combines proper design, installation, and maintenance. The strategies often vary depending on the application but include:
-
Advanced Control Systems: Implementing advanced control systems, such as PLC-based controllers and feedback loops using oxygen sensors, allows for precise regulation of primary air flow.
-
Regular Maintenance and Inspection: Regular inspections and preventative maintenance can help identify and address problems early on before they escalate.
-
Proper System Design: Careful design and selection of appropriate equipment can optimize airflow and prevent excessive primary air.
-
Operator Training: Proper training for operators to understand and manage the system is crucial. This includes understanding the indicators of excess primary air and the procedures to address them.
-
Process Optimization: Optimizing the process parameters based on the specific application can minimize the risk of excessive primary air.
Conclusion: The Importance of Primary Air Management
The role of primary air in various systems is undeniable. However, maintaining the optimal amount is critical for efficiency, safety, and environmental compliance. Understanding the causes and consequences of excessive primary air, combined with implementing effective mitigation strategies, is essential for ensuring optimal system performance and minimizing potential negative impacts across various sectors. By employing a proactive approach to primary air management, businesses can improve efficiency, reduce costs, and ensure environmental responsibility. Regular monitoring, preventative maintenance, and operator training remain cornerstones of successful primary air management across all applications.
Latest Posts
Latest Posts
-
Select The Best Strategic Goal For Wirecard
Mar 29, 2025
-
Nosotros Seguir Hablando De Cocina
Mar 29, 2025
-
An Area Organized Into An Independent Political Unit Is A
Mar 29, 2025
-
Most Residential Systems That Use Communicating Controls Use
Mar 29, 2025
-
How Does The Setting In Harrison Bergeron Affect George
Mar 29, 2025
Related Post
Thank you for visiting our website which covers about Too Much Primary Air Or Will Cause . We hope the information provided has been useful to you. Feel free to contact us if you have any questions or need further assistance. See you next time and don't miss to bookmark.