What Gauges Are Used For Measuring Duct Pressure
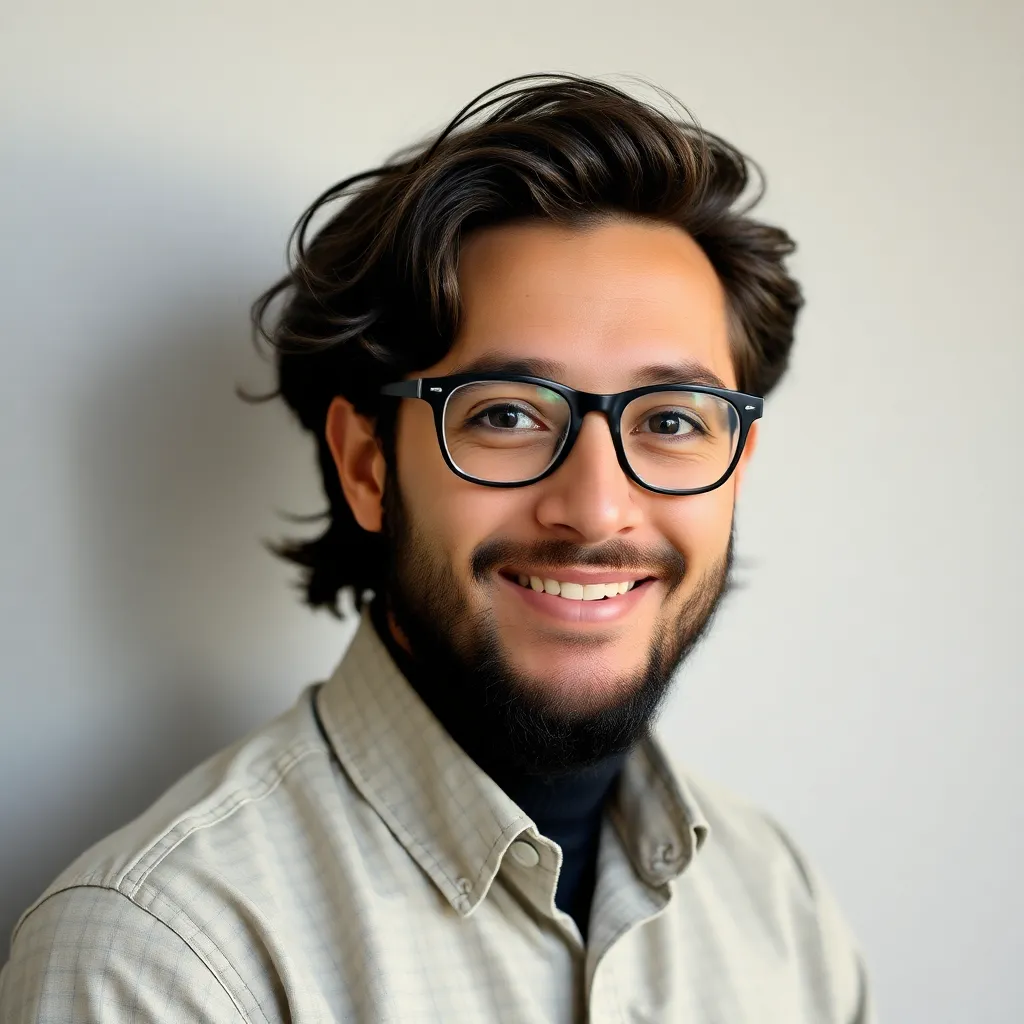
Breaking News Today
Apr 02, 2025 · 6 min read
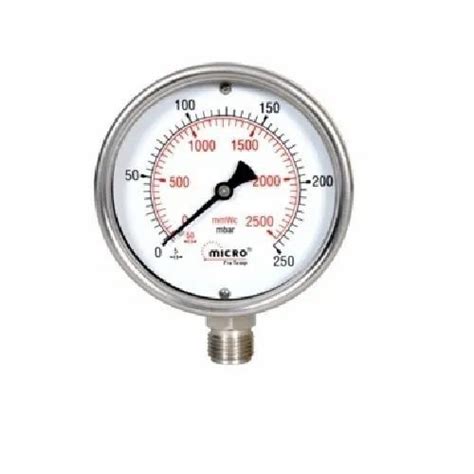
Table of Contents
What Gauges Are Used for Measuring Duct Pressure?
Maintaining optimal airflow in HVAC systems is crucial for efficient heating, cooling, and ventilation. Accurate measurement of duct pressure is essential for troubleshooting problems, ensuring proper system design, and maximizing energy efficiency. But with a variety of gauges available, understanding which one is appropriate for a given task can be challenging. This comprehensive guide explores the different types of gauges used for measuring duct pressure, their applications, advantages, and limitations. We'll delve into the specifics of each, providing you with the knowledge to choose the right tool for the job and ensuring accurate, reliable readings.
Understanding Duct Pressure
Before we dive into the types of gauges, let's clarify what we mean by "duct pressure." In HVAC systems, duct pressure refers to the difference in air pressure between two points within the ductwork. This pressure difference drives the airflow, and deviations from the design specifications can indicate problems. We're primarily concerned with two key pressure measurements:
Static Pressure:
This represents the pressure exerted by the air itself within the duct, independent of its movement. It's a measure of the energy in the air due to its density and position. Static pressure is important for understanding the overall system resistance and identifying blockages or leaks.
Velocity Pressure:
This measures the pressure created by the movement of air within the duct. It's directly related to the air's velocity and is essential for determining airflow rates.
Total Pressure:
Total pressure is the sum of static and velocity pressure. This represents the total energy of the air within the duct system.
Measuring these pressures accurately allows technicians to diagnose issues such as:
- Insufficient airflow: Low pressure readings can indicate restricted airflow due to blockages, leaks, or improper duct sizing.
- Excessive airflow: High pressure readings might signify leaks or an improperly balanced system.
- System imbalances: Discrepancies in pressure between different parts of the system highlight imbalances that need to be addressed.
- Fan performance issues: Pressure readings can help assess fan performance and detect problems such as motor failure or wear and tear.
Types of Gauges for Measuring Duct Pressure
Several types of gauges are used to measure duct pressure in HVAC systems, each with its own strengths and weaknesses.
1. Magnehelic Gauge:
- Description: Magnehelic gauges are differential pressure gauges that utilize a magnetic coupling between a rotating indicator and a diaphragm. The diaphragm deflects proportionally to the pressure difference, and this deflection is translated into a readable scale.
- Advantages: They're highly accurate, durable, and resistant to damage from dust and debris, making them ideal for use in dirty ductwork. They're also relatively inexpensive compared to some other options. They offer a wide range of pressure measurement capabilities, suitable for various HVAC applications.
- Disadvantages: They might be less sensitive to very low-pressure differences. Also, the magnetic coupling mechanism might require periodic calibration to maintain accuracy over time.
- Applications: Measuring static pressure, velocity pressure, and total pressure in HVAC ductwork. Suitable for both low and medium pressure ranges.
2. Inclined Manometer:
- Description: Inclined manometers are simple differential pressure gauges that use a liquid (usually water or oil) column to indicate pressure differences. The inclined tube amplifies the reading, making it easier to read smaller pressure variations.
- Advantages: They're relatively inexpensive and easy to use. Their simple mechanism makes them easy to understand and maintain.
- Disadvantages: They are less accurate than Magnehelic gauges and are easily affected by temperature changes. They are also susceptible to damage and require careful handling. The use of liquids means they're not suitable for dirty or dusty environments.
- Applications: Primarily for measuring static pressure; not as suitable for velocity pressure measurements. Best used in clean environments and for applications where high accuracy isn't crucial.
3. Digital Pressure Gauges:
- Description: Digital pressure gauges utilize electronic sensors to measure pressure differences and display the reading digitally. They typically offer high accuracy and a wide range of measurement capabilities. Many digital gauges provide data logging and communication capabilities for easy data recording and analysis.
- Advantages: High accuracy, easy-to-read digital display, many feature data logging and communication capabilities, potentially better suitability for automated data gathering systems.
- Disadvantages: More expensive than Magnehelic or inclined manometers. Can be sensitive to electrical interference or require battery replacements. The sensor might require periodic calibration to maintain accuracy.
- Applications: Suitable for measuring static, velocity, and total pressure. Particularly useful in situations where precise measurements are needed or when data logging is required for analysis and reporting.
4. Pitot Tube with Manometer:
- Description: A Pitot tube is a flow measurement device used to measure velocity pressure. It consists of two openings: one facing the airflow (measuring stagnation pressure) and one perpendicular to it (measuring static pressure). The difference between these pressures is used to calculate the air velocity. A manometer (often an inclined manometer or digital pressure gauge) is used to measure the pressure difference.
- Advantages: Provides direct measurement of velocity pressure, essential for airflow calculations. Relatively inexpensive, especially when using a simple inclined manometer.
- Disadvantages: Requires careful insertion of the Pitot tube into the ductwork to ensure accurate readings. Readings might be affected by turbulence within the ductwork. The accuracy depends on the accuracy of the manometer being used.
- Applications: Used specifically for measuring velocity pressure, which is then used in conjunction with static pressure readings to calculate total pressure and airflow rates.
5. Pressure Transducers:
- Description: Pressure transducers are electronic sensors that convert pressure differences into electrical signals. These signals are then processed to provide a digital readout of pressure. They're often integrated into more sophisticated HVAC monitoring and control systems.
- Advantages: High accuracy and precision, fast response times, suitable for integration with building management systems (BMS).
- Disadvantages: Relatively expensive, requires specialist knowledge for installation and calibration. Might be more susceptible to electronic interference.
- Applications: Used in advanced HVAC systems for continuous monitoring and control of duct pressures. Suitable for automated data acquisition and integration into larger monitoring networks.
Choosing the Right Gauge
Selecting the appropriate gauge depends on various factors, including:
- Accuracy required: For critical applications demanding high accuracy, digital pressure gauges or pressure transducers are preferred. For less critical applications, a Magnehelic gauge or inclined manometer might suffice.
- Budget: Inclined manometers are the most economical option, while pressure transducers represent the most expensive.
- Environment: For dusty or dirty environments, a Magnehelic gauge is more robust than an inclined manometer.
- Type of pressure measurement: Pitot tubes are specifically designed for velocity pressure measurements, while other gauges can measure static and total pressure.
- Integration with other systems: For systems requiring automated data logging and integration with BMS, digital pressure gauges or pressure transducers are ideal.
Calibration and Maintenance
Regardless of the type of gauge used, regular calibration and maintenance are essential for ensuring accurate readings. Calibration should be performed according to the manufacturer's instructions, typically using certified pressure sources. Regular cleaning, especially for gauges used in dirty environments, will prevent buildup of dust and debris that could affect accuracy.
Conclusion
Accurate duct pressure measurement is crucial for efficient and effective HVAC system operation. By understanding the various types of gauges available and their respective strengths and weaknesses, HVAC technicians and building professionals can select the most suitable tool for each specific task. This leads to improved system performance, enhanced energy efficiency, and reduced operational costs. Remember that proper calibration and maintenance are vital for maintaining the accuracy and longevity of any pressure measuring device. With the right tools and techniques, maintaining optimal airflow becomes much more manageable.
Latest Posts
Latest Posts
-
Which Type Of Testing Involves One Ear
Apr 03, 2025
-
Rn Learning System Medical Surgical Renal And Urinary Practice Quiz
Apr 03, 2025
-
What Is The Password For The Companyinfo Zip Hash
Apr 03, 2025
-
A Sign Of Intoxication Could Be A Guest
Apr 03, 2025
-
Which Statement Accurately Describes Long Term Environmental Changes
Apr 03, 2025
Related Post
Thank you for visiting our website which covers about What Gauges Are Used For Measuring Duct Pressure . We hope the information provided has been useful to you. Feel free to contact us if you have any questions or need further assistance. See you next time and don't miss to bookmark.