Which Medium Uses The Lost-wax Casting Method
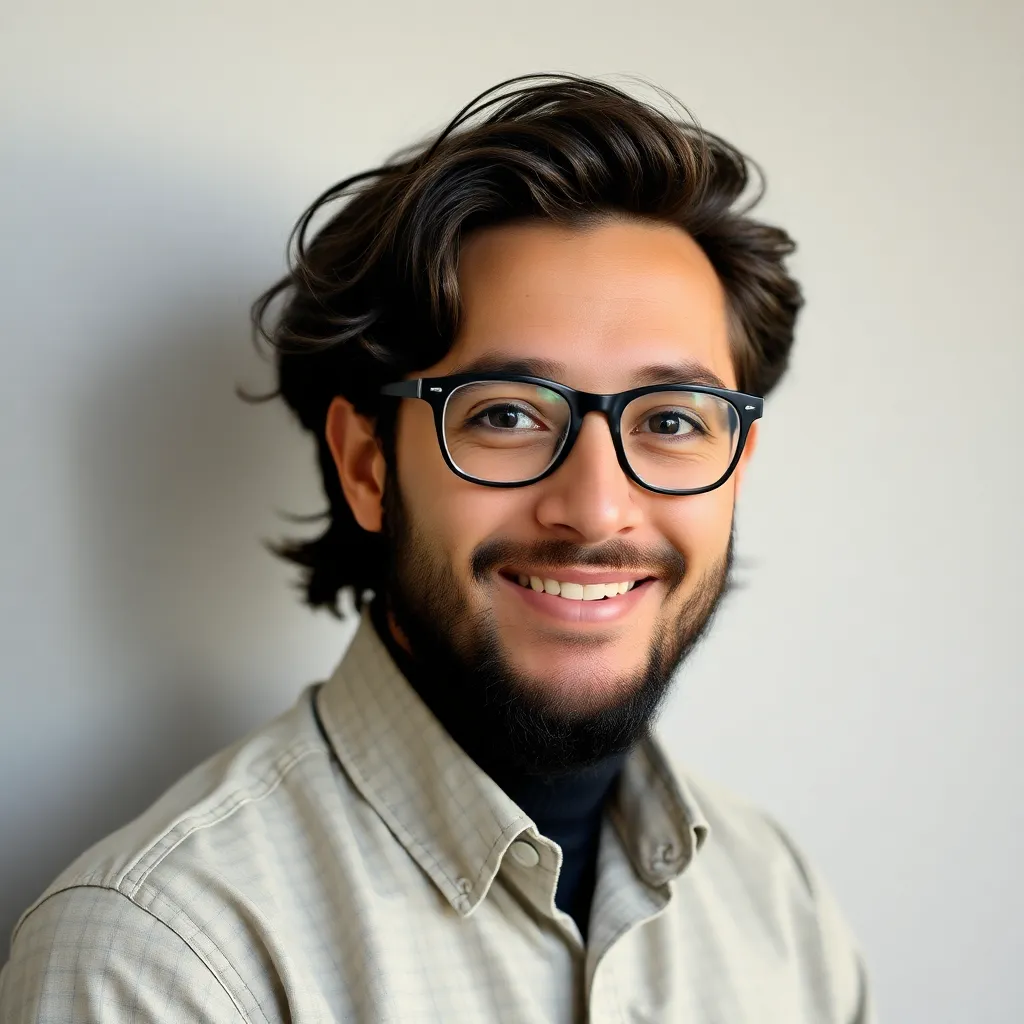
Breaking News Today
Mar 26, 2025 · 7 min read
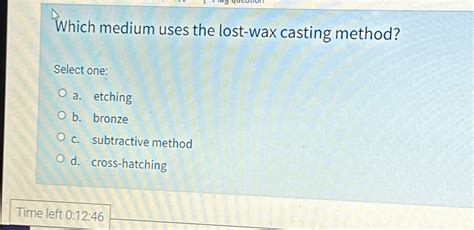
Table of Contents
Which Medium Uses the Lost-Wax Casting Method? A Comprehensive Guide
Lost-wax casting, also known as investment casting, is an ancient and remarkably versatile method for creating intricate metal objects. Its enduring popularity stems from its ability to produce highly detailed pieces in a wide range of metals, making it a cornerstone technique across various artistic and industrial sectors. But which mediums exactly utilize this fascinating process? Let's delve into the diverse applications of lost-wax casting.
The Lost-Wax Casting Process: A Brief Overview
Before exploring the mediums, it's helpful to understand the fundamental steps involved in lost-wax casting. This ancient technique, with evidence dating back to the 4th millennium BC, involves several key stages:
1. Creating the Wax Model:
The process begins with crafting a model of the desired object using wax. This can be done by hand-carving, molding, or using 3D-printed wax patterns, depending on the complexity and desired level of precision.
2. The Sprue and Runners System:
A system of sprues (channels) and runners (smaller channels) is attached to the wax model. These pathways allow molten metal to flow into the mold cavity during casting.
3. Investment Coating:
The wax model, with its sprues and runners, is carefully coated in layers of a refractory investment material, typically a ceramic slurry. This investment acts as a mold, hardening around the wax.
4. Burnout:
The investment-covered wax model is then heated in a kiln, carefully melting and removing the wax. This leaves behind a hollow cavity within the hardened investment mold, precisely mirroring the original wax model.
5. Metal Pouring:
Molten metal is poured into the cavity created by the burnout process. The metal fills the mold, taking on the precise shape of the original wax model.
6. Cooling and Removal:
Once the metal has cooled and solidified, the investment mold is carefully broken away, revealing the finished metal casting. This final stage often includes cleaning and finishing processes to remove any residual investment and achieve the desired surface quality.
Mediums Utilizing Lost-Wax Casting: A Diverse Spectrum
The versatility of lost-wax casting allows its use across a wide array of mediums and applications. Let's explore some of the key areas:
1. Jewelry and Ornamental Arts:
This is arguably the most prominent application of lost-wax casting. The technique's precision and ability to create intricate details make it ideal for:
-
Fine Jewelry: From delicate necklaces and earrings to elaborate rings and brooches, lost-wax casting allows jewelers to create pieces with intricate designs and textures that would be impossible to achieve through other methods. Precious metals like gold, silver, and platinum are commonly used.
-
Sculptural Jewelry: Larger, more sculptural pieces that push the boundaries of traditional jewelry design often rely on lost-wax casting to achieve their complex forms.
-
Ornamental Objects: Beyond jewelry, the method is employed to produce decorative items such as figurines, decorative elements for furniture, and other artistic creations.
2. Dental and Medical Applications:
The precision of lost-wax casting also extends into the medical field, where it's crucial for creating:
-
Dental Crowns and Bridges: Lost-wax casting is essential for producing accurate and durable dental restorations, ensuring a precise fit and natural appearance.
-
Surgical Implants: While other methods are used, lost-wax casting can be employed to produce custom-designed implants with intricate geometries.
-
Medical Instruments: The process can create highly detailed medical instruments requiring specific shapes and tolerances.
3. Industrial Manufacturing:
Beyond the artistic and medical fields, lost-wax casting plays a vital role in industrial manufacturing:
-
Turbine Blades: The aerospace industry utilizes lost-wax casting to produce turbine blades with intricate internal cooling channels, essential for high-performance engines. The ability to create complex shapes with thin walls makes it a preferred method.
-
Automotive Components: Various automotive parts, such as intricate engine components or decorative trim pieces, can be produced using this method.
-
Precision Engineering: Any application requiring highly accurate and detailed metal parts can benefit from lost-wax casting, including components for electronics, machinery, and other precision equipment.
4. Sculpture and Art:
The lost-wax casting method has been a cornerstone of sculpture for millennia, enabling artists to realize their creative visions in metal:
-
Bronze Sculptures: Bronze, with its durability and aesthetic qualities, is a popular choice for large-scale sculptures and smaller works, often cast using the lost-wax method.
-
Other Metal Sculptures: Beyond bronze, lost-wax casting can be used with other metals, such as aluminum, brass, and silver, to produce a wide variety of sculptural forms.
-
Casting Multiple Parts: The process allows the creation of sculptures with multiple components, which are then assembled.
5. Reproducing Existing Objects:
Lost-wax casting also finds use in reproducing existing objects:
-
Museum Replicas: The precise nature of the casting method makes it ideal for creating accurate replicas of ancient artifacts and other historically significant objects.
-
Limited Edition Pieces: Artists can use lost-wax casting to create limited-edition replicas of their original sculptures or other artworks.
Materials Used in Lost-Wax Casting: Metals and Investment
The choice of material significantly impacts the final product. Let’s look at the key material aspects:
Metals:
The versatility of lost-wax casting allows for casting a broad range of metals, including:
-
Precious Metals: Gold, silver, platinum, and palladium are frequently used in jewelry and high-value applications due to their aesthetic qualities and resistance to corrosion.
-
Base Metals: Bronze (an alloy of copper and tin), brass (copper and zinc), aluminum, and nickel are frequently employed for industrial and artistic applications due to their strength, cost-effectiveness, and other desirable properties.
-
Specialty Alloys: Lost-wax casting enables the use of specialty alloys designed for specific applications, such as those with high strength, corrosion resistance, or specific thermal properties.
Investment Materials:
The investment material surrounding the wax model plays a critical role in the casting process. The properties of the investment influence the quality of the final casting:
-
Ceramic-Based Investments: These are the most common type, composed of refractory materials that can withstand high temperatures during the burnout process. They provide stability and detail reproduction.
-
Types of Ceramic Investments: Different formulations exist, each with varying properties to accommodate different metals and casting needs.
-
Investment Preparation: The correct mixing and application of the investment material are crucial to the success of the casting.
Advantages and Disadvantages of Lost-Wax Casting
Like any manufacturing process, lost-wax casting possesses both advantages and disadvantages:
Advantages:
-
High Detail and Accuracy: The process excels at producing highly intricate and accurate castings, even with thin walls and complex geometries.
-
Versatility of Metals: A wide range of metals can be cast using this technique.
-
Complex Shapes: It readily accommodates the creation of complex shapes and geometries that might be difficult or impossible to produce with other methods.
-
Suitable for Small and Large Castings: The process is adaptable to both small-scale jewelry items and large-scale sculptures.
Disadvantages:
-
Labor-Intensive: The process requires multiple steps and significant manual labor, particularly for intricate designs or larger castings.
-
Cost: The investment in equipment, materials, and labor can be substantial, especially for complex projects.
-
Waste Generation: The process generates waste materials, including the investment and the wax. Sustainable practices are becoming increasingly important to mitigate this aspect.
-
Mold Breakage: The investment mold can sometimes break during the casting or cooling process, leading to casting defects or loss of the metal.
Conclusion: A Timeless Technique with Enduring Relevance
Lost-wax casting remains a highly valuable technique across a remarkable range of mediums, from fine jewelry to large-scale industrial applications. Its ability to create highly detailed and accurate metal castings in various metals ensures its continued use in both artistic and industrial contexts. Understanding the process, its advantages and disadvantages, and the range of mediums that utilize it provides a crucial foundation for appreciating the significance of this ancient and enduring technique. The ongoing development of new materials and techniques, coupled with advances in 3D printing for wax model creation, ensures that lost-wax casting will continue to evolve and find new applications in the future.
Latest Posts
Latest Posts
-
A 13 Year Old Girl Tells You
Mar 26, 2025
-
Explain How Human Impact Can Lead To Succession In Ecosystems
Mar 26, 2025
-
How Much Should Montrel Expect To Pay
Mar 26, 2025
-
A Form Letter Would Not Be Appropriate For
Mar 26, 2025
-
A 67 Year Old Man Is Found Unresponsive
Mar 26, 2025
Related Post
Thank you for visiting our website which covers about Which Medium Uses The Lost-wax Casting Method . We hope the information provided has been useful to you. Feel free to contact us if you have any questions or need further assistance. See you next time and don't miss to bookmark.