Hoses And Hose Connections Should Be Able To Withstand
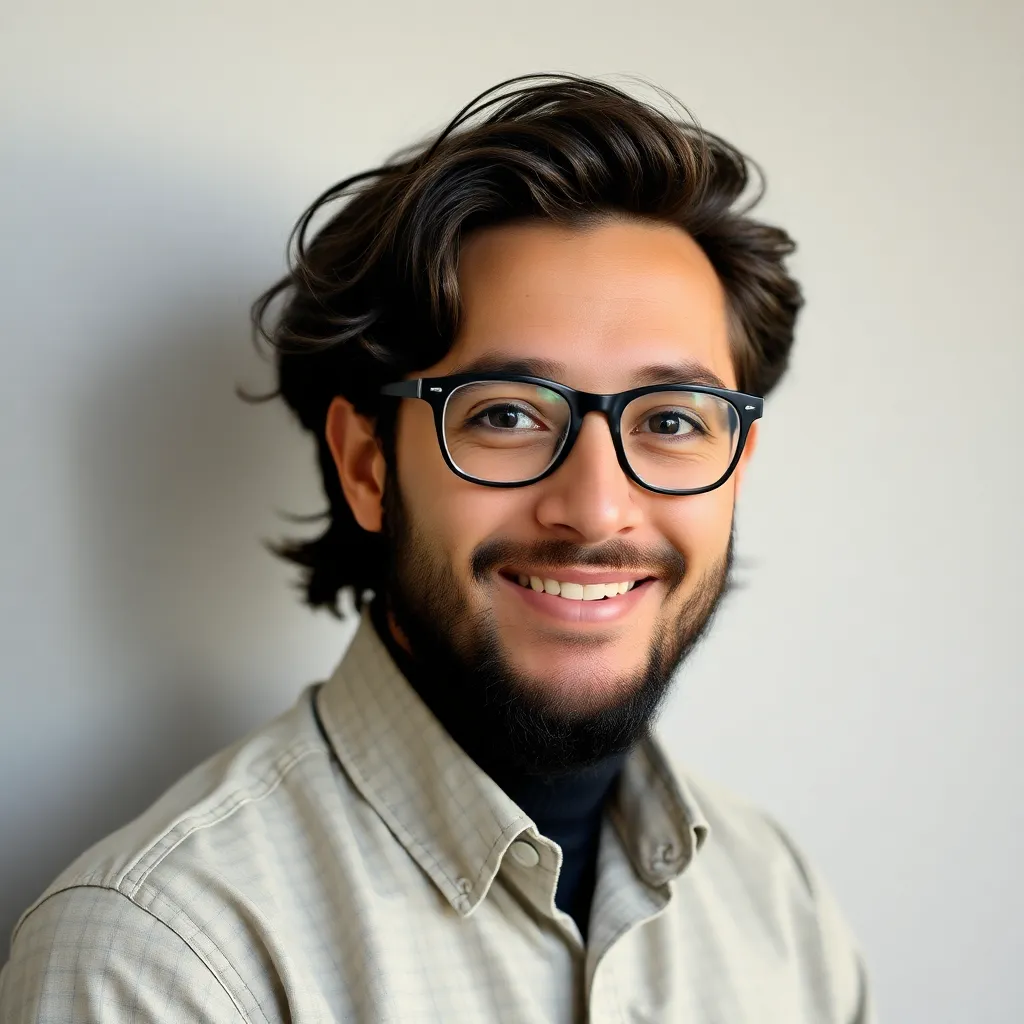
Breaking News Today
Mar 16, 2025 · 7 min read
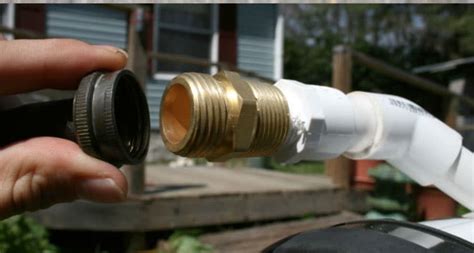
Table of Contents
Hoses and Hose Connections: Withstanding the Test of Pressure, Temperature, and Time
Hoses and their connections are ubiquitous in countless industries and applications, from industrial manufacturing and agriculture to automotive repair and everyday household use. Their seemingly simple design belies the crucial role they play in safely and efficiently transferring fluids, gases, and even solids. However, the effectiveness of any hose system hinges on its ability to withstand a range of demanding conditions. This article delves deep into the critical factors hoses and their connections must endure, exploring the materials, designs, and testing procedures that ensure reliable performance and prevent catastrophic failures.
The Critical Factors: Pressure, Temperature, and Chemical Compatibility
The performance of a hose system is fundamentally determined by its ability to withstand three primary factors: pressure, temperature, and chemical compatibility. Each of these factors interacts in complex ways, and understanding their individual and combined effects is paramount to selecting and implementing the appropriate hose and fitting for a given application.
1. Pressure Resistance: The Backbone of Hose Integrity
Pressure resistance is arguably the most critical factor. A hose must reliably contain the internal pressure of the fluid or gas it carries without leaking, bursting, or otherwise failing. The pressure rating of a hose is typically expressed in pounds per square inch (psi) or bars, and it's crucial to select a hose with a safety factor significantly exceeding the expected operating pressure. This accounts for potential pressure surges, fluctuations, and the gradual degradation of the hose material over time.
Factors Affecting Pressure Resistance:
-
Hose Material: The inherent strength and elasticity of the hose material directly impact its pressure resistance. Reinforcing materials such as steel wire, synthetic fibers, and textile braids significantly enhance pressure capabilities. The type and arrangement of these reinforcements are crucial design considerations.
-
Hose Construction: The construction method, including the number of layers, the type of bonding between layers, and the overall diameter, all play a significant role in determining pressure resistance. A multi-layered construction with properly bonded layers offers superior pressure handling capabilities compared to a single-layer design.
-
Hose Diameter: Smaller diameter hoses generally handle higher pressures than larger diameter hoses for the same material and construction. This is due to the reduced surface area subjected to internal pressure.
-
Age and Degradation: Over time, hoses can degrade due to factors such as exposure to sunlight, chemicals, and repeated flexing. This degradation reduces their pressure resistance, making regular inspections and replacements essential for safety.
2. Temperature Extremes: Maintaining Performance Across the Spectrum
Temperature significantly influences the performance of hoses and connections. Extreme heat can cause material softening, weakening, and even melting, while extreme cold can lead to embrittlement and cracking. The temperature range a hose can safely operate within is crucial information that must be considered for any application.
Factors Affecting Temperature Resistance:
-
Hose Material: Different materials exhibit different temperature tolerances. Some materials, such as certain rubbers and plastics, are suitable for high-temperature applications, while others are better suited for low-temperature environments. The selection of the appropriate material is based on the expected temperature fluctuations.
-
Reinforcement Materials: The reinforcement materials within the hose also affect its temperature resistance. Some reinforcements may degrade at high temperatures, compromising the hose's structural integrity.
-
Environmental Factors: Exposure to direct sunlight or other sources of radiant heat can drastically reduce the effective temperature range of a hose.
-
Fluid Temperature: The temperature of the fluid being conveyed also influences the hose's operating temperature range. The hose must be capable of withstanding both the ambient temperature and the fluid temperature.
3. Chemical Compatibility: Preventing Degradation and Leaks
The chemical compatibility of a hose is crucial, especially when transferring corrosive or reactive fluids. Exposure to incompatible chemicals can cause material degradation, swelling, softening, or cracking, leading to leaks and potential safety hazards.
Factors Affecting Chemical Compatibility:
-
Hose Material: Different materials exhibit varying degrees of resistance to different chemicals. Some materials are highly resistant to a wide range of chemicals, while others are susceptible to even mild acids or bases. Selection of the hose material should always be based on the chemical composition of the fluid being conveyed.
-
Chemical Concentration: The concentration of the chemical can significantly impact its effect on the hose material. Even a chemically resistant material may be degraded by highly concentrated solutions.
-
Temperature: Temperature can influence the reactivity of chemicals, potentially increasing their corrosive effect on the hose. High temperatures often accelerate chemical reactions and degradation.
-
Contact Time: Prolonged contact with incompatible chemicals will generally lead to greater material degradation.
Hose Connections: The Critical Link
The integrity of the entire hose system is only as strong as its weakest link—the hose connections. These connections must be able to withstand the same pressures, temperatures, and chemical exposures as the hose itself. Furthermore, they must provide a reliable, leak-free seal.
Types of Hose Connections:
-
Clamps: Clamps provide a secure mechanical connection by compressing the hose onto a fitting. They are widely used due to their simplicity and cost-effectiveness. However, the clamping force must be sufficient to create a leak-proof seal and withstand the operating pressure.
-
Crimped Fittings: Crimped fittings involve a permanent mechanical connection where a metal ferrule is crimped onto the hose, securing it to the fitting. This provides a more robust and reliable connection compared to clamps, particularly for high-pressure applications.
-
Swaged Fittings: Swaged fittings are similar to crimped fittings but use a different method of securing the connection. They typically offer even greater strength and reliability than crimped fittings.
-
Threaded Fittings: Threaded fittings are common in many applications, providing a secure connection through the use of threads. However, proper sealing is critical to prevent leaks.
Factors Affecting Connection Integrity:
-
Fitting Material: The fitting material must be compatible with both the hose material and the conveyed fluid. It should also possess sufficient strength and durability to withstand the expected pressures and temperatures.
-
Sealing Mechanisms: Effective sealing is crucial to prevent leaks. This can be achieved through O-rings, gaskets, or other sealing mechanisms. The correct choice of sealing mechanism depends on the operating pressure, temperature, and fluid compatibility.
-
Installation: Proper installation is essential for the integrity of the hose connection. Incorrect installation can lead to leaks, weakened connections, and potential failures.
-
Maintenance: Regular inspection and maintenance of hose connections are critical for ensuring their continued reliability. Damaged or worn connections should be promptly replaced.
Testing and Standards: Ensuring Quality and Safety
Numerous standards and testing procedures are in place to ensure the quality, reliability, and safety of hoses and hose connections. These procedures involve subjecting the components to rigorous testing under simulated operating conditions. These tests verify that the hoses and fittings meet their specified performance characteristics.
Common Testing Methods:
-
Burst Pressure Test: This test determines the maximum pressure a hose can withstand before bursting. The burst pressure is typically significantly higher than the rated operating pressure to provide a safety margin.
-
Proof Pressure Test: This test involves applying a pressure below the burst pressure to verify the hose's integrity. It helps to identify any weaknesses or leaks.
-
Impulse Pressure Test: This test simulates pressure surges that can occur in certain applications.
-
Fatigue Testing: This test involves repeatedly applying and releasing pressure to simulate the effects of long-term use. It helps to assess the hose's resistance to fatigue failure.
-
Temperature Cycling Tests: These tests subject the hose to repeated temperature changes to assess its resistance to thermal stress.
-
Chemical Resistance Tests: These tests involve exposing the hose to different chemicals to evaluate its compatibility and resistance to degradation.
Selecting the Right Hose: A Critical Decision
The selection of the appropriate hose and hose connection is a crucial decision that must be made based on a thorough understanding of the operating conditions. Failure to select the proper hose can lead to leaks, equipment damage, injury, and environmental contamination. Consideration should be given to the following factors:
- Working Pressure: The maximum expected pressure the hose will encounter.
- Operating Temperature: The expected temperature range.
- Fluid Compatibility: The chemical properties of the conveyed fluid.
- Hose Length and Diameter: The required length and diameter to accommodate the application.
- Environmental Factors: Exposure to sunlight, moisture, and other environmental factors.
- Industry Standards and Regulations: Compliance with relevant industry standards and regulations is crucial.
By carefully considering these factors, and by adhering to established testing and safety standards, it’s possible to select and implement a hose system that will reliably and safely meet the demands of any application, whether it's a simple garden hose or a critical component in a high-pressure industrial process. The longevity and reliability of hoses and hose connections are not merely a matter of convenience; they are essential for ensuring safety, preventing costly downtime, and maintaining the integrity of numerous operations across diverse industries.
Latest Posts
Latest Posts
-
True Or False Professional And Technical Communication Is Research Oriented
Mar 18, 2025
-
Which Best Describes The Terrorist Planning Cycle
Mar 18, 2025
-
Cdl Combination Test Questions And Answers Pdf
Mar 18, 2025
-
Life Insurance Exam Questions And Answers Pdf
Mar 18, 2025
-
The Direct Carry Is Used To Transfer A Patient
Mar 18, 2025
Related Post
Thank you for visiting our website which covers about Hoses And Hose Connections Should Be Able To Withstand . We hope the information provided has been useful to you. Feel free to contact us if you have any questions or need further assistance. See you next time and don't miss to bookmark.