Managers Are Considered Within An Organization Osha
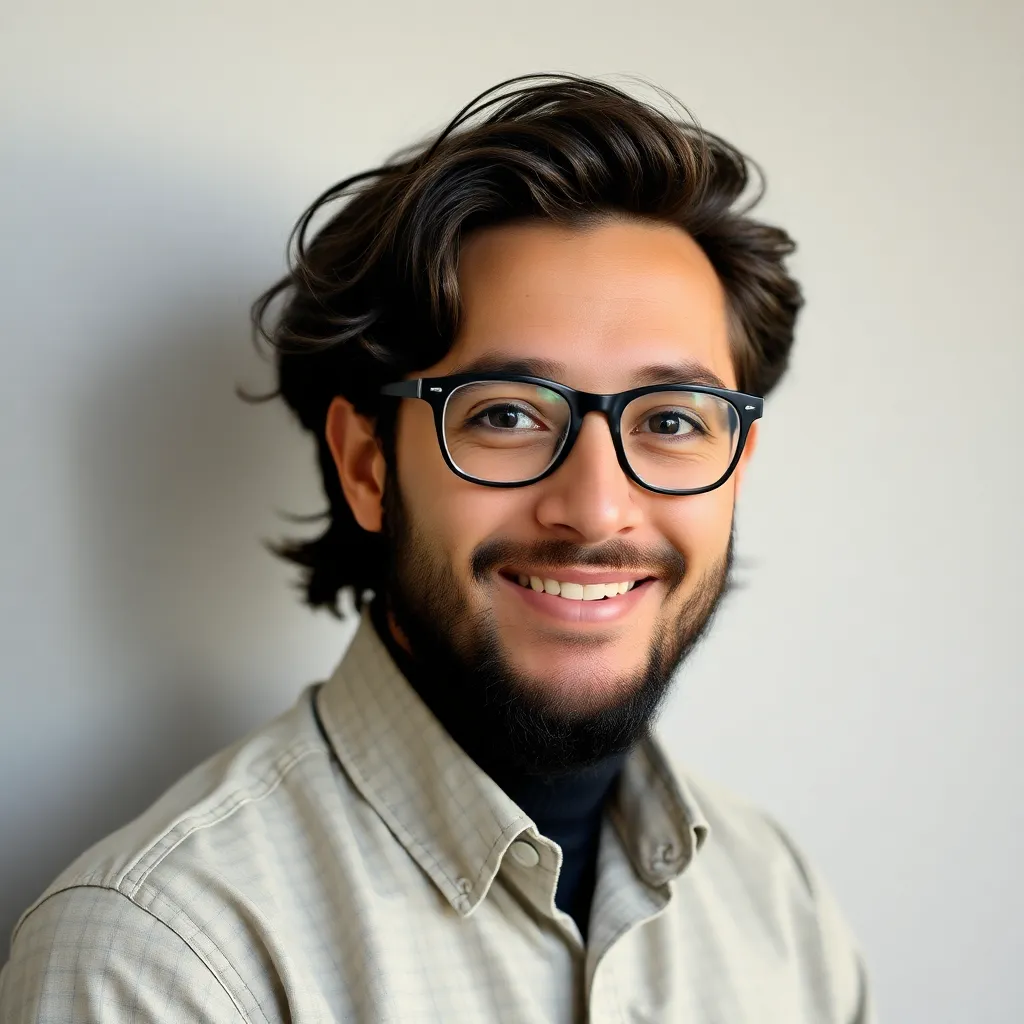
Breaking News Today
Apr 02, 2025 · 7 min read
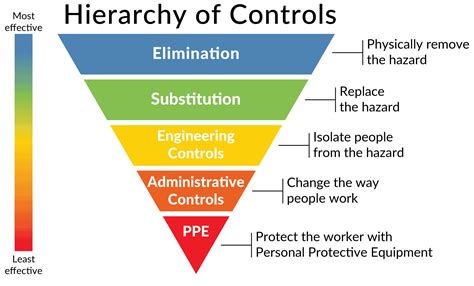
Table of Contents
Managers: The Crucial Link in OSHA Compliance within an Organization
Managers play a pivotal role in ensuring Occupational Safety and Health Administration (OSHA) compliance within any organization. They are not simply figureheads; they are the frontline implementers of safety policies, the trainers of employees, and the investigators of incidents. Their understanding of OSHA regulations, their commitment to safety, and their proactive approach directly impact the safety culture of the workplace and the organization's overall success in avoiding costly accidents, fines, and reputational damage. This article delves deep into the responsibilities, challenges, and best practices for managers in navigating the complex landscape of OSHA compliance.
The Managerial Role in OSHA Compliance: Beyond Policy Enforcement
OSHA compliance isn't solely about posting regulations or conducting annual safety training. It's a holistic approach that permeates every aspect of the work environment. Managers are at the heart of this process, acting as the crucial link between overarching safety policies and their practical application on the ground. Their responsibilities extend beyond simply enforcing rules; they encompass leadership, training, proactive hazard identification, and fostering a culture of safety.
1. Proactive Hazard Identification and Risk Assessment: A Manager's Duty
Effective OSHA compliance begins with proactive hazard identification. Managers must conduct regular workplace inspections, not just cursory walkthroughs. This involves systematically identifying potential hazards, assessing their risks, and implementing control measures to mitigate those risks. This requires a thorough understanding of the specific hazards associated with their department or team's work. For example, a manager in a construction company needs a different skillset and knowledge base than a manager in a software development firm.
Examples of proactive hazard identification:
- Regular safety inspections: Scheduled and unscheduled inspections to identify potential hazards, including ergonomic issues, trip hazards, fire hazards, electrical hazards, and chemical exposures.
- Job hazard analysis (JHA): A systematic process of identifying and evaluating hazards associated with specific tasks.
- Incident investigation: Thoroughly investigating all incidents, near misses, and accidents to understand the root causes and prevent recurrence.
- Employee feedback: Actively soliciting feedback from employees about safety concerns and potential hazards.
2. Training and Education: Empowering Employees for Safety
Managers are responsible for ensuring their employees receive adequate safety training. This training must be relevant, comprehensive, and tailored to the specific hazards present in their workplace. Furthermore, training shouldn't be a one-off event; it should be ongoing and reinforced through regular updates, refresher courses, and ongoing communication.
Effective safety training elements:
- Hazard-specific training: Training that addresses the specific hazards associated with the employee's job.
- Emergency response training: Training on how to respond to emergencies, including fire, evacuations, and first aid.
- Personal protective equipment (PPE) training: Training on how to properly select, use, and maintain PPE.
- Regular reinforcement: Reinforcing safety procedures through regular communication, toolbox talks, and safety meetings.
3. Enforcing Safety Policies and Procedures: Leading by Example
Managers are responsible for ensuring that safety policies and procedures are followed consistently. This involves not only enforcing rules but also providing clear explanations for why they're necessary and modeling safe behavior themselves. Inconsistency from managers sends a confusing message and undermines the effectiveness of the entire safety program.
Strategies for effective enforcement:
- Clear communication: Communicating safety policies and procedures clearly and consistently to all employees.
- Consistent enforcement: Consistently enforcing safety rules, regardless of the employee's position or seniority.
- Positive reinforcement: Recognizing and rewarding employees for safe behavior.
- Progressive discipline: Using progressive discipline to address safety violations, starting with warnings and escalating to more severe measures as necessary.
4. Documentation and Record Keeping: A Critical Component of Compliance
Maintaining accurate and comprehensive records is crucial for demonstrating OSHA compliance. Managers are responsible for documenting safety training, inspections, incident investigations, and other safety-related activities. This documentation is essential for demonstrating compliance during OSHA inspections and for identifying areas for improvement in the safety program.
Essential documentation:
- Safety training records: Records of all safety training provided to employees.
- Inspection records: Records of all workplace inspections, including identified hazards and corrective actions.
- Incident investigation reports: Reports on all incidents, near misses, and accidents.
- Emergency response plans: A detailed plan for responding to emergencies.
The Challenges Managers Face in Ensuring OSHA Compliance
While the role of a manager in OSHA compliance is crucial, it’s not without its challenges. These can range from practical limitations to inherent human factors that influence safety practices within the workplace.
1. Balancing Safety with Productivity: A Delicate Act
One of the biggest challenges managers face is balancing safety with productivity. Implementing strict safety measures can sometimes slow down work processes. However, the costs associated with workplace accidents—lost productivity, medical expenses, legal fees, and damage to reputation—far outweigh any temporary slowdown caused by prioritizing safety. Managers must find a way to integrate safety into the workflow seamlessly, making it an integral part of the production process rather than an obstacle.
2. Dealing with Employee Resistance to Safety Procedures: Fostering a Culture of Safety
Some employees may resist safety procedures, either out of laziness, impatience, or a lack of understanding. Managers must effectively address this resistance by fostering a culture of safety where employees understand the importance of safety procedures and are empowered to speak up about safety concerns without fear of reprisal. This requires open communication, consistent reinforcement, and positive reinforcement of safe behaviors.
3. Keeping Up with Evolving OSHA Regulations: Continuous Learning
OSHA regulations are constantly evolving. Managers must stay abreast of these changes to ensure their organization's compliance. This requires ongoing training and access to updated resources. Failing to keep up with regulations can lead to fines, penalties, and legal issues.
4. Resource Constraints: Balancing Budget and Safety
Implementing robust safety programs requires resources, both financial and human. Managers may face budget constraints that limit their ability to implement all necessary safety measures. They need to prioritize safety initiatives strategically, focusing on the most critical hazards and seeking creative solutions to overcome resource limitations.
Best Practices for Managers in OSHA Compliance
Successful OSHA compliance requires a proactive and multifaceted approach. Managers who adopt the following best practices significantly improve their chances of creating a safe and compliant workplace.
1. Lead by Example: Demonstrating Commitment to Safety
The most effective way for managers to promote safety is to lead by example. They must consistently follow safety procedures themselves and demonstrate a genuine commitment to safety in their actions and words. This sets the tone for the entire team and encourages employees to follow suit.
2. Empower Employees: Encouraging Proactive Participation
Managers should empower their employees to participate actively in safety initiatives. This includes soliciting feedback, involving them in safety inspections and training, and encouraging them to report safety hazards without fear of reprisal. A collaborative approach fosters a stronger safety culture.
3. Invest in Ongoing Training: Continuous Improvement
Investing in ongoing safety training is crucial. This isn't just about initial compliance training; it's about providing regular updates, refresher courses, and specialized training as needed. This ensures that employees stay informed about the latest safety procedures and technologies.
4. Regularly Review and Update Safety Policies: Adaptability and Proactiveness
Safety policies and procedures should be reviewed and updated regularly to reflect changes in the workplace, technology, and OSHA regulations. Regular review ensures that the safety program remains relevant and effective.
5. Thorough Documentation: A Cornerstone of Compliance
Meticulous documentation is essential. Maintaining accurate records of safety training, inspections, incidents, and corrective actions is crucial for demonstrating compliance during OSHA inspections.
Conclusion: Managers as Guardians of Workplace Safety
Managers are the linchpin of OSHA compliance within an organization. Their responsibilities extend far beyond simply enforcing regulations; they encompass leadership, training, proactive hazard identification, and fostering a safety-conscious culture. By embracing proactive safety measures, empowering employees, and staying abreast of evolving regulations, managers can create a workplace where safety is not just a priority but a fundamental value, leading to a more productive, efficient, and ultimately, safer work environment. The investment in time, resources, and training pays dividends in reduced accidents, improved employee morale, and sustained compliance with OSHA regulations. Ignoring this responsibility, however, can lead to devastating consequences, impacting both the organization and its employees.
Latest Posts
Latest Posts
-
Correctly Label The Intrinsic Muscles Of The Hand
Apr 03, 2025
-
An Underwriter Determines That An Applicants Risk
Apr 03, 2025
-
Signs Of A Pulmonary Blast Injury Include
Apr 03, 2025
-
Wild Animals Are Not Considered A Natural Resource
Apr 03, 2025
-
What Communication Strategies Contribute To Providing Successful
Apr 03, 2025
Related Post
Thank you for visiting our website which covers about Managers Are Considered Within An Organization Osha . We hope the information provided has been useful to you. Feel free to contact us if you have any questions or need further assistance. See you next time and don't miss to bookmark.