The Lean Philosophy Suggests That Workers Are
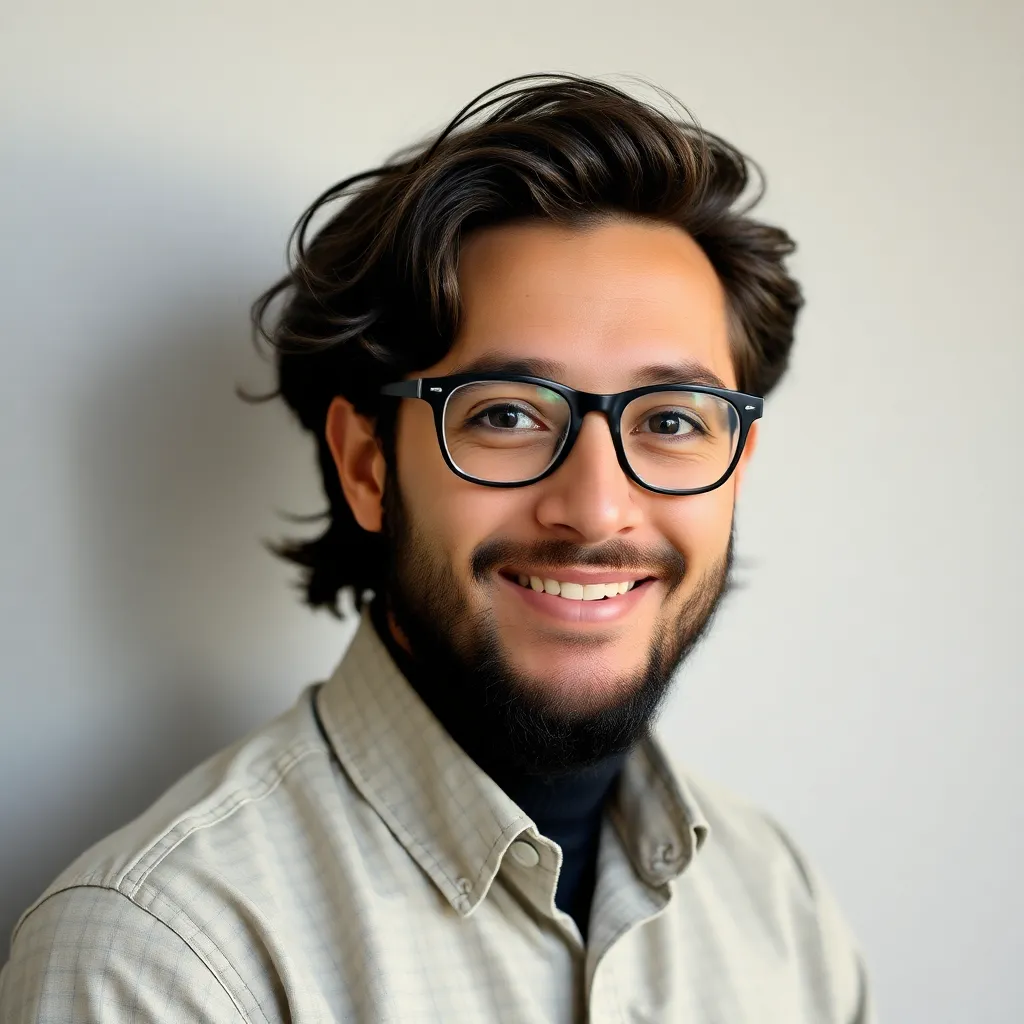
Breaking News Today
Mar 29, 2025 · 6 min read
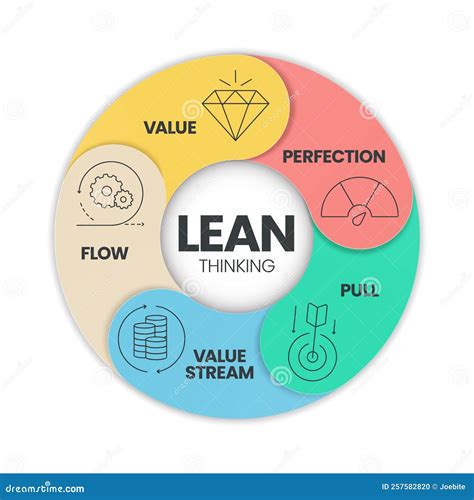
Table of Contents
- The Lean Philosophy Suggests That Workers Are
- Table of Contents
- The Lean Philosophy Suggests That Workers Are…Empowered Problem-Solvers
- Beyond the Assembly Line: Redefining the Role of the Worker
- 1. Empowerment and Autonomy: The Key to Engagement
- 2. Respect for People: A Foundation of Lean
- 3. Problem-Solving as a Core Competency
- The Organizational Impact of Empowering Workers
- 1. Flatter Hierarchies and Decentralized Decision-Making
- 2. Increased Teamwork and Collaboration
- 3. A Culture of Continuous Improvement
- 4. Enhanced Employee Engagement and Retention
- Measuring the Success: Tangible Benefits of the Lean Approach
- 1. Increased Productivity and Efficiency
- 2. Improved Quality
- 3. Reduced Costs
- 4. Increased Customer Satisfaction
- 5. Enhanced Innovation and Creativity
- 6. Improved Safety
- Conclusion: Lean and the Future of Work
- Latest Posts
- Latest Posts
- Related Post
The Lean Philosophy Suggests That Workers Are…Empowered Problem-Solvers
The Lean philosophy, often associated with manufacturing, is far more than just a set of tools and techniques. At its core, Lean is a management philosophy that centers on respect for people and a relentless pursuit of eliminating waste to deliver maximum value to the customer. This inherently implies a particular view of workers, one that moves far beyond the traditional model of simply executing pre-defined tasks. Lean suggests that workers are, in fact, empowered problem-solvers who are essential to the continuous improvement process. This article will delve deep into this crucial aspect of Lean, exploring how this philosophy views workers, the implications for organizational structure and culture, and the resulting benefits.
Beyond the Assembly Line: Redefining the Role of the Worker
Traditional manufacturing often viewed workers as cogs in a machine, responsible for performing repetitive tasks with minimal input or autonomy. Lean fundamentally challenges this perspective. Instead of passive executors, Lean sees workers as active participants in the value creation process. Their knowledge, skills, and experience are considered invaluable assets, not just operational costs. This shift in perspective underpins several key principles:
1. Empowerment and Autonomy: The Key to Engagement
Lean empowers workers by giving them the authority and responsibility to identify and solve problems. This contrasts sharply with hierarchical structures where decision-making is concentrated at the top. In a Lean environment, workers are encouraged to:
- Identify waste: They are trained to recognize various forms of waste (muda) – defects, overproduction, waiting, transportation, inventory, motion, and over-processing – and suggest improvements.
- Implement solutions: They are given the tools and support to implement their solutions, fostering a sense of ownership and accountability.
- Continuously improve: They participate actively in continuous improvement initiatives (Kaizen), sharing their insights and contributing to the overall efficiency and effectiveness of the organization.
This empowerment fosters a sense of ownership and pride in the work, leading to increased engagement and motivation. Workers are no longer simply fulfilling tasks; they are actively contributing to the success of the organization.
2. Respect for People: A Foundation of Lean
The very foundation of Lean rests on the principle of respect for people. This means valuing the contributions of every individual, recognizing their inherent potential, and creating a work environment that fosters their growth and development. This respect manifests in several ways:
- Training and Development: Lean organizations invest heavily in training and development programs to equip workers with the skills and knowledge needed to contribute effectively. This includes training on Lean principles, problem-solving techniques, and process improvement methodologies.
- Cross-functional Collaboration: Lean encourages cross-functional collaboration, breaking down silos and promoting teamwork. Workers from different departments are encouraged to share ideas and work together to solve problems.
- Open Communication: Open and transparent communication is crucial in a Lean environment. Workers are encouraged to share their ideas and concerns without fear of retribution. This creates a culture of trust and collaboration.
By respecting the contributions of each worker, Lean organizations create a positive and supportive work environment that enhances productivity and innovation.
3. Problem-Solving as a Core Competency
Lean emphasizes problem-solving as a core competency for all workers. This isn't limited to engineers or managers; it's expected of everyone. The philosophy equips workers with the tools and techniques to identify, analyze, and solve problems effectively.
- 5S Methodology: 5S (Sort, Set in Order, Shine, Standardize, Sustain) is a foundational Lean technique that improves workplace organization and efficiency. Workers are actively involved in implementing and maintaining 5S.
- Kaizen Events: Kaizen events, or focused improvement projects, involve teams of workers working together to identify and solve problems in a specific area. These events provide valuable hands-on experience in problem-solving.
- Value Stream Mapping: Value stream mapping is a visual tool used to identify and eliminate waste in a process. Workers are often involved in creating and updating value stream maps, providing crucial insights into the process.
By fostering a culture of problem-solving, Lean organizations empower workers to take ownership of their work and continuously improve processes.
The Organizational Impact of Empowering Workers
The Lean philosophy's view of workers has profound implications for organizational structure and culture:
1. Flatter Hierarchies and Decentralized Decision-Making
Lean organizations tend to have flatter hierarchies with decentralized decision-making. Empowering workers means giving them the authority to make decisions at the point of work, reducing the need for layers of management. This speeds up problem-solving and decision-making processes.
2. Increased Teamwork and Collaboration
Lean fosters a culture of teamwork and collaboration. Workers are encouraged to share ideas, collaborate on problem-solving, and support each other. This collaborative approach leads to increased innovation and efficiency.
3. A Culture of Continuous Improvement
Lean creates a culture of continuous improvement (Kaizen). Workers are actively involved in identifying and eliminating waste, leading to ongoing improvements in processes and products. This continuous improvement mindset leads to increased productivity and competitiveness.
4. Enhanced Employee Engagement and Retention
By valuing workers' contributions and providing them with autonomy and opportunities for growth, Lean organizations enhance employee engagement and retention. Employees are more likely to be motivated and committed when they feel valued and empowered.
Measuring the Success: Tangible Benefits of the Lean Approach
The Lean philosophy's focus on empowering workers yields significant tangible benefits:
1. Increased Productivity and Efficiency
By eliminating waste and streamlining processes, Lean organizations achieve significant improvements in productivity and efficiency. Empowered workers are more likely to identify and eliminate inefficiencies, leading to increased output with fewer resources.
2. Improved Quality
Lean emphasizes defect prevention and continuous improvement, resulting in improved product and service quality. Empowered workers are more likely to identify and address quality issues promptly, reducing defects and improving customer satisfaction.
3. Reduced Costs
By eliminating waste and improving efficiency, Lean organizations significantly reduce costs. This includes reduced material costs, labor costs, and overhead costs.
4. Increased Customer Satisfaction
Improved quality, faster delivery times, and lower costs all contribute to increased customer satisfaction. Lean organizations are better positioned to meet customer needs and exceed their expectations.
5. Enhanced Innovation and Creativity
Empowered workers are more likely to be innovative and creative. When given the authority to make decisions and implement changes, they are more likely to come up with new ideas and solutions.
6. Improved Safety
Lean emphasizes a safe work environment, and empowered workers are more likely to identify and report safety hazards, leading to improved safety performance.
Conclusion: Lean and the Future of Work
The Lean philosophy's view of workers is revolutionary. It challenges traditional management models that view workers as mere cogs in a machine and instead positions them as key drivers of innovation, efficiency, and organizational success. By empowering workers, fostering a culture of respect, and emphasizing continuous improvement, Lean organizations create a work environment where everyone can thrive. This approach is not just a trend; it's a fundamental shift in how we think about work and the role of the individual within an organization. In the future of work, the organizations that embrace this philosophy will be the ones best positioned to succeed. The Lean philosophy is a testament to the fact that investing in people is the best investment any organization can make. It's a philosophy that unlocks human potential and transforms organizations from the inside out. The empowered worker, therefore, is not just a theoretical concept but the cornerstone of a sustainable and thriving business.
Latest Posts
Latest Posts
-
Cellulose And Starch Are Examples Of Quizlet
Apr 01, 2025
-
What Type Of Information Does This Personnel Roster Represent
Apr 01, 2025
-
A Patient Has Been Exposed To Meningococcal Meningitis Quizlet
Apr 01, 2025
-
Development Of Coronary Heart Disease Is Related To Quizlet
Apr 01, 2025
-
A Cost Of Living Adjustment Is Based On The Quizlet
Apr 01, 2025
Related Post
Thank you for visiting our website which covers about The Lean Philosophy Suggests That Workers Are . We hope the information provided has been useful to you. Feel free to contact us if you have any questions or need further assistance. See you next time and don't miss to bookmark.