Which Is Not A Cost Of Quality
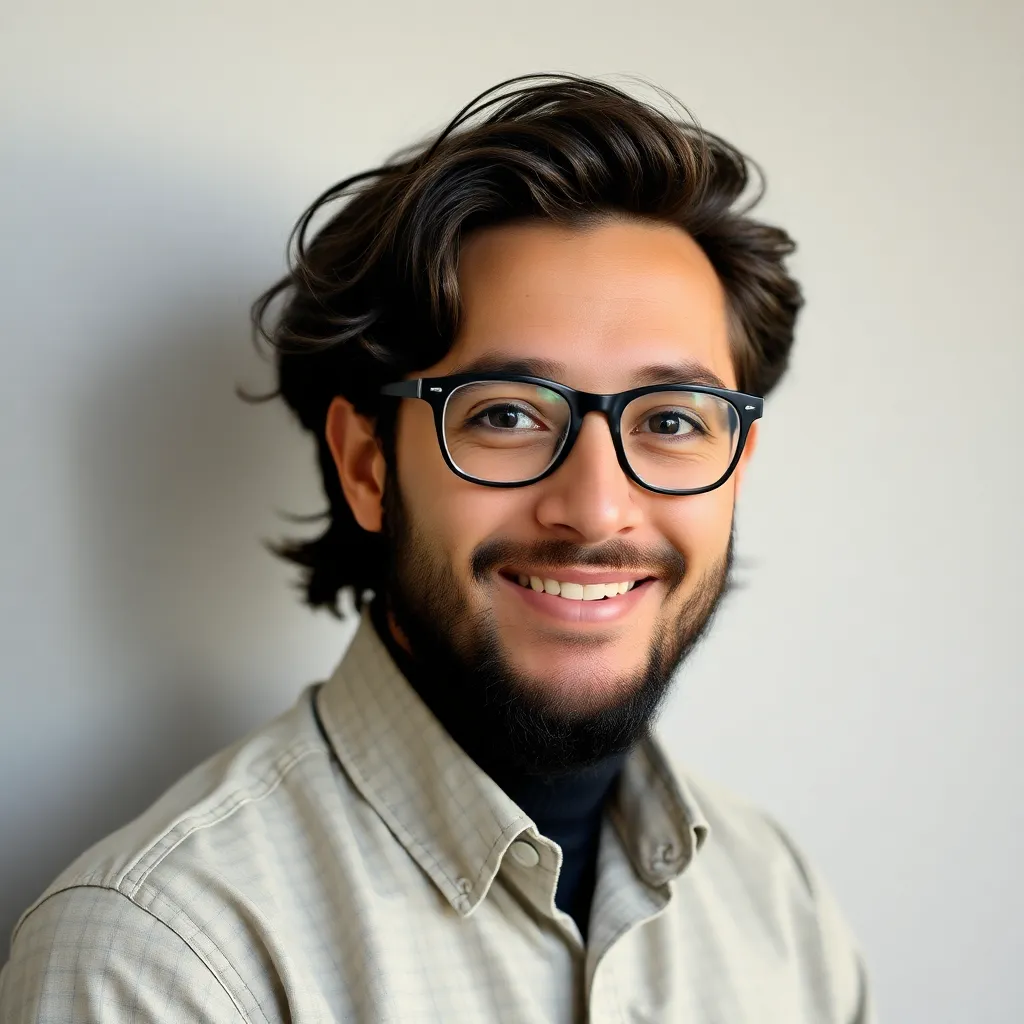
Breaking News Today
Mar 29, 2025 · 5 min read
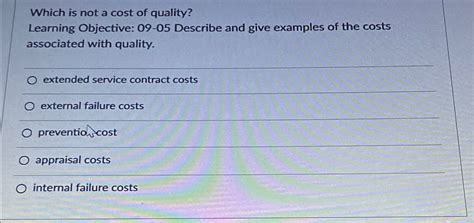
Table of Contents
- Which Is Not A Cost Of Quality
- Table of Contents
- Which is NOT a Cost of Quality? Understanding the True Financial Impact of Quality Management
- What Is a Cost of Quality?
- 1. Prevention Costs:
- 2. Appraisal Costs:
- 3. Internal Failure Costs:
- 4. External Failure Costs:
- What is NOT a Cost of Quality?
- 1. Investment in Quality Management Systems:
- 2. Research and Development (R&D) Costs:
- 3. Marketing and Sales Expenses:
- 4. General and Administrative Expenses:
- 5. Employee Salaries (Unless Directly Related to Quality Improvement):
- 6. Routine Maintenance and Upkeep:
- The Importance of Understanding COQ
- Conclusion: Beyond the Numbers
- Latest Posts
- Latest Posts
- Related Post
Which is NOT a Cost of Quality? Understanding the True Financial Impact of Quality Management
Quality management is paramount for any successful business. However, many misunderstand the concept of "cost of quality" (COQ), often assuming it represents all expenses related to quality. This is a crucial misconception. The cost of quality encompasses specific categories of expenses incurred due to poor quality, not all expenses related to quality initiatives. This article delves deep into the nuances of COQ, exploring what is not included, and illustrating how a holistic understanding can significantly improve your bottom line.
What Is a Cost of Quality?
Before understanding what isn't, it's vital to define what constitutes a cost of quality. COQ categorizes expenses arising from defects, failures, and inefficiencies related to poor quality. These costs are broadly classified into four categories:
1. Prevention Costs:
These are proactive costs incurred to prevent defects from occurring in the first place. Think of it as an investment in quality, rather than a cost of failure. Examples include:
- Quality planning: Developing comprehensive quality plans and procedures.
- New product review: Thoroughly evaluating new products before launch.
- Supplier quality rating: Evaluating and selecting reliable suppliers.
- Training: Educating employees on quality procedures and best practices.
- Process improvement: Implementing tools and techniques (like Six Sigma or Lean) to optimize processes.
- Quality audits: Regular audits to ensure processes meet standards.
2. Appraisal Costs:
These are costs incurred to detect defects. They involve assessing the quality of products or services. Examples include:
- Inspection: Checking products at various stages of production.
- Testing: Conducting thorough tests to ensure product functionality and performance.
- Calibration: Ensuring measurement instruments are accurate.
- Statistical process control: Monitoring processes to identify deviations.
- Quality audits: (Yes, some aspects of audits fall under both prevention and appraisal)
3. Internal Failure Costs:
These are costs associated with defects discovered before the product or service reaches the customer. Identifying and rectifying these issues internally is crucial. Examples include:
- Scrap: Discarding defective products.
- Rework: Correcting defects in products or services.
- Downtime: Production downtime due to quality issues.
- Inventory adjustments: Correcting discrepancies in stock due to errors.
- Internal failure analysis: Investigating the root causes of internal failures.
4. External Failure Costs:
These are the most damaging costs, representing the expenses related to defects discovered after the product or service reaches the customer. These costs can significantly impact reputation and customer loyalty. Examples include:
- Warranty claims: Repairing or replacing defective products under warranty.
- Product returns: Handling returned products due to defects.
- Complaints: Addressing customer complaints and resolving issues.
- Legal actions: Costs related to lawsuits or legal battles due to product defects.
- Lost sales: Loss of future sales due to negative reputation and word-of-mouth.
- Product recalls: Recalling defective products from the market.
What is NOT a Cost of Quality?
Now, let's address the core of the article: what expenses are not considered part of the cost of quality? The key is to understand that COQ focuses on the negative financial consequences of poor quality, not all expenses related to improving or maintaining quality. Therefore, the following are generally not included in COQ:
1. Investment in Quality Management Systems:
Implementing robust quality management systems (like ISO 9001) is a significant investment, but it's considered a strategic business decision aimed at preventing future problems. While the initial costs are substantial, they aren't directly linked to existing defects. Think of it as investing in infrastructure to prevent future losses, not repairing current damage.
2. Research and Development (R&D) Costs:
R&D expenses are focused on creating new products and improving existing ones. Although this indirectly contributes to quality, the costs themselves are not directly tied to fixing defects or failures. They are investments in future product quality and innovation.
3. Marketing and Sales Expenses:
These are essential for reaching customers, but are separate from the costs related to fixing defective products or addressing customer complaints arising from poor quality. Marketing focuses on promoting the product; COQ focuses on the consequences of product failure.
4. General and Administrative Expenses:
These are overhead costs associated with running a business (rent, salaries, utilities, etc.). While a portion may be indirectly related to quality functions, the bulk of these expenses are not directly tied to defect prevention or remediation.
5. Employee Salaries (Unless Directly Related to Quality Improvement):
Salaries for employees whose sole role is dedicated to improving quality (quality engineers, quality control inspectors) are generally categorized under Prevention or Appraisal Costs. However, general employee salaries across the company are not considered COQ.
6. Routine Maintenance and Upkeep:
Regular maintenance and upkeep are essential for ensuring the smooth functioning of equipment and processes. These costs prevent major breakdowns, but aren't considered COQ as they don't directly relate to fixing defects resulting from poor quality. They are preventative maintenance, aimed at avoiding potential failures, not fixing existing ones.
The Importance of Understanding COQ
Accurately identifying and classifying COQ provides crucial insights into a company's financial health and operational efficiency. A clear understanding helps in:
- Improving profitability: By identifying and reducing the costs associated with poor quality, businesses can significantly improve their profitability.
- Enhancing customer satisfaction: Reducing external failure costs leads to happier customers and improved brand reputation.
- Improving operational efficiency: Focusing on prevention and appraisal costs leads to more efficient processes and fewer defects.
- Making informed business decisions: Understanding COQ helps make informed decisions about investments in quality management.
- Benchmarking against competitors: Tracking COQ allows businesses to benchmark their performance against competitors and identify areas for improvement.
Conclusion: Beyond the Numbers
The cost of quality is more than just a financial metric; it reflects the overall health of an organization's commitment to excellence. While calculating COQ requires a diligent approach to data collection and categorization, understanding what isn't included is equally crucial. This nuanced understanding allows for a more accurate picture, enabling businesses to invest wisely in quality initiatives that not only prevent financial losses but also build a stronger, more resilient, and ultimately more successful organization. By focusing on preventing defects rather than solely reacting to them, businesses can significantly shift their financial trajectory, fostering sustainable growth and customer loyalty. The true value of understanding COQ lies not just in the numbers, but in the strategic decisions it informs, ultimately shaping a culture of quality that permeates every facet of the business.
Latest Posts
Latest Posts
-
To Achieve A High Standard Of Living A Nation Should
Apr 01, 2025
-
Huipil Es Una De Las Ciudades Mas Importantes De Guatemala
Apr 01, 2025
-
In Sample And Out Of Sample Criteria Are Based On The Forecast
Apr 01, 2025
-
Select The Five Major Mechanisms Of Antimicrobial Resistance
Apr 01, 2025
-
After Determining That Someone Has Had Too Much To Drink
Apr 01, 2025
Related Post
Thank you for visiting our website which covers about Which Is Not A Cost Of Quality . We hope the information provided has been useful to you. Feel free to contact us if you have any questions or need further assistance. See you next time and don't miss to bookmark.